Today's automotive industry faces many environmental and sustainability challenges. Recycled plastics are seen as one of the solutions that can help us limit negative environmental and climate impacts from industry, especially when it comes to manufacturing automotive parts.
What makes recycling of plastics so important?
Plastics recycling is crucial from the point of view of the challenges and forecasts for the automotive industry. The process reduces the amount of landfill waste, as well as the need for extracting and processing raw materials, which helps us reduce our greenhouse gas emissions. Given that the use of plastics in automotive constructions is increasing, their reuse has the potential to yield a significant reduction of carbon footprint. This is possible due to the fact that recycling is less energy-intensive than producing new plastics out of virgin raw materials. With the new EU laws in place, vehicle manufacturers are required to increase the share of recycled plastics in their products. What is more, the End-of-life vehicles Regulation adopted in May 2021 calls upon manufacturers to manage the disposal of their products and bear the financial burden of recycling.
Disposal of automotive plastics
The disposal of automotive parts made of plastic is a complex process that starts with proper waste segregation and processing of the materials. The first stage requires removing individual components such as bumpers, grilles and scuff plates. The materials are then separated and carefully sorted based on type and quality. In the next stage, the materials are recycled or – if recycling is not an option – they are transported to the proper landfills.
It goes without saying that automotive plastics disposal poses a number of challenges, which stem from the fact that modern cars are highly complex products, which are made out of a wide variety of materials – that alone makes dismantling and recycling very difficult. Parts comprising multiple plastics or materials containing harmful substances, including phthalates and bisphenol, are most likely to end up in landfills, which results in the threat of them leaching into the soil and polluting the environment. These days, companies are making every effort to ensure that vehicle parts are made of single materials or designed in a way that makes them easy to dismantle and recycle.
Plastics processing in the automotive industry
Processing plastic waste opens up new opportunities for innovation in the automotive sector. With state-of-the-art technologies including chemical recycling, companies are now able to recover high-quality raw materials out of post-consumer plastics to reuse them in the production of a full range of car parts.
Injection moulding remains one of the most popular methods of processing and forming plastic elements. In the process, thermoplastic materials are injected under high pressure into a mould, where they are left to harden in the final shape. The introduction of this technology enabled mass production of components characterised by different sizes, as well as complex shapes.
These days we are seeing a growing popularity of plastic injection moulding technologies, which enable making parts out of materials such as EPP and EPS. The process requires injecting a foaming material and a blowing agent under low pressure into a mould. Once the part has cooled down, it can be removed from the mould. The resulting parts are characterised by high durability, as well as light weight due to their cellular structure. These days, EPP parts are increasingly used to build passive safety system components – bumper dampers and seat cushions.
