Ford caught the attention of the international press and automotive industry when, in June 2018, it announced that each of its vehicles contains 250 bottles of recycled plastic, which represents the reuse of 1.2 billion bottles per year. Now in 2023, it declares that more than 85% of vehicle parts and materials are recycled, and its strategy focuses on including environmentally friendly and recycled plastics and renewable materials.
VOLVO, RENAULT, OPEL, FORD AND SKODA INCREASE USE OF HIGH-QUALITY RECYCLED MATERIALS
Volvo had ensured that at least 25% of the plastics used in the manufacture of cars would be recycled in 2025 under the UN-backed environmental plan. The Swedish company has called on automotive suppliers to cooperate more closely with manufacturers to develop the next generation of components as sustainable as possible, with a particular focus on the use of recycled plastics.
One of the main priorities of Knauf Industries Automotive today is to develop sustainable industrial processes that result in increasingly environmentally friendly materials. That's why we created IDLab, which enables us to supply expanded polystyrene (EPS) or recycled Airpop parts to automotive customers.
Ford recycled plastic components are used to protect the car chassis and to cover the front and back wheel arches. They improve aerodynamics and can assist in better sound insulation.
The use of recycled plastic in cars is nothing new. Opel has been doing this since 1990. Already the Calibra model contained four types of recycled materials that were incorporated into the headlight frames and water deflector, bumper attachments and even an inlet manifold.
Skoda also uses recycled plastic components using, among other things, injection molding technology. According to a comment by Lukáš Zuzánek, Skoda's 2020 Technical Development Officer, "due to its properties, plastic is by far the best performing material used in the automotive industry. It replaces metal, contributing to lower car weight, lower CO2 emissions and lower fuel consumption."
See also: Automotive’s engagement in the fight against climate change
WHICH PLASTICS ARE RECYCLED? Huge potential of polypropylene
Renault Group is also engaged in the use of recycled materials. Since the launch of the Megane II model at the end of 2014, it has 30% of components made from recycled materials. Meanwhile, the Renault Scenic Etech model, which is 90% recyclable and uses plastic instead of leather for the seat upholstery, has been announced for 2024.
In March 2019 the French automobile giant published a study “Closed-loop polypropylene, an opportunity for the automotive sector" that highlights the huge potential of this polymer as a source of supply for the automobile industry, also taking into account the guarantee of meeting the requirements of the European regulation on the recovery of materials from vehicles that have reached the end of their useful life.
Recycling regulations in the automotive industry
The research, published by Field Action Science Reports, shows that in 2015 plastic derivatives represented 17% of the weight of cars (12% for polymers and 5% for elastomers) and that the forecast for 2030 indicates that this proportion will increase to almost 20% (15.6%, polymers). The average weight of cars will be reduced from 1250 to 1123 kg and they will contain an additional 25 kg of plastic. The challenge is to significantly increase the amount of recycled materials.
