Innovation and sustainable development are megatrends that have been observed in recent years and the primary objectives of the automotive industry for 2020. As the industry goes in this direction, the amount of plastics in cars will continue to grow.
Production of sustainable vehicles with lower fuel consumption, and emitting less pollution, necessitates reduction of their weight. This goal can be achieved by gradually increasing the presence of lightweight materials like thermoplastics and carbon fiber, which are replacing metal components. On the other hand, automotive is intensifying work on electric and hybrid vehicles. In this regard, plastics open up new horizons.
These are indispensable changes that contribute to environmental protection and enable adaptation to the most restrictive government regulations. For example, the new European regulation on CO2 emissions concerning passenger cars and delivery vans foresees a 20% reduction in 2025 compared to 2021. This reduction will reach up to 37,5% in 2030 for passenger cars and up to 31% for delivery vehicles. The article New EU emission standards start, published on just-auto.com, contains a declaration of the European Union, in which we read that “The new Regulation will reduce fuel consumption costs for consumers and strengthen the competitiveness of the EU automotive industry, while stimulating employment and contributing to the achievement of the EU's commitments under the Paris Agreement”.
EPP and EPS plastics at the IDLab of Knauf Industries Automotive
To meet these new requirements, automotive manufacturers must gradually adapt their production processes. As a consequence, innovation has become a priority today. The IDLab of Knauf Industries Automotive conducts research on solutions and technologies that open up new horizons for the application of plastics like expanded polypropylene (EPP) and expanded polystyrene (EPS) in cars, and it also develops and tests new products containing new expanded plastics. We are aware of the deep transformations occurring in the automotive industry and the leading role of suppliers in them. In 2020, Knauf will continue to develop digital technology.
The article Five 2020 Trends for the Automotive Industry, published in Autonomous Vehicle Technology, presents the prospects for development of the electric car market and turns attention to growing awareness of the issue of a sustainable model of mobility and improvement of car performance (reduction of battery production and operating costs, while simultaneously increasing battery capacity). It is predicted that, in 2030, 55% of the automotive industry’s sales will be fully electric vehicles.