Other processing technologies used in the automotive sector include extrusion, which enables manufacturing long parts like mouldings and profiles. Some components are made using CNC machining, which allows for precise milling, cutting and shaping plastic parts; however, its use is usually limited to prototyping and small-batch production.
Turning plastic waste into car parts
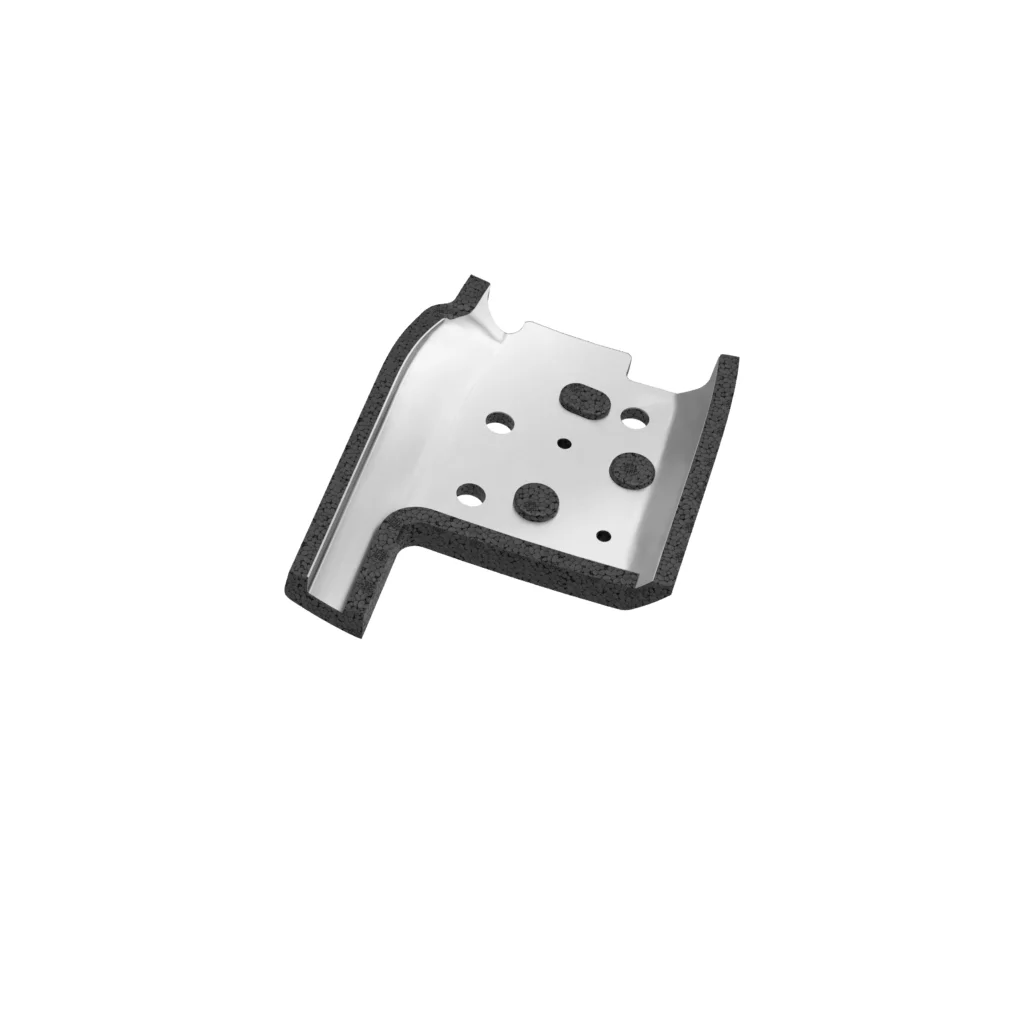
In most cases, the process of turning plastic waste into new plastic car parts comprises several key steps. It starts with collecting plastic waste and transporting it to the recycling plant, then sorting plastics by type, decontamination and cleaning, shredding, melting and reforming into pellets that can be used as raw material for making new plastic products. Sorting is key – that is when recyclable plastics are separated from other waste. This step is crucial for the success of the entire process, as different types of plastic are characterised by different properties and thus have to be processed separately. This is followed up by mechanical, chemical and energy recycling.
The first method remains the most popular and the simplest of all – the waste is shredded into pieces, then melted and remade into plastic pellets or flakes. These can be then used as raw materials for manufacturing new parts. The chemical method entails decomposing plastics using pyrolysis (high-temperature processing in an anaerobic environment) as well as hydrolysis (processing involving water). Chemical recycling of plastics enables recovering raw materials in the cases where mechanical processing would not be the optimal choice. Energy recycling is employed when other methods cannot be used. The combustion of end-of-life plastics yields energy, which is still a better alternative to storing them in a landfill.
Unfortunately, one of the challenges is the lack of uniform standards for plastic recycling in the automotive industry – different countries and companies use different methods and processes to achieve their objectives. What is more, some plastics are more difficult to process than others, which affects the cost and efficiency of the process. What bodes well for the future is the continuous development of the new methods and processes.
Economic and environmental benefits of making automotive parts of recycled plastics
The production of car plastics yields a number of economic and environmental benefits, the most important of which is reduced need for non-renewable raw materials, which translates into lower consumption of natural resources and furthers the objectives of a circular economy. Key economic benefits include lowering the need for virgin raw materials and production costs, as processing existing plastics can be significantly cheaper than producing new material out of fossil fuels.
What is more, consumers are increasingly paying attention to the environmental and sustainability concerns, which means that the market for recycled products is growing. Environmental benefits include reducing the amount of waste going to landfills, curbing environmental pollution and lowering the carbon footprint. Recycling lowers greenhouse gas emissions associated with conventional manufacturing processes. As an additional benefit, this reduces the need for natural resources – reusing and reprocessing secondary raw materials means that they are not required in the manufacturing process. In other words, low-emission vehicles and the continued use of plastics in the automotive industry largely depend on recycling.
