The share of plastics in car construction is constantly increasing. Maximum simplification and slimming down the structure to maximize convenience, reduce costs and minimize the environmental footprint. For this purpose, it was necessary to eliminate all materials traditionally used in the carmaking sector and replace them with lighter and more environment-friendly materials.
Expanded polypropylene (EPP) was one of the new materials selected. The revolutionary car model was equipped with replaceable panels (doors, hood, mudguards, bumpers), mounted on a tubular, aluminum structure. Thanks to 100% recoverable parts, Toyota reduced the vehicle's weight by 20%, down to the value of 750 kg.
CAR WEIGHT aND USED MATERIALS
Back when in 2013 Toyota unveiled the ME.WE concept car model, which was designed around the philosophy of 'remove everything unnecessary'. Despite the fact that the ME.WE is still just a prototype that has not yet been implemented into serial production, many of the plastic parts made from EPP it features have become indispensable to the automotive industry. The growing need to reduce vehicle weight in order to improve energy efficiency, and in the case of electric vehicles, to improve their range, forced the R&D departments of individual car brands to intensify efforts in the area of tapping the enormous potential offered by polymers.

Here are several examples:
- production methods through molding and injection of plastics, ideal for processing polypropylene, enable standard automotive components production and maximum return on investment;
- plastic bumpers combined with glass fibers are twice as light and absorb up to five times more impact energy.
The light weight of car parts AND NEW TECHNOLOGIES reduce fuel consumption
According to the latest 2023 EPA Automotive Trends Report, over the past five years, 8 of the 14 largest manufacturers selling vehicles in the US have lowered their estimated actual CO2 emissions for new vehicles.
Tesla consistently ranks highest with its zero-emission electric vehicle fleet. The biggest reduction in CO2 emissions was recorded by Toyota (differences measured between the 2017 and 2022 model years) at 32 g/ml. Toyota reduced greenhouse gas emissions across all vehicle types and overall emissions decreased, although the share of so-called Truck SUVs (as defined in the source report: 4-wheel drive SUVs with a gross vehicle weight of min. 6000 lbs) increased from 27% to 38%. Kia achieved the second highest reduction in total tailpipe CO2 emissions at 21 g/mi, while Mercedes recorded the third highest reduction in total CO2 emissions at 14 g/mi. Emission reductions were also achieved by Hyundai, Ford, Nissan, Stellantis and VW.
What materials are used in car manufacturing? Effects on the combustion and weight of cars
Reducing the weight of components is very important. According to the Automotive Trends Report (2018) by the US Environmental Protection Agency (EPA), the energy efficiency of a car grows by 2% for every 45 kg replaced by plastic. Considering the fact that 100 kg of plastic parts can replaced even 300 kg of steel (the main raw material used in car production), this means 750 liters of fuel saved per every 150,000 km and 30 tons less CO2 emissions annually in Europe alone.
Polymers are currently the second most commonly used raw material in vehicle production and make up 20% of overall vehicle weight, i.e. about 300 kg in a car weighing 1,500 kg, in approx. 2000 parts of different types and sizes. According to Plastics in Motion with Today’s Trends in Transportation prepared by the Plastics Industry Association in Washington D.C., plastic parts make up 50% of vehicles’ volume and are on an increasing trend.