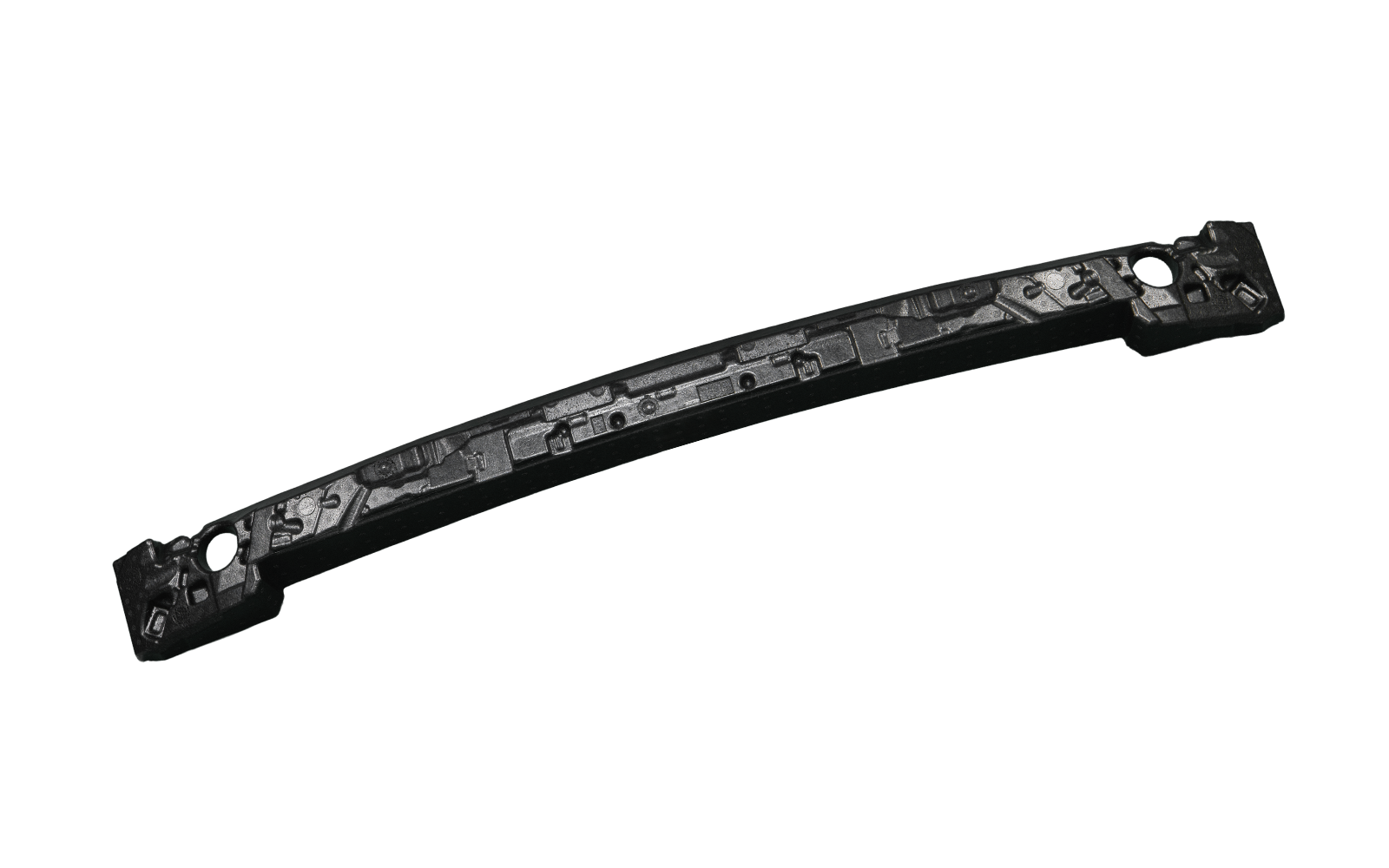
The research describes in detail the Renault project, which aims to develop a closed-loop economy by recovering polypropylene from the bumpers and wheel arch coverings so that it can be used to produce new plastic car parts.
Increased use of environmentally friendly EPP
The presence of expanded polypropylene (EPP) in automotive components, of which Knauf Industries Automotive is one of the main suppliers, is constantly increasing due to numerous advantages in terms of lightness and increased safety. European producers consume more than one million tonnes of polypropylene per year.
The amount recovered for reuse increases every year. As an example, 680 tonnes of polypropylene were recycled by French ELV processing centres in 2015, corresponding to the bumpers and wheel arches of 42,000 vehicles.
RECYCLING PROCESS – ONGOING INVESTMENT in energy efficiency and sustainable development
The Spanish car parts industry, one of the most powerful in the world, is committed to the European objectives of the decarbonisation of the economy and transport. According to the Spanish Association of Automotive Suppliers (SERNAUTO), of which Knauf Industries Automotive is a member, this sector invested in 2018 1,545 million EUR (4.2% of its turnover) in research and development of technological solutions that enable the design of increasingly efficient and sustainable vehicles.
One solution is to gradually increase utilisation of recycled plastics, although a study developed by Renault shows that recovery processes need to be improved in order to be more efficient and obtain high-quality end products at a cost that can compete with primary raw material prices.
The main difficulties concern the separation of different components of which they are composed and the elimination of odours and impurities in order to produce high quality reusable granules.
In 2019, the Plastics Industry Association developed a project to demonstrate the recycling capacity of thermoplastic bumpers. The results are very promising for new recycled components. The American organisation confirms that there is a technology and market for recycling plastics, such as EPP used in the manufacture of automotive components, and points out the interest of brands in incorporating them into design and production processes.
See also: Components from sustainable materials from Knauf Automotive
RECYCLING REGULATIONS FOR THE AUTOMOTIVE INDUSTRY IN EUROPE
To remind, according to Directive 2000/53/EC, from 1 January 2015 car manufacturers are obliged to reuse 95% of end-of-life vehicles: 85% from their materials and the remaining 10% for energy generation.
THE RECYCLING POTENTIAL OF PLASTICS IN THE AUTOMOTIVE INDUSTRY
Although the potential of recycling of plastics in the automotive sector has been demonstrated by numerous research studies and their application in industrial processes, it still has to overcome the reluctance, also among manufacturers. For example, at the Convention of the American Institute of Scrap Recycling Industries (ISRI) in 2017, Toyota pointed out as one of the problems to be overcome that recycled material is of lower quality. Therefore, in order to be able to offer such solutions, companies must meet technical specifications and quality requirements and offer constant delivery performance.
Awareness of the sector and commitment to technological innovation are the basis for building a further sustainable automotive industry.