The automotive industry is one of the most dynamic and innovative sectors of economy, constantly adapting to changing customer needs, expectations and regulations. In 2024, it will face many challenges, both technological and market-related, that will affect its situation and forecasts.
The directions of the automotive industry development in the coming years are clear. Vehicle emissions reductions due to sustainability and ecological requirements, individual customer demands for safety and comfort, and the development of smart technologies are making manufacturing processes increasingly complex. To remain competitive, manufacturers must invest in smart factory and manufacturing solutions. All of this is superimposed on the still felt effects of the global crisis caused by the pandemic and the war in Ukraine. In the light of all these aspects, manufacturers are looking for new technological and material solutions to address limited availability and regularly rising raw material prices. Knauf Industries is a trusted partner for manufacturing companies, Tier-1 suppliers and OEMs to support their goals and strategies by providing innovative solutions in extremely lightweight foamed plastics – expanded polypropylene (EPP) and expanded polystyrene (EPS).
What challenges does the automotive industry face in 2024?
The automotive industry is facing a number of issues that require flexible adaptation to difficult economic and geopolitical conditions, tightening environmental requirements or technological changes related to digitization, among others. One of the most important challenges is decarbonization, i.e. reducing CO2 emissions and switching to alternative fuels such as green electricity or hydrogen. At the end of 2023, assumptions were set for the new, more stringent Euro 7 standard, which is to take into account not only emissions from the exhaust system, but also those generated during braking, and even the durability and battery life of electric and hybrid cars. As a result, manufacturers need to balance the emissions and weight aspects of vehicles more and more sensibly, along with the insulation and comfort aspects of cars. Meanwhile, technological changes and the development of artificial intelligence are causing users to expect individualization of vehicles and greater driving comfort. According to some predictions, it is the experience of using a vehicle that will be a key factor in the purchase decision. Therefore, one of the most important criteria for selecting suppliers in the automotive industry will be high flexibility of the offer.
Trend of decreasing vehicle weight to reduce emissions
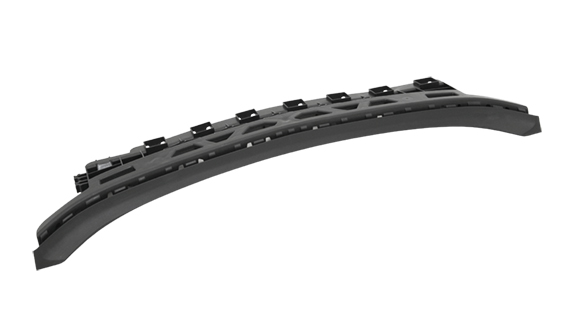
A major trend in vehicle design is the reduction in vehicle weight, enforced by increasingly stringent environmental standards. In the case of internal combustion cars, this reduces exhaust fumes, whereas in electric and hybrid cars it reduces the need for charging while increasing ranges. In addition, the EU's emission requirements are also to take into account particulate pollution from braking. According to a report commissioned by the European Commission, "Non-exhaust traffic related emissions. Brake and tire wear PM," up to 55% of PM 10 emissions from urban traffic are caused by tire and brake pad abrasion. One way to achieve this is precisely by "slimming" vehicles. EPP and EPS are ultralight foam materials that contain 95% and 98% air, respectively. The high quality, strength and rich performance properties of EPP make the material ideal for use in the manufacture of components for car seats, passive safety systems, sun visors, trunk components and even elements of car batteries or hydrogen tanks. EPS fittings, meanwhile, are the optimal material for ultralight front bumper absorbers. By using EPP and EPS, the weight of the vehicle can be reduced by up to 10%, which translates into an 8% reduction in CO2 emissions.
Energy transformation in the automotive industry and Knauf Industries' EPP battery housings
A report from DSR Consulting shows that by 2030 the share of electric vehicles in new car sales in Europe will rise to 40%, and in China to as much as 50%. Meanwhile, the European Union's new standard requires electric and hybrid car manufacturers to have a minimum battery life – 80% up to five years from the start of operation or 100,000 km and 72% after eight years or 160,000 km. Although the battery life of new cars is longer in many cases, it can be expected that the normative restrictions in this regard will gradually increase. This means that auto parts manufacturers will have to adapt their production lines, logistics processes and quality management systems to the new technical and environmental requirements.
Knauf Industries, in line with the ongoing transformation of the automotive industry, offers its customers comprehensive solutions for protecting and insulating the battery in electric and hydrogen cars.

High-quality housings for electric batteries, as well as covers for hydrogen tanks, can be produced from foamed polypropylene. The EPP foam material is not only very lightweight, but also resistant to mechanical damage, chemical damage or electrical breakdown. As an excellent thermal insulator, it protects sensitive components from extreme temperatures and thus prevents failures and extends their life. Our battery kits include housings, module insulators and even fasteners that successfully replace traditional metal mounting components.
Challenges of sound insulation in vehicles
The requirements to reduce the dead weight of vehicles and increase the proportion of recyclable raw materials are causing manufacturers to use far fewer insulating materials. The thick layers of felt, sponges or bituminous materials used a dozen years ago have been replaced by small fragments of carpet or thin felt, which can only be found in sensitive areas. Meanwhile, effective soundproofing of the cabin is important not only in cars with internal combustion engines, but also in electric vehicles. In such vehicles, wheel rolling noises or wind noise are well audible at higher speeds. EPP is an excellent soundproofing material, so it is an ideal alternative to traditional damping solutions. Its foam structure absorbs sound waves and reduces their reflection. The trunk linings, door or floor fillings produced from it cushion all vibrations, ensuring optimal driving comfort. At the same time, the components produced from monomaterial are 100% recyclable, so they fully comply with the requirements of the circular economy.