The future of recycling plastics in the automotive sector – the future of parts manufacturing
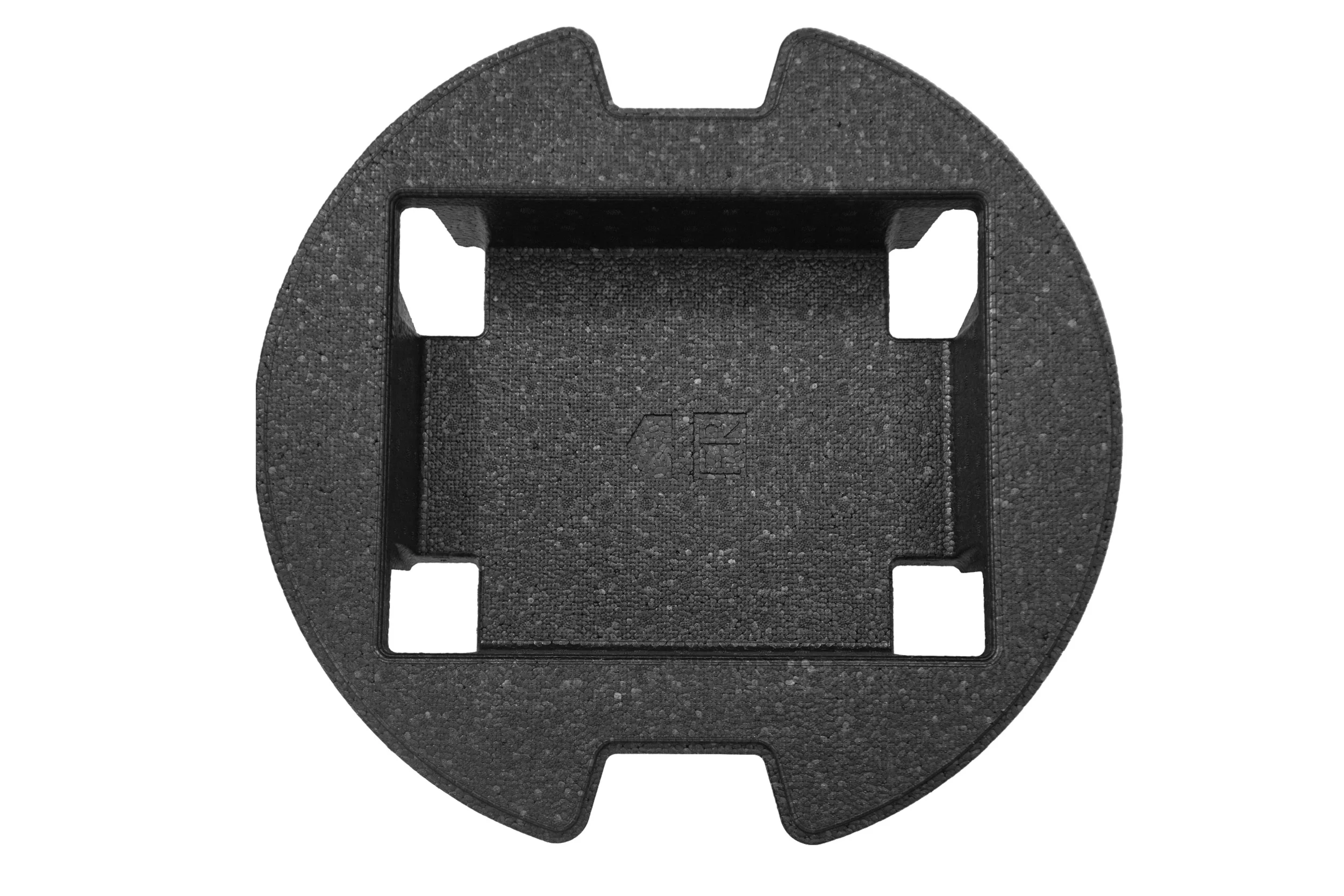
The future of recycled car plastics seems to be very promising and the potential feels boundless. Electric cars, 3D printing and sustainability are driving innovations that could change the way automotive parts are manufactured. An ever-growing number of companies claim to be increasing the share of recycled materials in their products.
At Knauf Industries, we produce car parts made of sustainable plastics for the automotive industry, among other things, using innovative rEPP plastic with the addition of post-consumer recycled materials. Using these materials makes it easier for manufacturers to comply with European Union regulations. The new laws in force in the EU require manufacturers to increase the share of recycled plastics in their products to 6% by 2025 and 25% by 2030. This translates directly into the development of the plastics sector in the automotive industry – according to estimates, it might be worth as much as $68.6 billion by 2026.
Other interesting and promising solutions include bioplastics or sustainable biomass plastics such as NEOPS®. All thanks to their properties and performance that matches or even exceeds conventional counterparts while ensuring a lower carbon footprint. The raw materials used in the production process of traditional polystyrene are replaced with non-food green waste in line with the Mass Balance principle. Unlike conventional plastics derived from fossil fuels, these new materials do not require any natural resources and their production is less harmful to the environment. What is more, all automotive EPP and EPS car components are fully recyclable, which makes them a sustainable solution.
Seeing how today's cars contain more and more components made of plastic, including interior trim, bumpers, headlights, intake manifolds and insulating mats, recycled plastics seem to be an important step towards more sustainable manufacturing.