The challenges of smart manufacturing affect all automotive leaders who want to continue to set new trends, reach a wider audience and implement solutions that improve efficiency while reducing costs. Without Industry 4.0 solutions in the supply chain, you can forget about achieving these goals. That is why it makes sense to choose reliable partners with well-developed production lines and Smart Factories.
Effectiveness, efficiency, innovation – a new definition of factory system
Smart Factory in 2024 no longer surprises anyone, and Industry 4.0 is a reality for many manufacturing companies. Solutions such as the Internet of Things, the robotization of production or harnessing the potential of 5G communications are just some of the issues that modern companies face on a daily basis. These are not exotic, imaginary problems of the extremely progressive economies of the Far East or one of the myths that shape markets in the US. The Fourth Industrial Revolution is happening right here in Europe. There are already many examples of smart manufacturing in the automotive industry. The key issue for 21st century companies is to meet environmental standards, and a modern manufacturing system makes this task much easier. Industry 4.0 allows us to design solutions that work perfectly with our products, reduce "time to market" and take a much better, more meticulous approach to the modern consumer.
See also: Logistics in the automotive industry – effective solutions and innovations
What is a Smart Factory?
Smart Factory is a central concept of Industry 4.0. It is a production environment where machines and even entire production plants and logistics systems communicate with each other and organize the production process largely autonomously, without human intervention. The role of employees is limited to monitoring processes and intervening only when needed. The basis of the Smart Factory are "smart products," i.e. products to which, for example, RFID chips or tags are attached. Through wireless communication via 5G or Bluetooth, machines can read RFID tags, locate individual components and operate the entire production process. The smart factory is based on cyber-physical systems, that is, the integration of the digital world with the physical world through the Industrial Internet of Things (IIoT). Such state-of-the-art factories use completely new methods of organizing production, which enable, among other things, a high level of product personalization and a low level of employee involvement in the entire manufacturing process.
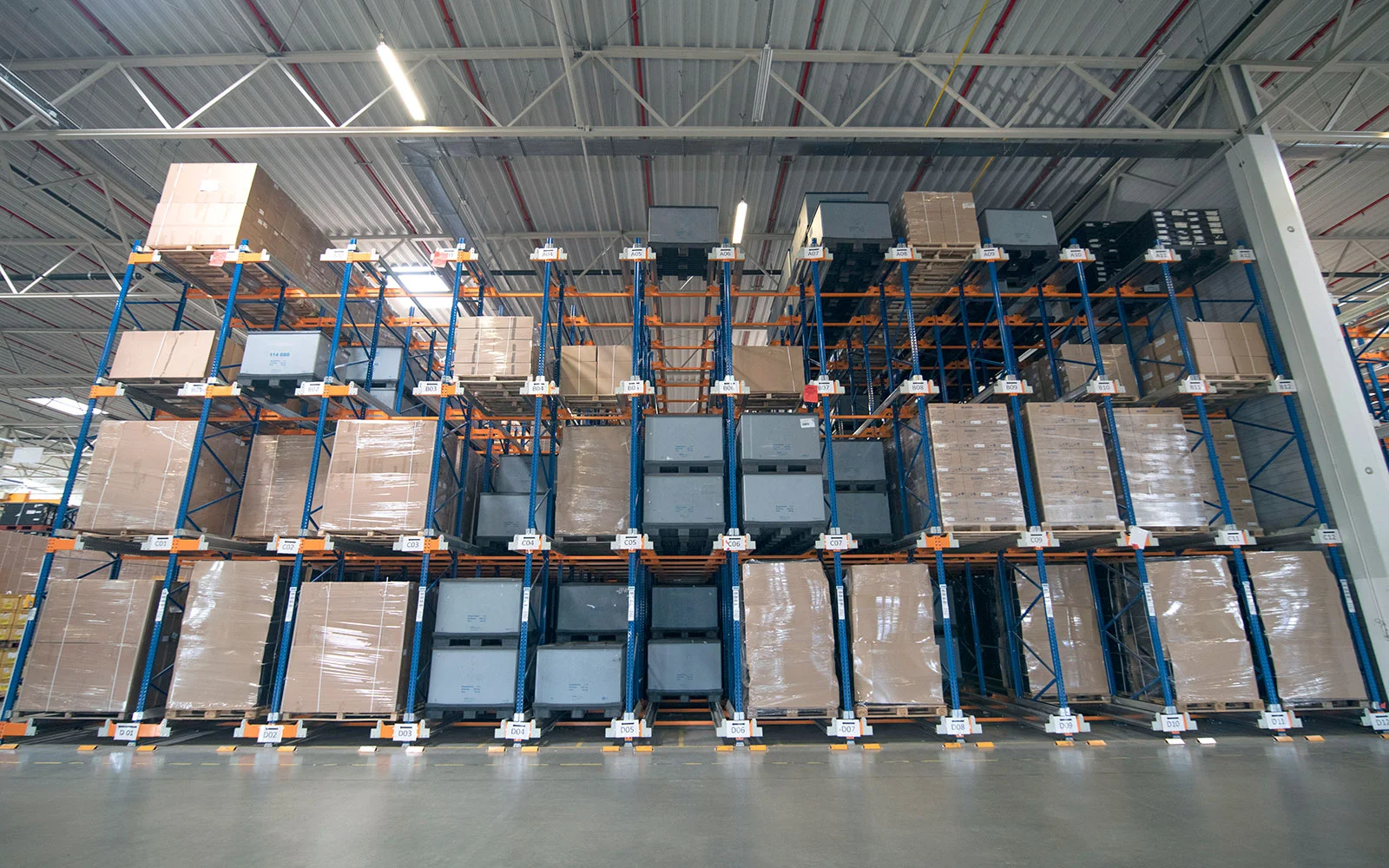
Challenges and unique solutions in the implementation of a Smart Factory
There are many issues to be addressed in order to integrate intelligent production of automotive components. It does not merely come down to the right machine equipment. In the previous era – the industry of The Third Revolution – the right infrastructure was key. Nowadays, automated technology, personnel and innovation are required. New solutions are also becoming increasingly important. Many people already wonder what effect 5G technology will have on manufacturing. It is certain to redefine Internet of Things (IoT) solutions and greatly expand design and communication capabilities. Some companies are already using the technology extensively in the areas of automation, artificial intelligence (AI), machine learning (ML), augmented and virtual reality AR/VR or robotics, improving and transforming their processes and services. Nowadays, every car factory needs innovation. Implementing Industry 4.0 solutions in the supply chain is a prerequisite for remaining competitive and eliminating problems caused by logistics costs. On the other hand, it is not always clear in which direction to go and which solutions to choose. Perhaps in such a situation, it is worth considering choosing the right manufacturing partner who knows these issues and has the courage to implement Smart Factory solutions.
