The request for quotation and the feasibility study of projects for the automotive industry is the beginning of a complex and multi-level process, which is expected to result in the production of products and services perfectly suited to the customer's needs. At Knauf Industries we have developed a multi-stage, proactive approach involving a comprehensive needs analysis and support of business partners with our knowledge, experience and technological know-how at every stage of project implementation.
The stage of implementation of serial production of components in our plants is only the penultimate link in the implementation of projects entrusted to us by customers from the automotive industry. Our comprehensive experience and know-how in the production of injection-moulded components, as well as in-depth knowledge of the processes and standards applicable in the automotive industry have enabled us to develop a proven in practice, multi-stage approach to order handling. It assumes thorough quality control in each phase, close communication with the customer, full transparency and process predictability. Our multidisciplinary team takes care of every link in the process, from the analysis of the feasibility of the order, through the optimal adjustment of production tools, the production of injection moulded parts in the factory, to the aftermarket service and taking care of serial deliveries to the customer at strict intervals. How do we do this step by step?
Analysis, information flow and full synchronisation of activities are the basis for production in the automotive industry
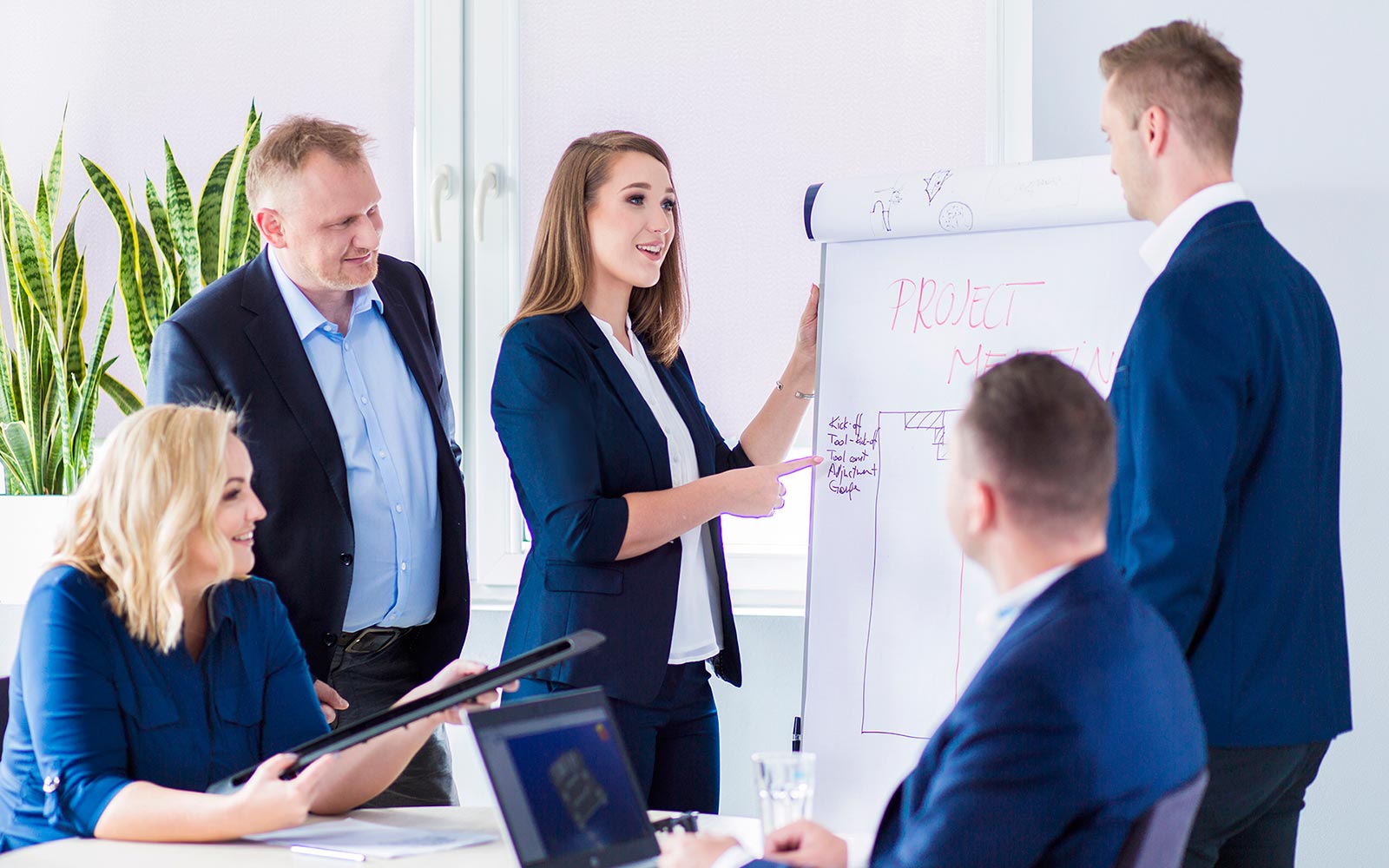
Reliability of deliveries, timeliness, absence of quality defects and full compliance of product characteristics with the specification are necessary conditions on which cooperation between automotive companies is based. At Knauf Industries, we offer much more – a multidisciplinary approach that ensures full process security and its optimisation, which translates into time and cost savings for the customer. The basis of our activities is carefully thought-out organisational structure composed of high-class specialists combining technical and business competences, who handle the project from the enquiry to the completion of after-sales service. The correct flow of information between Knauf Industries and the customer is ensured by a well-integrated team consisting of a key account manager, project manager and plant customer service. Already at the stage of a request for quotation a meticulous analysis of production feasibility is carried out. During this analysis, a computer simulation of injection moulding – Mold Flow – is created, which allows to assess the technical possibilities of manufacturing a product with defined parameters, select the appropriate technology and materials and optimise production costs. If necessary, we propose modifications of the injection moulding part in order to obtain the best possible results. Only after such analysis is an offer tailor-made to the customer's needs submitted, taking into account all possible aspects.