Of course, to reach such a number, engagement in innovative technologies is decidedly required. Automation of assembly and 3D printing, which is closely related to the former, provide a path to development of new solutions, reduction of raw materials consumption and improvement of the sector’s efficiency in the long term. In this scope, Knauf Industries Automotive is conducting intensive research and development work in the conviction that the immediate future of industrial processes is grounded in a circular economy.
Plastic the main character among innovative technologies
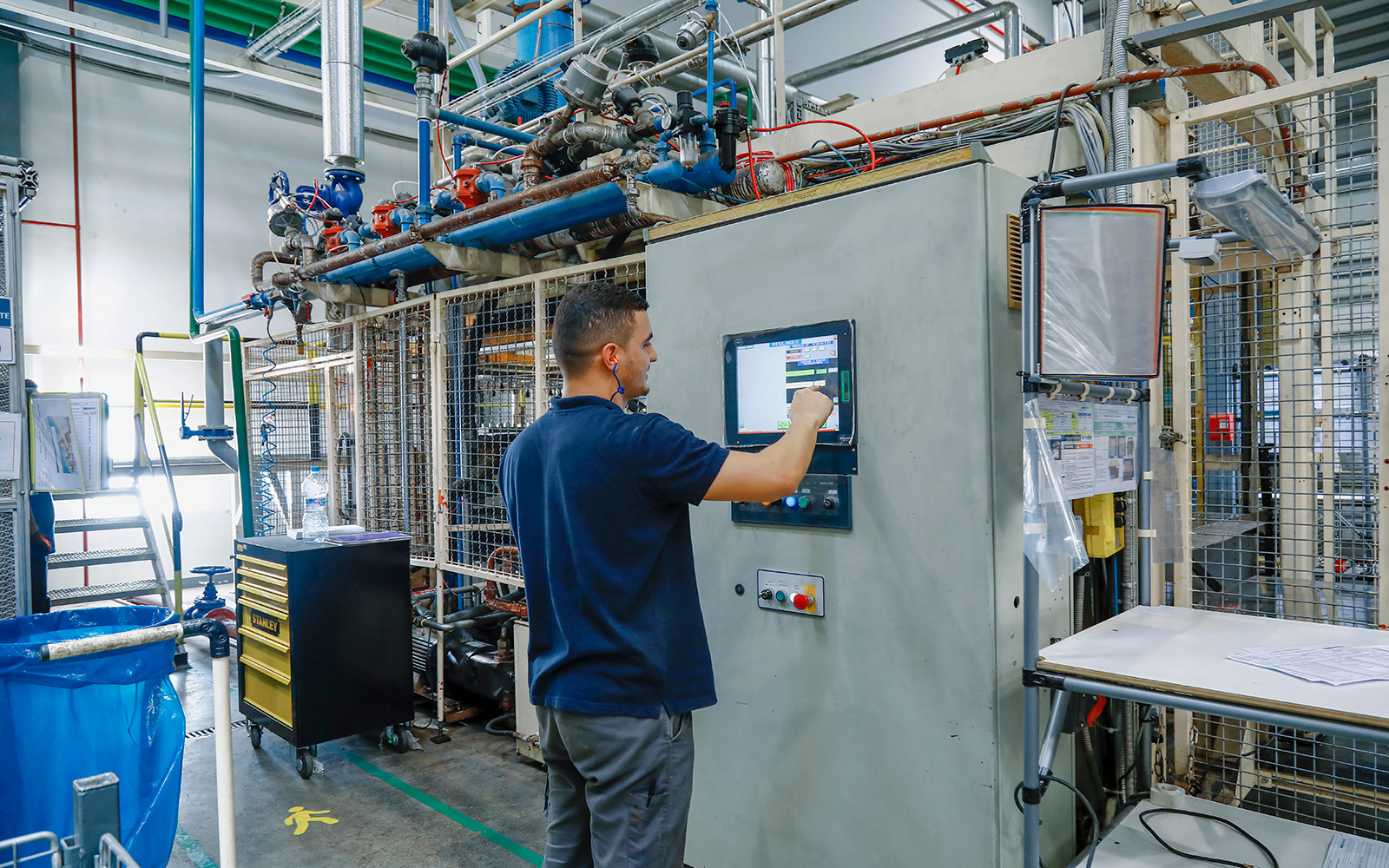
Composites World, in its report The markets: Automotive (2020), stresses that autonomous driving and electric mobility are the two main trends that will require innovative plastic products and processing technologies in order to obtain products of even better quality that will be able to combine an increasing number of functions and new, high-performance composite technologies. The market will be characterized by increased demand for electronic components such as plugs and connectors. The text also indicates that solutions associated with injection molding of plastics will be the response to the development of the electric vehicles market.
This relates to, among others, technologies like overmolding, in which impressions made from woven or unidirectional fibers in a thermoplastic die are press-formed into a 3D shape, while reinforced plastic is injection-molded in the top part and around the die, forming ribs, protrusions, inserts and fastening points of complex geometry. In this way, components such as backrests, airbag housings, door crossbars, bumper bars and floor components can be manufactured.
The article These are the 8 key 3D printing trends for 2020 according to HP, published in the 3D Printing Media Network, presents advances in process automation enabling perfect integration of 3D-printed metal and plastic elements. 3D printing will shortly offer immediate solutions making it possible to create wear-resistant parts, add surface treatment, and even to manufacture engines with plastic components.
The development of this technology will allow manufacturers to generate less waste and emit less CO2. The work of engineers and designers is of critical importance to optimization of materials consumption, even in the designing of components with complicated geometry, so that vehicles’ weight can be reduced and their energy efficiency improved.