See also: Achievements in the use of thermoplastic components in the automotive industry in 2019
CAR WEIGHT AND DEVELOPMENT OF MATERIALS USED IN CAR PRODUCTION
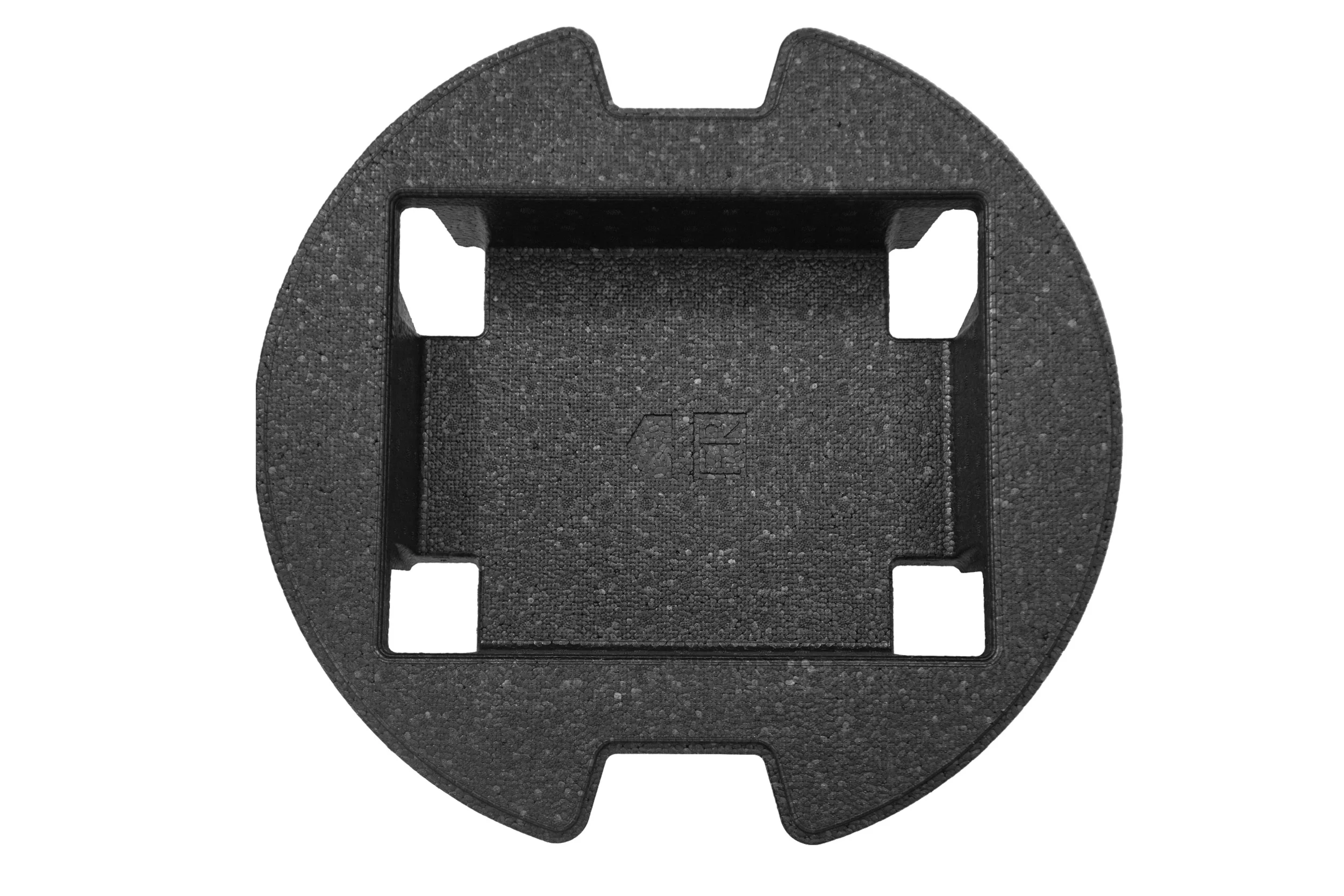
The application of polymers in the automotive industry is nothing new, but it was done on a substantially smaller scale than now. In the 1950's, cars contained negligible amounts of plastic, and up to the 70’s, the share of plastic in vehicles did not exceed 3%. In 2004, the Transportation Energy Data Book indicated that a medium-sized car contained approx. 120 kg of plastic, and one kilogram of plastic could replace even 1,5 kg of traditional materials. Since that time, technological progress has made it possible to improve this ratio. By making the EPP elements more attractive, the weight of the car is reducing.
The same study analyzed the evolution of the utilization of individual materials in car production from 1977 to 2004. It was determined that the share of steel shrank from 75% to 53%, the share of aluminum grew from 2,6% to 8,6%, and of plastic from 4,6% to 7,6% (in Europe: it reached the level of 11% globally).