See also: Supply chain cost optimization – how to reduce supply chain costs?
How is the concept of Smart Factory and Industry 4.0 developing?
In the coming years, the prevalence of Smart Factories in the automotive industry is bound to grow, and more interesting technologies will be implemented over time. In fact, the 5G revolution has already begun. According to consulting firm STL Partners, the financial benefits of implementing this technology for the global manufacturing industry could reach $740 billion by 2030. However, it is important to remember that many production lines are still based on old standards and do not resemble the car factories of the future. So it is worth preparing for the coming changes in the industry and implementing innovative solutions as soon as possible.
Technologies used in a Smart Factory
A Smart Factory integrates advanced technologies such as artificial intelligence (AI), the Internet of Things (IoT), digital twins, robotics and Big Data. The goal of all processes is to create a manufacturing environment that not only increases efficiency, but also demonstrates flexibility and adaptability to changing conditions. All components of this environment work together to create an integrated system that enables efficient and flexible production management. Learn about the elements of the Smart Factory concept – their application and future prospects.
Digital twins and the Smart Factory concept
Digital twins, i.e. virtual replicas of physical objects or systems, can be used to create accurate, dynamic models of machines, process lines, production processes or even entire factories. This makes it possible to anticipate problems, optimize processes and make informed decisions about production management. Digital twins, combined with other technologies such as the Internet of Things (IoT), artificial intelligence (AI), and cyber-physical systems (CPS), form the basis for the future of Industry 4.0.
Industrial Internet of Things in Smart Factories
The Industrial Internet of Things (IIoT) plays a key role in the concept of Smart Factories and Industry 4.0. The solution uses smart technologies to streamline manufacturing and industrial processes. First and foremost, it enables almost any device to be connected to the Internet so that it can be remotely accessed and managed from anywhere. IIoT takes data collected in the cloud by machines operating in an industrial environment and uses it for real-time analysis. This way, problems and areas for improvement can be identified faster, saving time and money. The Industrial Internet of Things helps build models of digital twins of factories, production lines or products. They allow the company to create predictive models and simulations that would be difficult to run in real-world conditions. IIoT is a key element in the automation and robotization of manufacturing processes.
Machine learning and Artificial Intelligence in a Smart Factory
Artificial Intelligence (AI) is a scientific field that deals with the creation and design of machines that can mimic human behavior and thought processes. It covers a wide range of technologies and topics, such as natural language processing (NLP), autonomous vehicles, robotics and machine learning (ML), among others. ML algorithms can collect more and more data over time, increasing the adaptability of machines. Robots are already widely used in car manufacturing, performing tasks such as welding, assembly and painting. In the future, they should become increasingly flexible and autonomous, allowing them to adapt to changing conditions. In this context, AI and ML can help optimize production processes, improve product quality, increase energy efficiency and reduce costs.
