In order to increase production efficiency, such solutions as process mapping could prove beneficial. The method is based on a graphical representation of activities performed by a company, allowing for better control of day-to-day activities. How is mapping conducted and what are its advantages?
What is process mapping?
Production process mapping is a graphical representation of all the steps and operations performed in a given facility that are needed to produce the final product. Additional information regarding data, correlations and instructions is also included. The main idea is to clearly present the next steps required to achieve a goal, which translates into more efficient management.
How does the process map work in a company?
Creating a process map is particularly important in the manufacturing sector, where efficiency is almost always a priority. It is a solution that will work for both new companies and businesses that have been on the market for a long time. Process mapping can be implemented regardless of the scale of operations or the volume of products being prepared. Here are some of the benefits you can expect:
- Understanding how the process works – this allows even new employees to quickly and seamlessly integrate into the tasks at hand, which means an increase in productivity, as well as a faster return on investment in recruitment.
- More efficient communication between employees and departments – access to clear information maintained in a consistent format greatly improves the flow of data within the company. This, in turn, not only reduces the amount of time required for employee training, but also allows for quick and efficient assignment of selected tasks to the right people.
- Reduced risk of errors – process mapping allows you to determine all elements of production, which reduces the risk of overlooking important elements.
- Swift identification of areas requiring improvement – ongoing insight into the operation and requirements of individual stages allows you to easily identify which areas require changes. This makes it possible, among other things, to reduce losses during production and maintain high productivity.
Process map – how to make a proper plan?
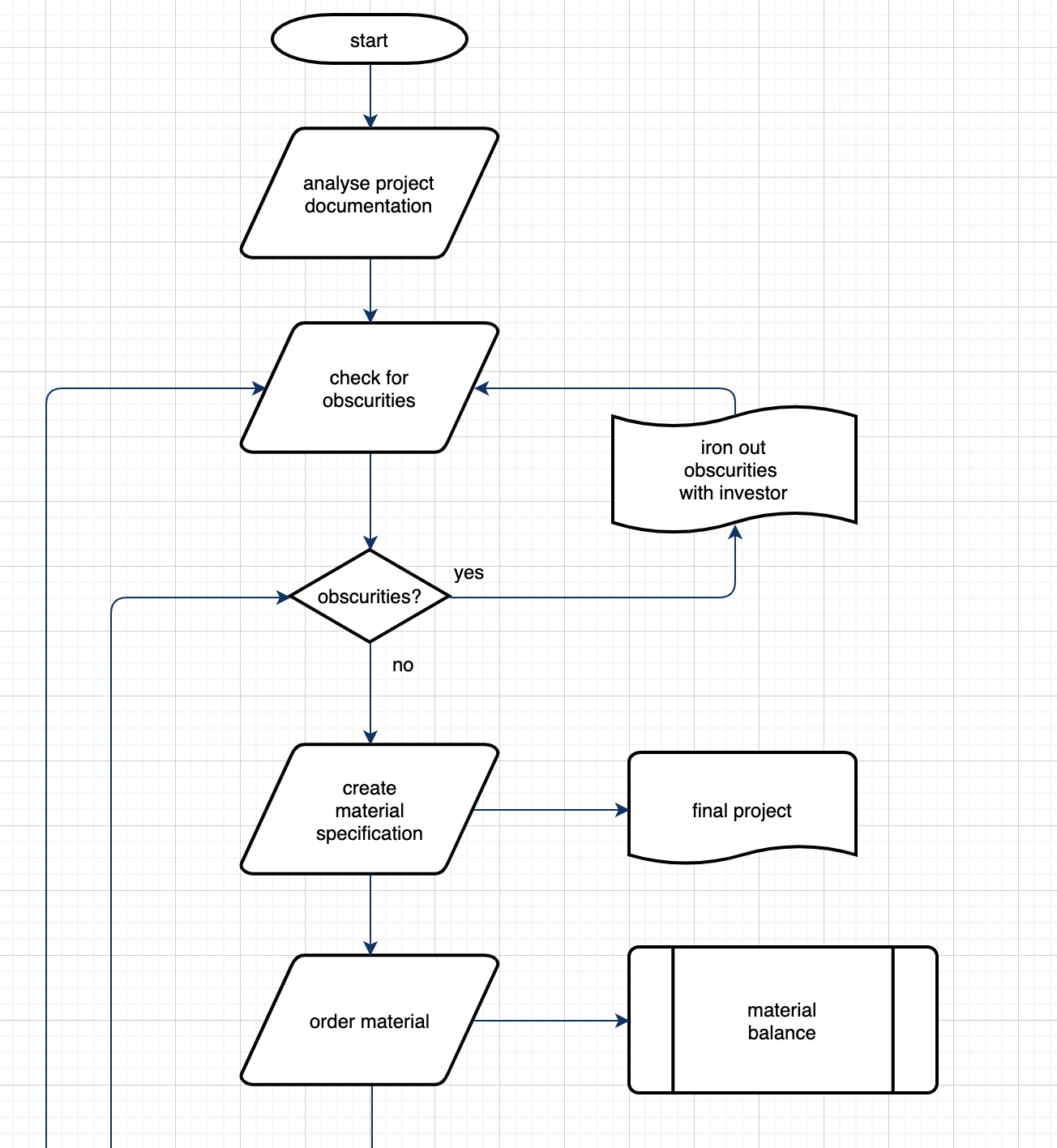
Creating a process map must, first of all, be as clear as possible when presenting the various steps, stages and requirements. To begin with, it is necessary to define the starting point from which you move on to subsequent tasks. Importantly, each element of the map should be named and labeled so that all employees know what they are responsible for and how each part of the process works.
There are several methods of depicting production processes:
- Process diagram – a graphical representation that runs from top to bottom. The top is the start, and the bottom is the end of the process. Between them are placed the individual steps needed to achieve the goal.
- Flow diagram – in this case, the enterprise process map is arranged from left to right. If specific steps need to be developed, you can additionally use horizontal positions.
- VSM (value stream mapping) – this is the term for process mapping methods derived from lean management ideology. Here, the main role is played not by the processes themselves, but by the flow of value within the activities carried out by the company.
See also: How to implement key lean manufacturing methods?
Process mapping – symbols
Process mapping is a task related to the graphical representation of activities – therefore, symbols play a very important role. Through those symbols, it is possible to determine the type of a given task or production stage. Most often a specific scheme is used, in which individual shapes have specific meanings:
- rectangle – operations;
- rhombus – decisions and tests;
- parallelogram – input and output data;
- arrows – direction of action;
- circle – link between map pages;
- triangle – storage or archiving;
- hexagon – checks, verifications and measurements.
