The floor for a car is what the foundation is for a house. The floor plate is often the starting point for the design of a car's body, and to a large extent determines its comfort. However, effective sound insulation does not have to involve increasing the vehicle's own weight. Our EPP foam floor panels perfectly combine low weight with sound absorption, and at the same time perfectly smooth out any irregularities.
Car floor soundproofing at the manufacturing stage – how to effectively protect the floor in the car?
The design of the car floor is vital to the size of the car, the spacing of the wheels or the pillars supporting the roof. The car floor also has a significant impact on the organization of the car interior and on driving comfort. It insulates the passenger compartment from noise while driving and thus affects its acoustics.
What does good soundproofing of the floor and car body elements depend on?
However, effective soundproofing of a car floor is not the norm. The need to lower the vehicle's own weight forces the use of a thinner insulation layer, which may result in worse acoustic insulation. When designing the floor and the body of a car, its mechanical strength and the effectiveness of protecting passengers against the effects of a possible accident have become a priority. However, there are solutions involving modern materials, which combine low weight, high acoustic insulation, and at the same time the ability to dampen impacts and shocks. The technologies applied help to effectively soundproof not only the floor, but also the engine and wheel arches, as well as to soundproof car doors.
How are car floorboards made and what materials are used to soundproof them?
In the past, car floor panels were based on a simple frame structure. Today, a car floor is a solid, stiffened platform which must meet a number of complicated requirements related to the tensile, bending and torsion strength of its individual components. Achieving strictly specified parameters must be preceded by very complex mathematical calculations which take a lot of time, even for modern computers. For this reason, the so-called shared car floor plate was created, which can be used in different models, versions and even brands of cars. This significantly reduces the cost and production time of the car. Already at the beginning, the constructors know, among other things, where the engine will be mounted. This allows various design teams to work in parallel on all aspects of car construction, from the drivetrain and suspension to the shape of the body, the arrangement of the car interior and the routing of cables for electronics or, for example, the underfloor GPS, often used by car manufacturers. If necessary, the floor plate of the car can be lengthened or widened depending on the size of the car or requirements related to e.g. its road grip. Depending on the size of the car, different plate thicknesses are also used, which can increase the weight of the car. For this reason, however, in some vehicles this component may provide poor protection against noise, which affects driving comfort and safety.
Does car floor soundproofing influence a car's weight?
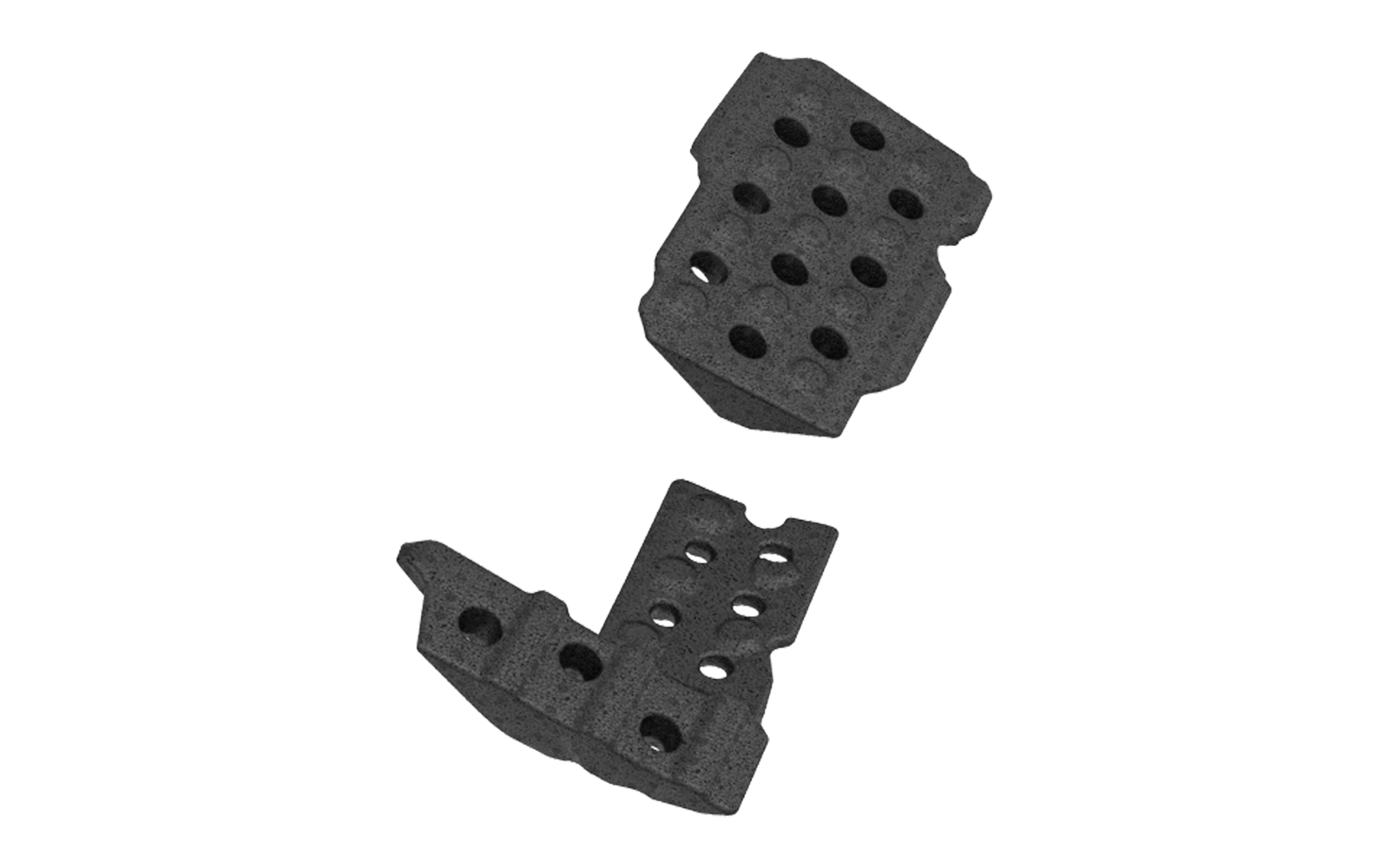
Effective soundproofing of the car floor is not common in every car segment. Good soundproofing materials can be found in premium car models. In most cases, the factory soundproofing of the car floor generally performs poorly.
