Since 1839, when Charles Goodyear patented vulcanized rubber, obtained by modifying the mechanical properties of natural rubber taken from the Pará rubber tree, the plastics and automotive industry began sharing a common history. This rubber was the first polymer and soon found an application in tires for vehicles.
Until the middle of the 20th century, research and experiments involving plastics led to the creation of new materials, which gradually turned out to be useful in the automotive industry. For example, the excellent insulating properties of bakelite, obtained by Leo H. Backeland in 1907, made it a perfect material for manufacturing plugs, handles and switches.
In 1913, Henry Ford’s assembly line revolutionized the automotive industry. Serial production reduced costs and made the car a mass-produced consumer product. Concurrent advances in scientific research enabled the development of macromolecular chemistry, which was of decisive significance to the discovery of new polymers like polyurethanes, ethylene, epoxide resins, ABS, polyesters and polystyrene.
The first significant change in the widespread application of plastics in the automotive sector occurred after World War II. As James Maxwell reminisces in his book (Woodhead Publishing Limited, 1994) Plastics in the automotive industry, the opportunity of developing a cheap, petroleum-derived fuel afforded a coherent and reliable raw material for production of cheap plastics. This opened up a broad range of possibilities for the automotive industry.
The discovery of polypropylene
In the 1960's, new discoveries in the field of polymers made it possible to develop thermosetting polymers such as polypropylene, a type of plastic commonly applied in modern vehicles. Its numerous mechanical properties, light weight, and the fact that it is 100% recyclable mean that polypropylene now makes up 40% of all plastics used in the automotive sector.