Production process mapping – an example from the automotive industry
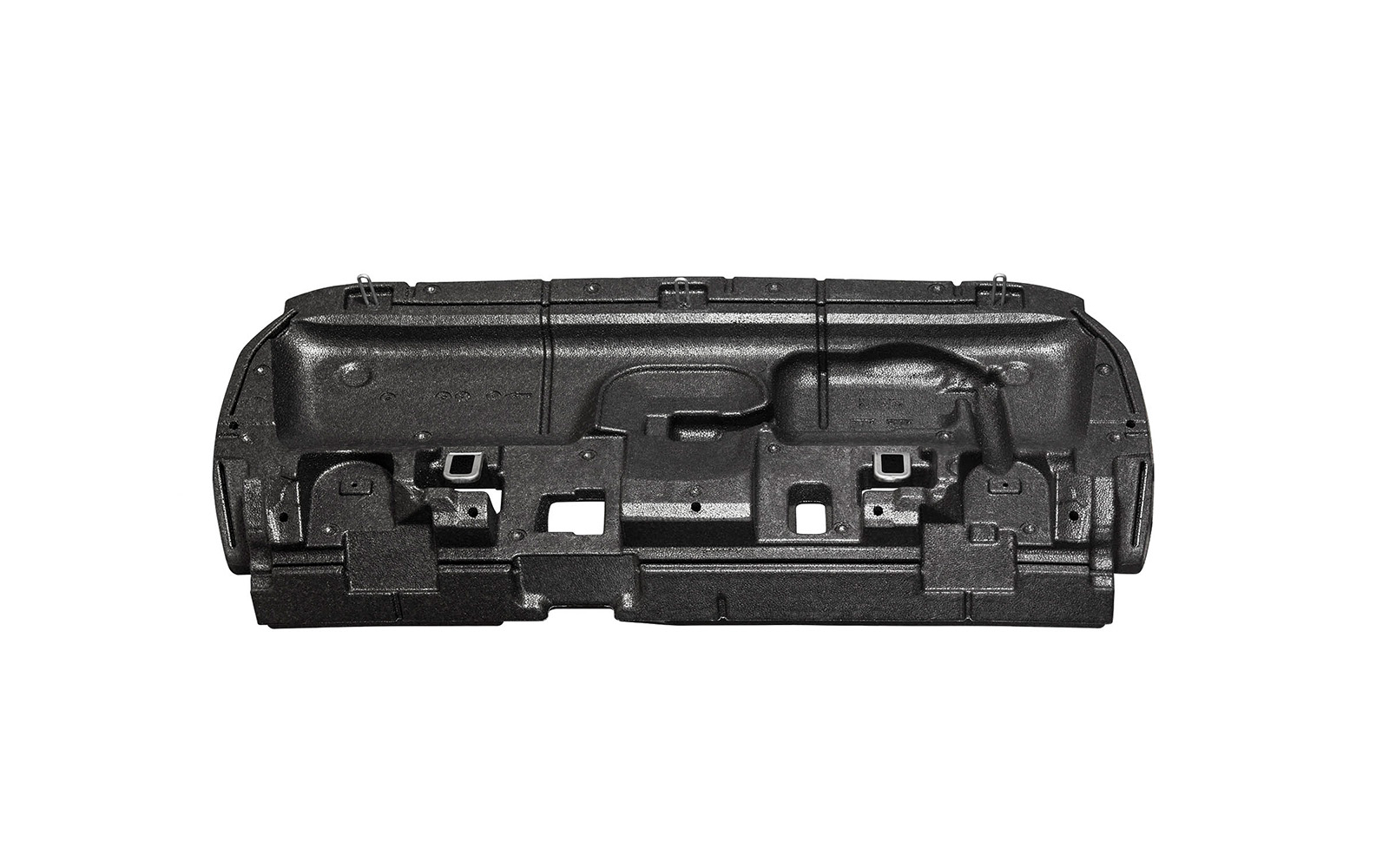
To understand how production process mapping works, it is useful to look at examples. Such solutions are used, among others, in the automotive industry, where maintaining high productivity is a key goal of virtually every company. How does process mapping work in this case? As an example, consider car seats made of foamed polypropylene. These are products with many interrelated operations and tasks to consider. For starters, you will need to procure material for production, which must also go hand in hand with quality control. At this point, two process routes can be separated – storage of waste and storage of finished material. Prepared polypropylene must be delivered to the production hall, to a designated location and a specific machine. After that, all the activities that determine the result of the production, i.e. the shape of a particular product, its size and adaptation to a specific model, are taken into account.
After preparation, the car seats are also subjected to quality control. Once again, two routes are available – either waste storage or preparation of the model for the customer. Next, packaging, storage and transportation are taken into account. The process map of a manufacturing company can be more or less detailed, depending on your needs – you can often find an approach based on creating several maps for different departments.
To learn more about manufacturing efficiency in the automotive industry, we invite you to contact Knauf Automotive and take advantage of our offer of car components.