The basic function of packaging in the logistics is first of all to protect the cargo. Its durability, sturdiness and also the properties that allow to maintain the parameters of transported products or raw materials exert considerable influence on reliability and quality of supplies. However, the optimal selection of packaging has much wider meaning, which extends also on the production and logistics processes within the production plant.
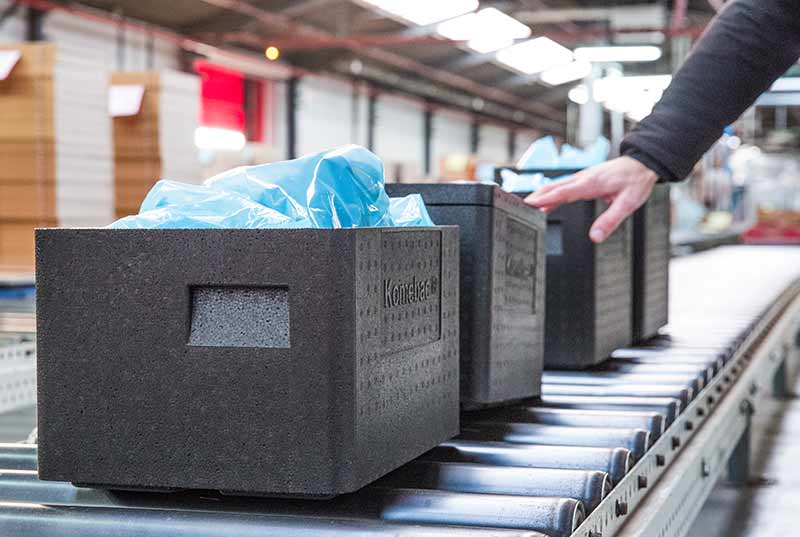
RELIABILITY AND OPTIMIZATION IN LOGISTICS thanks to packaging
The guarantee that the cargo will be supplied on time and intact is the key issue, especially in the automotive branch where lead times are short and quality standards are very high. This effect cannot be accomplished without diligent logistic planning with consideration of all processes, both the processes that take place inside as well as outside of the company. Packaging selected in a right way is the basic link of the whole logistics chain. It plays many functions on each phase of the chain, from the production line down to the supply to the customer and storage. Thus its shape, dimensions, material or functionalities must be adjusted not only to the contents but also to the specific conditions of the particular production line, way of transport and logistics processes in the plant. At present in the business trade between the automotive branch companies plastic containers are most frequently used, however, very light, single material containers made from expanded polypropylene have become a more attractive alternative.
Kinds and functions of packaging in the production and transport logistics
There are many kinds of logistic packaging. The most frequently used criterion of its division is the material, from which it has been produced. In general you can distinguish packaging made from wood, steel, cardboard or mixed. Whereas due to the construction you can distinguish chests, containers, baskets or boxes. Each time the type of packaging is adjusted to the kind of its contents, because its principal and basic function is protection of the cargo. The remaining functions may comprise:
- Informing about the kind of the contents,
- Handling function, i.e. transfer and storage,
- Recycling function.
In the automotive branch the most frequent kind of the cargo are small components, which require packaging, which is durable, capacious and closed in a relevant way, facilitating the logistics in the production processes. The common standard has already become reusable packaging, as it is more economical and practical than e.g. cardboard boxes.
Also it allows for better protection of the contents. Moreover, it facilitates the management of the packaging, among other things eliminating the problem of the packaging wastes. An important factor in transport is also weight of the load, which influences fuel consumption and transport costs. In the automotive branch, as well as in other industrial branches, polypropylene (PP) or expanded polystyrene (EPS) containers are currently used. The former are very durable mechanically, resistant to moisture and grease when the latter allow for production of boxes, inserts or separators for e.g. sensitive electronics. However, the branch is still looking for more and more lighter materials, which will be less expensive and easier in transport, both inside as well as outside of a manufacturing plant.
Reusable packaging in the production cycle – where is it used?
In the logistics the packaging must protect the goods against vibrations, temperature variations and overloading all the time, sometimes during very long travels. Contrary to appearances, delivery to the factory door is not the end of the road. At the production plant it is removed from a pallet , e.g. using a forklift. Especially in the instance of heavy elements the packaging must be very robust to withstand stresses related to unloading in the supply area and then transport and placement in a store. Car manufacturing plants are full of different kinds of pallets, boxes or baskets, therefore each saved storage space is valuable. Thus the containers should enable easy stacking and segregation of stocks per their types, thanks to relevant logistic marking.
Then the packaging is moved from the store to a production line, where it can be transported on a belt conveyor or with a forklift. Its construction and weight must facilitate handling and taking the goods out by an operator or a robot. Due to this fact the packaging is frequently provided with handles and special separators or inserts, which order its contents. Within the logistics chain of packaging, empty containers reach the sender back, whereby the companies must control permanently the inventories of packaging sent to the customers and suppliers, therefore it is worth to provided it with solutions registering its status.
Read more: Which material to choose for automotive returnable packaging?
Effective management of packaging in a closed circuit with Knauf Automotive containers
The innovation, which facilitates the Logistics chain are Komebac® containers made from expanded polypropylene (EPP), which combine light weight and excellent thermal insulation properties that are featured by the EPS Styrofoam with durability of the polypropylene (PP). Packaging produced from the expanded EPP plastic features small weight, since air constitutes 95% of its volume. Moreover, it is very much resistant to deformations, which may occur in the result of loading and unloading, and also suppresses very well impacts or shocks. This combination of the properties provides the advantages at basically each stage of the internal transport logistics, from the stage of packing by transferring up to the production line, where the goods are unpacked. Lighter foam logistic packaging provides larger easiness of handling, transfer by the line operators, store keepers as well as noise reduction during belt conveyor transport.
ADVANTAGES AND PRODUCTION TECHNOLOGY OF KOMEBAC® LOGISTIC PACKAGING
The method of pressure moulding, by which the Komebac® containers are made, enables manufacturing in one process of a product with precisely defined shapes, dimensions and interior organization, therefore they can be adapted in each detail to the characteristics of the particular product. Apart from free application of marking the technology process renders it possible also to install special sensors that send information concerning the cargo in real time. The single material solution is not only very practical but also it eliminates packaging wastes due to the possibility of recycling in 100%. The durability of the Komebac® packaging is estimated even up to 15 years, which corresponds to the life cycle of a car manufactured in the factory.
Contact our experts for more information on the available logistics packaging, i.e. returnable transport packaging.