Knauf Industries Automotive is working intensively on developing new applications for thermoplastics such as expanded polypropylene (EPP) and expanded polystyrene (EPS), whose presence in vehicles will continue to grow over the next several years, replacing other materials traditionally applied in the industry.
In the second half of the 1950’s, plastic was applied for manufacturing of a roof (Citröen DS), truck cabins, elbow rests, and empty interior panels. In the 1960's, polypropylene pedals were already being manufactured, and cooling fan and radiator housing components, the cooling system’s equalizing tank, hydraulic fluid tanks, and rigid dashboard guards were injection-molded. Such parts as the splitter cover, door and window components, seat foam and the front grille began to be manufactured from plastic.
The development of the plastic bumper
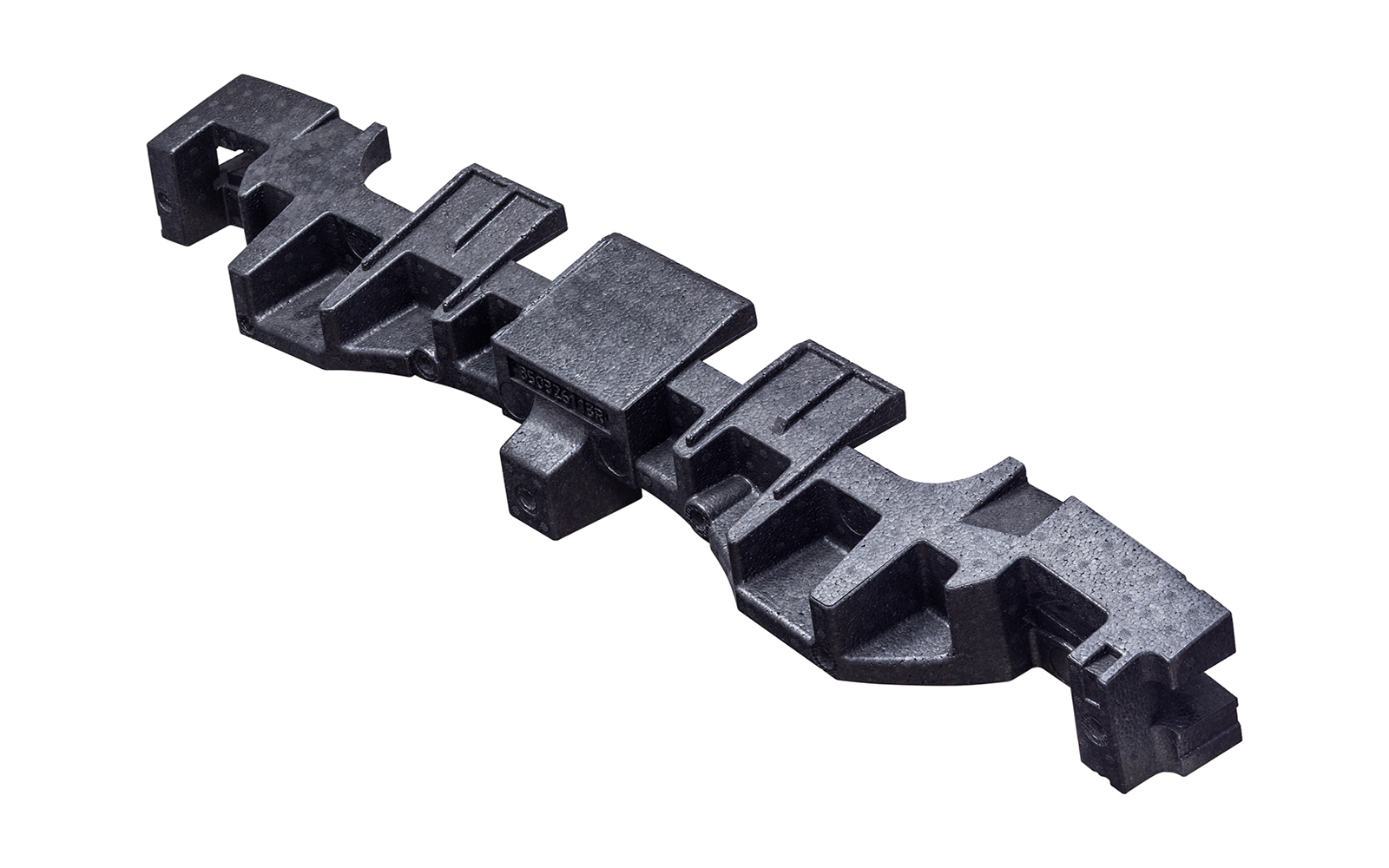
In the 1960's, technological progress made it possible to apply polymers in manufacturing of the most important car parts. The Renault 5 model from 1972 was the first mass-produced car with a plastic bumper, which became widespread in the decade that followed. This was a watershed moment in the history of the automotive industry, because, besides their decisive influence on vehicles’ appearance, plastic bumpers contributed to substantial reduction of vehicle weight and became a fundamental part of improved safety.
Volkswagen was the first brand to introduce “seamless” plastic radiator and fuel tanks; BMW – the front and rear spoiler; Renault – protective side panels; and General Motors – oil collector.