Automotive market situation and forecasts for the next few years
According to a Deloitte study, the future of the automotive industry by 2035 will be characterized by quite dynamic changes, driven by shifts in customer preferences, climate protection requirements and technological advances. Internal combustion cars will increasingly give way to electric cars, which will gain more intelligent features. Fully autonomous vehicles are unlikely to hit the streets for a long time to come, as too many drivers lack confidence in such solutions. A tangible trend of the future, on the other hand, is zero-emission vehicles built from ultralight parts. Personalization and ease of customized comfort solutions will become one of the key conditions for success in the automotive market. As a leader in the field of innovative plastics processing, we offer our partners a wide range of production capabilities and individual design support using the latest technologies. It is worth entrusting us with the outsourcing of the production of innovative foam components that can be easily tailored to meet requirements in every respect.
Knauf Industries as a trusted partner for manufacturing companies, Tier-1 suppliers and OEMs
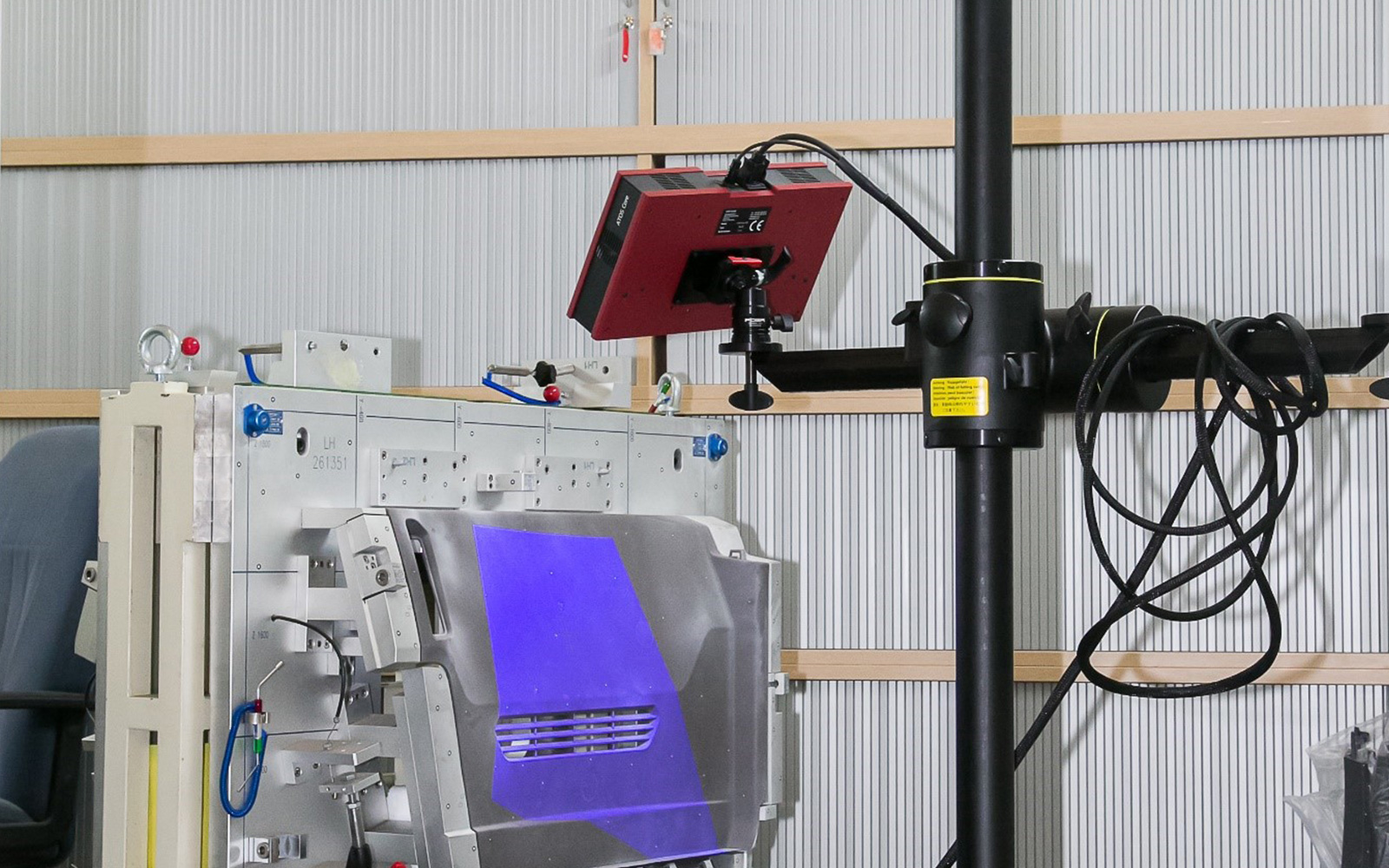
At Knauf Industries we offer to our customers comprehensive solutions, from design, preparation for production to professional processing of EPP foam components by plastic molding. Our products meet the highest standards of quality, safety and ecology, and our services are flexible and tailored to individual customer needs. Manufacturing cooperation with Knauf Industries is an opportunity to benefit from the experience and knowledge of a company that has been active in the automotive market for more than 40 years and continuously invests in technological development and innovation. A state-of-the-art measurement laboratory, 3D scanner, simulations performed and digital design services are a guarantee of precision, speed and reliability of processes. Our factories are located in strategic locations around the world, ensuring fast and efficient delivery of orders. We are ready to meet the challenges facing the automotive industry in the coming years, such as the development of electromobility, digital transformation and environmental regulatory changes.
We invite you to cooperate and contact us!