AVERAGE WEIGHT OF CARS AND CO₂ EMISSIONS REPORTS
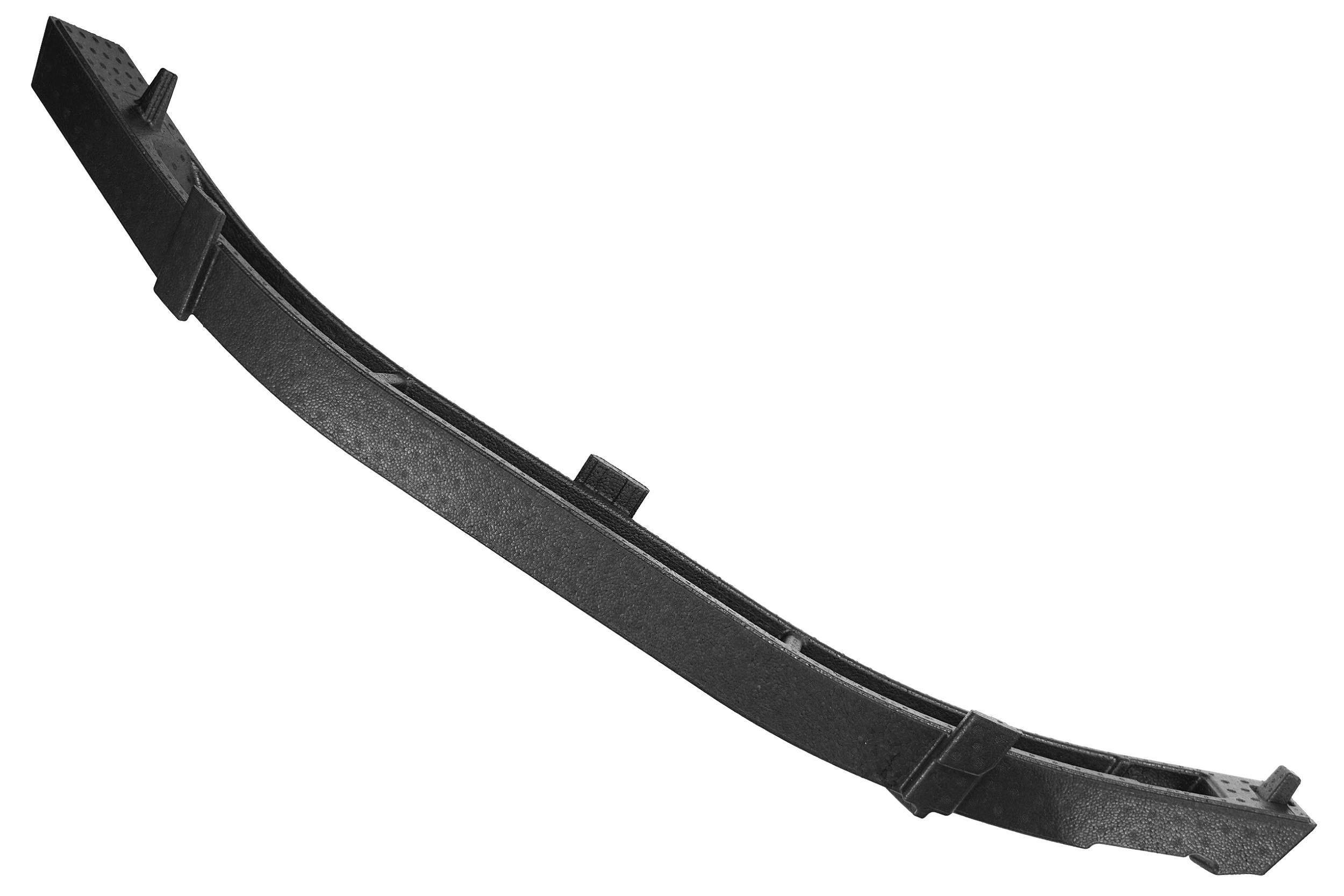
Despite the fact that the application of lightweight materials has become more widespread over the past decade, and reducing vehicle weight posed a challenge for the automotive sector, average vehicle weight has remained at a constant from 2004 until 2018 and has increased in recent years. This data is given by the previously mentioned Automotive Trends Report from 2018 and 2023. The reason for this state of affairs is easy to explain: despite the application of lighter parts like aluminum and foams such as EPP, consumers are choosing large cars with comprehensive equipment more and more frequently. The following data illustrates this: since 1975, in the USA, sales of sedan and station wagon vehicles decreased by 13%, while pick-up model sales increased by 29%.
As a consequence, the challenge that is being addressed is the future technological development required for farther-reaching substitution of traditional materials with parts improving vehicles’ energy efficiency and safety. This is the goal that the efforts of our company – Knauf Industries Automotive – are focused on.
Sources:
https://www.epa.gov/system/files/documents/2023-12/420s23002.pdf
https://www.sciencedirect.com/science/article/abs/pii/S2214785317304881