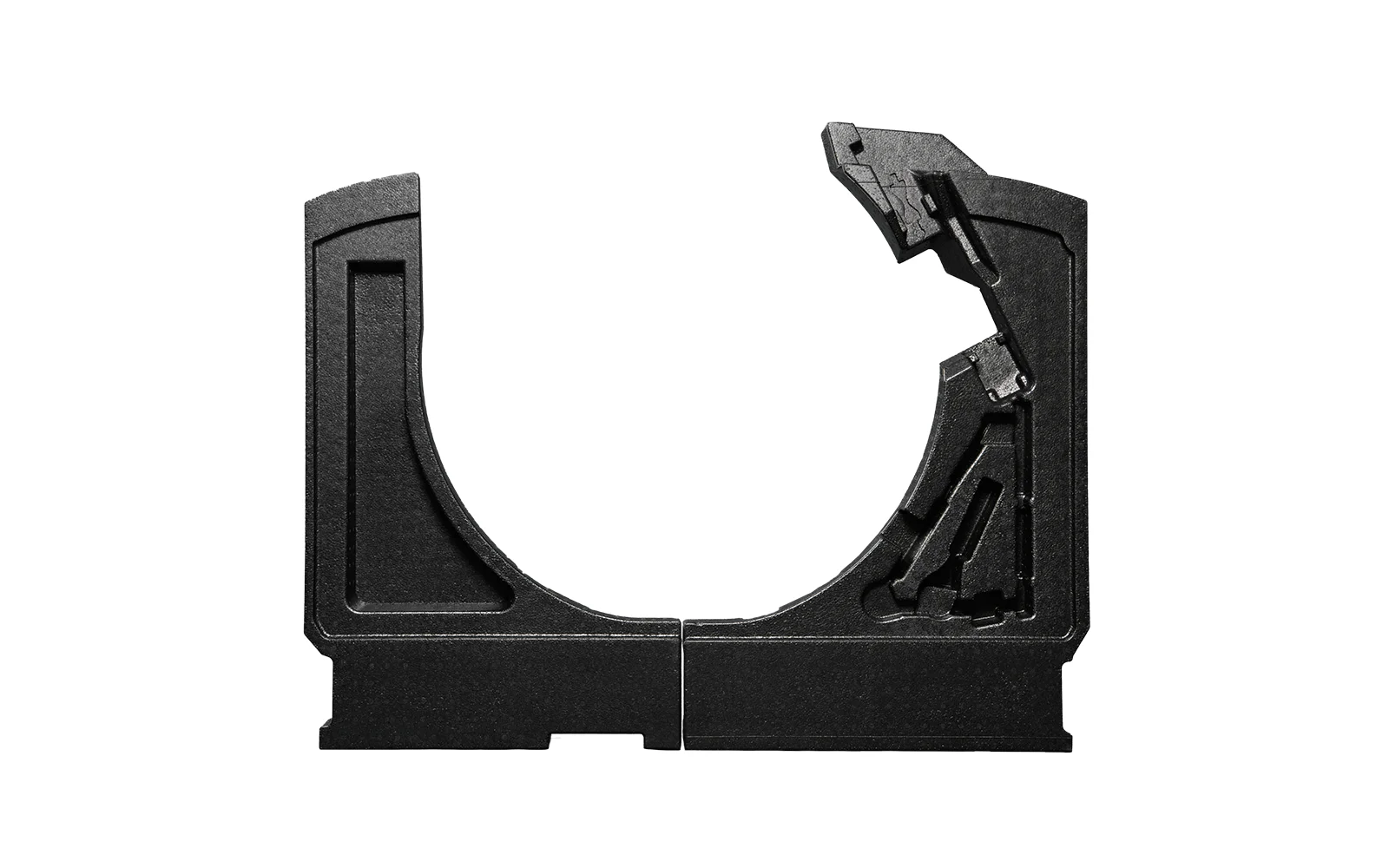
As R&D departments improved thermoplastic properties, impact absorption capacities and anti-corrosion qualities, design possibilities were also expanded, and individual brands expanded the application of new materials in the automotive industry to include such components as: mudguards, reflectors, housings, hood and tailgates.
When the turn of the century came, car accessories and performance were enhanced, and environmental protection regulations started to require lower emissions and greater engagement in recycling and reuse of components. Thus, the challenge is to both reduce the weight of vehicles and search for 100% recyclable materials that can replace materials used until now, also in the case of car body parts.
Plastic engines? The report “Plastics at the heart of the cars of today and the revolutions of tomorrow”, published in PlasticsleMag, Innovation and Plastics Magazine in March 2018, predicts that plastic engines will be created in the near future. Furthermore, it points to a revolution in mobility, associated, above all, with the emergence of car sharing on a per-minute basis, and resulting from the development of the electric, networked car. Such solutions will create new possibilities of applying plastics in the automotive industry.