Developing plastics application and processing innovations with Smart Factory solutions
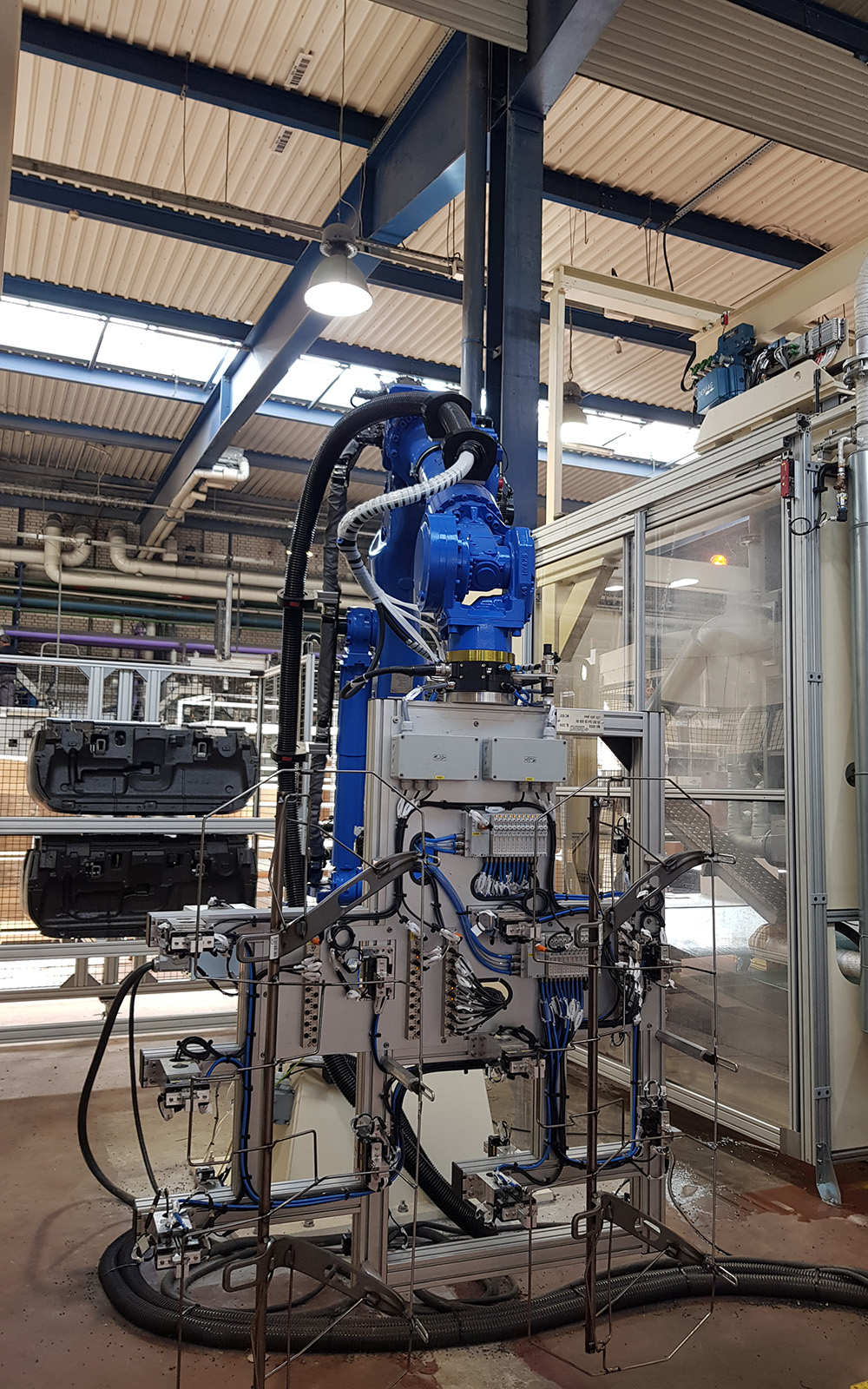
Driven by the solutions of Industry 4.0, the rapid development of sustainable plastics processing technologies allows for continuous improvements in the mechanical and strength properties of the components produced using these materials. Thanks to plastic injection molding and foamed plastic injection molding technologies, for example, automotive parts can be easily designed and manufactured from recycled raw materials, which are increasingly replacing high carbon footprint materials or innovative multi-material components. Smart Factory solutions, such as advanced AI and ML algorithms, can contribute to the development of completely new, creative product solutions, optimize production processes, and at the same time improve their quality while reducing costs and increasing the energy efficiency of the entire process.