Methods to soundproof a car floor – are soundproof floor mats effective?
Acoustic insulation in the form of felt and bitumen mats, once commonly used, have been replaced by a rather thin layer of felt and insulation tapes. This change was dictated by the fact that these materials are quite expensive, impractical and relatively heavy. Felt mats are absorbent, and when soaked with water not only add to their weight, but can also cause an unpleasant odor inside the car and increase the risk of rust in the car floor. This sometimes even results in the need to replace the floor of the car. Bituminous mats, on the other hand, require problematic hot installation and tend to crack.
European Union requirements and materials used for soundproofing car floors
Above all, however, the gradual phasing out of these materials has been driven by the requirements of the European Union, which obligate manufacturers to reduce vehicle emissions and use recyclable materials. So how to meet the new standards and avoid the need of drying the car floor once it has become wet in order to prevent rust? In this context, EPP foamed polypropylene parts have proven to be an excellent alternative and have much to offer modern vehicle manufacturers. This material is resistant to water and does not absorb moisture, which eliminates the risk of corrosion of the car floor
Read more: How to soundproof a car? Recommended materials for soundproofing the interior of a car
EPP flooring components – modern car floor soundproofing
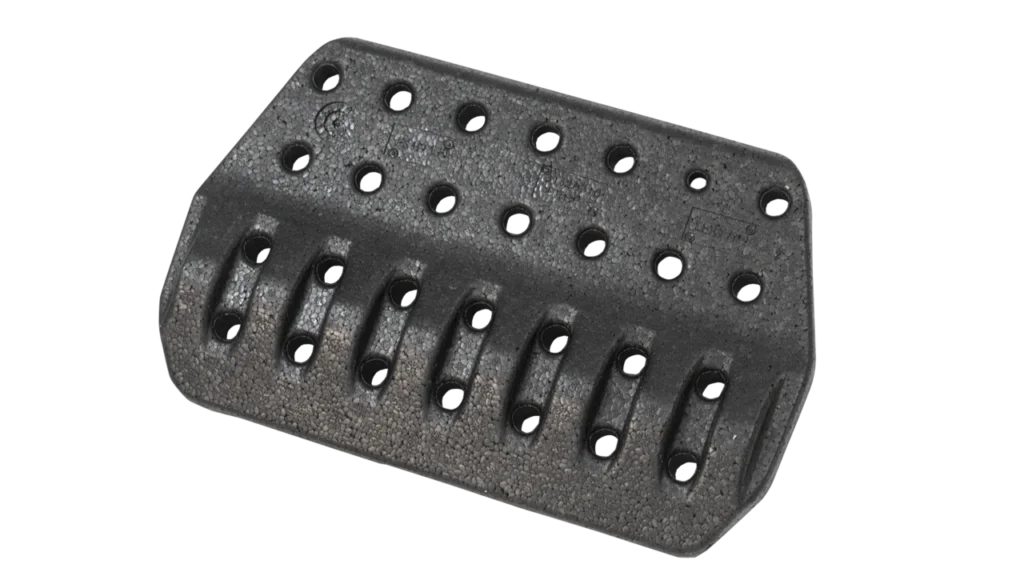
Foamed polypropylene EPP is a material filled with 95% air, which determines its excellent properties related not only to acoustics, but also thermal insulation or weight. It has high mechanical strength, and under the influence of mechanical factors does not undergo permanent deformation, but returns to its previous shape. This makes it an important function in passive car safety systems. In the process of pneumatic molding of floor components made of this material, we can continuously increase its density parameter, obtaining the expected acoustic or mechanical parameters, depending on a specific application. The method of pneumatic forming allows for flexible adjustment of filling shapes, depending on the shape of the car floor plate or wiring design. Elements with pre-molded wire harness slots can effectively protect sensitive electronics from damage or extreme temperatures. The multifunctional elements can take on even the most complex shapes, making it possible to compensate for any unevenness in the car's floor plate and freely design individual interior organization.
Our experienced project team guides the customer through every stage of component manufacturing implementation, from the feasibility phase of the project through its optimization to production preparation and coordination of injection mold manufacturing. Our state-of-the-art manufacturing facilities are equipped with the latest technology robots and production machinery to guarantee high-quality EPP automotive parts. Contact us for more information.