Side by side, which means from the approval of injection mould production to serial production
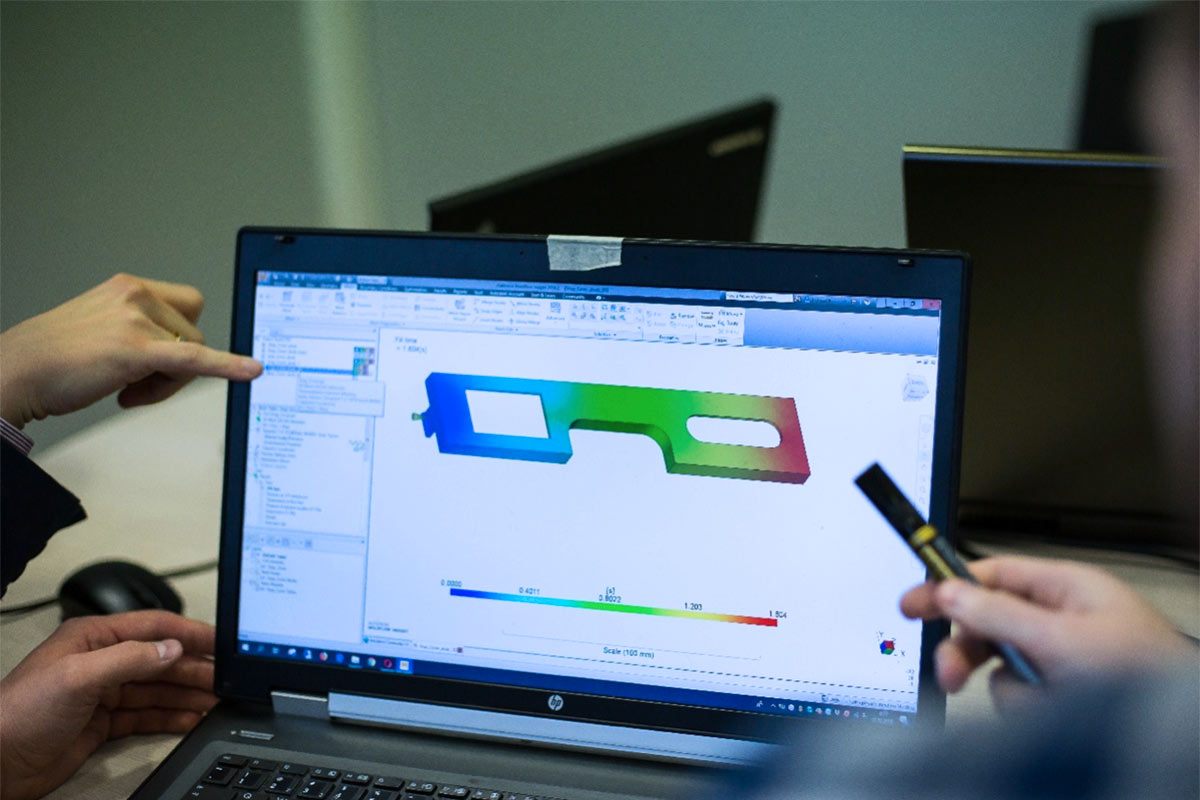
The acceptance of the offer by the customer opens a new stage, which is the production of the tool. A team of specialists from Knauf Industries supervises the whole process of construction and production of injection moulds in tool shops located in Europe and China. We assess the quality and make the necessary optimisations to ensure the required product parameters and the correct operation of the mould itself in technical terms throughout the project life cycle. Then we carry out the first production tests to check the compliance of the component with the documentation. We send the samples made in this way for the customer's approval and if necessary, we make the indicated changes.
The procedure for tooling tunning, consisting of testing, quality assessment and corrections, is repeated as necessary until the sample is fully accepted in every detail. Many years of experience and know-how of our technical department allow us to achieve the highest possible results, which translates into shorter acceptance time and acceleration of the whole process. Additionally, if the injection moulded component requires further processing in the form of tape application or texturing, we execute the whole order on the basis of a project prepared by our team and approved. If necessary, we also provide the service of applying paint coatings in an external paint shop (water-based paints, solvent-based paints, UV, High Gloss, Soft Touch Feeling, hot stamping, laser marking, PVD).
Production process of injection moulded components under full control
The customer's approval allows the tool to be used to produce the first parts at the Knauf Industries plant in Wrocław. The documentation approving the product for production, together with the measurement reports, is developed by our specially appointed, qualified design team. However, before the serial production stage, automotive customers not only accept the production result, i.e. the product itself, but also have the opportunity to assess all related processes on site in our plant. We provide them with an insight into our quality management system according to ISO 9001 and IATF 16949:2016, the conditions of automotive production, the level of training of the team or production capacity. After meeting all the conditions and final approval of the whole process by the customer, we start production according to the planned schedule. The highest production standards are ensured by the same quality engineer who takes part in the giving an opinion on the project at the proposal and implementation stage. It guarantees a full flow of information also in the subsequent stages. Completion of the project and the transfer to serial production takes place after a few months. This ensures 100% verification of correct implementation at all organizational levels and guarantees that the customer's expectations are met in every aspect. Timely deliveries are made by our qualified logistics and planning department. However, our customer care does not finish there – even after the serial production stage is completed, we provide full after-sales service.