Knauf industries – a trusted partner in smart manufacturing
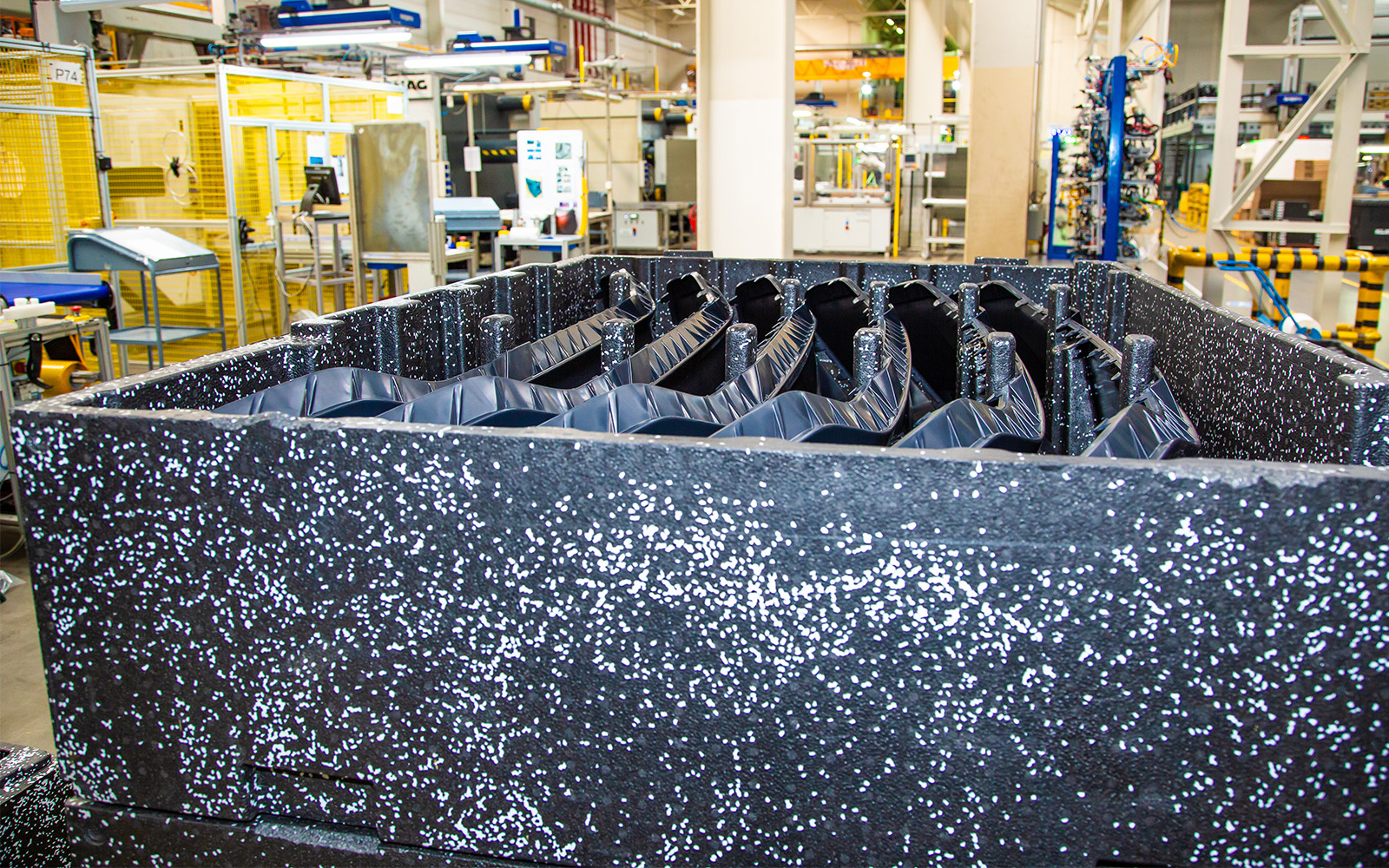
When it comes to Smart Manufacturing, Knauf Industries Automotive is ready. We try to implement successful solutions as soon as possible, especially if they improve the competitiveness of our partners in the market. We focus on adapting to the needs of our customers and supporting them in manufacturing automotive plastic injection molding parts and implementing their project objectives. In Smart Factories, the humans work in the communication and expertise sector. We know that by combining the capabilities of modern robots, 3D technology (eg. 3D printers and scanners) and new communication channels, we will provide the best possible solutions. Therefore, we focus on comprehensive cooperation, which applies to each stage of a given project. We are truly committed to transforming the complex processes of today's Smart Manufacturing into a simple, customer-friendly procedure. Our solutions ensure that any negative impact of complicated technical issues is minimized – we offer:
- modern production lines,
- the flexibility to adapt to new standards,
- the digitalization of logistics processes,
- human resources management through RFID,
- the readiness to meet the challenges of Industry 4.0.
We are constantly drawing on the expertise of our research & development center – IDLab® and local R&D teams monitoring the latest trends and solutions.