The increasing use of plastics in the automotive industry is a response to the need of reducing the weight of vehicles and improving fuel efficiency, complying with the strictest regulations on greenhouse gas emissions and the demand for environmentally friendly products. However, plastics also ensure improvements in car design, both in terms of internal and external components.
Today, automotive designers are looking for a lightweight material that will improve the designing, manufacturing and efficiency of moulded parts. For decades, they replaced heavy metal components with plastics such as polypropylene (thermoplastic) and fiber-filled composites. This practice is expanding since manufacturers are trying to increase the use of polymers for vehicle exterior parts and interior accessories.
Thanks to technological progress, engineers have a wider range of new and lighter options, offering greater freedom of design, including in mechanical parts that are consistent with the weight reduction strategy. An analysis of the latest developments in car weight reduction is presented in the article Advanced Polymers Drive Automotive Lightweighting.
New applications of plastics
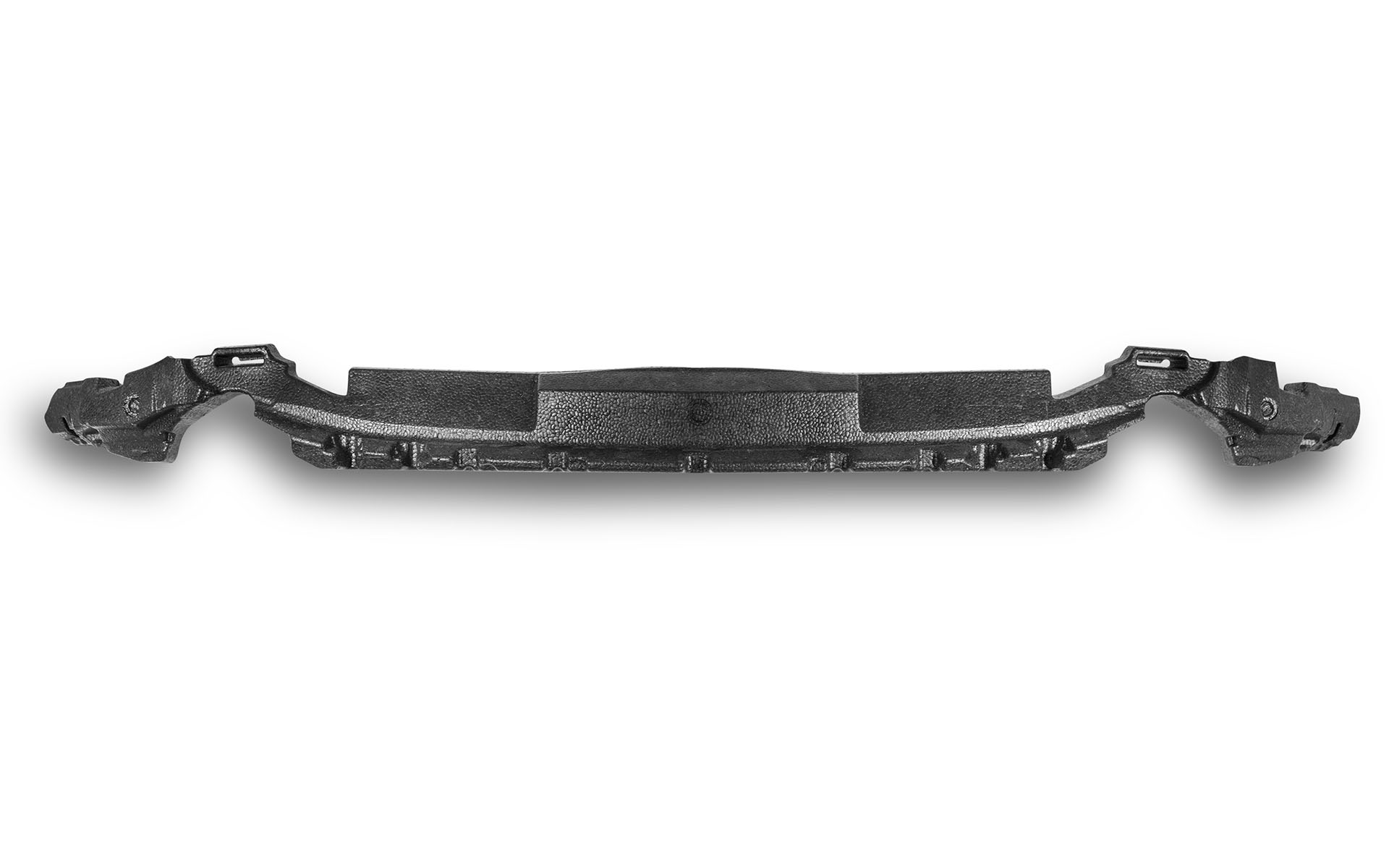
At Knauf Industries Automotive we are gathering experience in the design and manufacture of automotive plastic components, expanding the use of moulded plastics such as expanded polypropylene (EPP) and expanded polystyrene (EPS). We invest in innovation through the activities of IDLab, the Centre for Research, Development and Innovation, where we are working with new materials that provide solutions that the automotive industry needs.
Since the 1960s, plastics have changed the bodywork structure and allowed Original Equipment Manufacturers (OEMs) to modular assembly while reducing manufacturing costs. Plastic interior parts provide not only comfort and style, but also ergonomics, noise control and increased safety.
Polymers offer more design freedom than metals, are recyclable, abrasion resistant, durable and vibration resistant. They combine many features, which has led to a paradigm change in bodywork design. Currently, among the approximately 30,000 or so parts that the car consists of, one third is made of 39 different types of plastic. 70% of them are made of polypropylene, polyurethane, polyamides and PVC.
Article Six trends impacting the global automotive plastics market in the new decade, published by Plastics Today, highlights the major innovations that will contribute to the continued increase of plastics in the automotive industry, according to the Automotive Plastics Market Research Report prepared by Global Market Insights.
Demand for polypropylene will increase continuously as new applications will be found both inside and outside vehicles and under the bonnet, where plastics will replace some metal parts. According to the report, the greater popularity of electric cars will also increase the use of polystyrene in engine parts because, in contrast to internal combustion engines, electric motors do not require heat resistance. On the other hand, it is expected that EPP and EPS will replace ABS in decorative parts of the interior due to their shiny appearance.
Freedom of creation
In combination with digital technology, plastics enable the manufacture of parts with a more complex and organic geometry through 3D printing, layer by layer. It gives designers more freedom of creation, applicable to the latest cars we can already find on the market. We see this reflection in prototypes and concept vehicles.
Functional surfaces that integrate electronics with plastics begin to be a reality. In the long term, the buttons on the dashboard will disappear, providing great freedom in designing modern car interiors.

An example of a concept car which benefits from this creative freedom is the Mercedes-Benz VISION EQS. Thanks to new technologies, it combines various materials in the search for sustainability, inside the car using: maple wood from German forests together with plastic from recycled plastic bottles (PET). Whereas the roof is the result of a special development project that combines high quality textile material to which recycled plastics found in the sea have been added.
Design freedom, new, bolder and more functional aesthetics, greater safety, reduced weight and thus fuel consumption, commitment to sustainable development … This is how plastics are revolutionising the automotive industry.