Looking at the evolution of the flagship models of the popular compact city cars over the last decades, one can see that their profiles have not only become more rounded but also are significantly longer and wider. Where does it come from and what challenges does it pose to designers in the automotive industry?
Back in the 1980s, cars had a much simpler design, characterised by sharp, geometric lines. Today, when you look at the modern equivalents of the classic models, you get the impression that they are more “inflated”, higher and longer. This is related, among other things, to the requirements of modern consumers, who are looking for more comfortable and better-looking cars with a spacious interior. This is particularly true for the B segment.
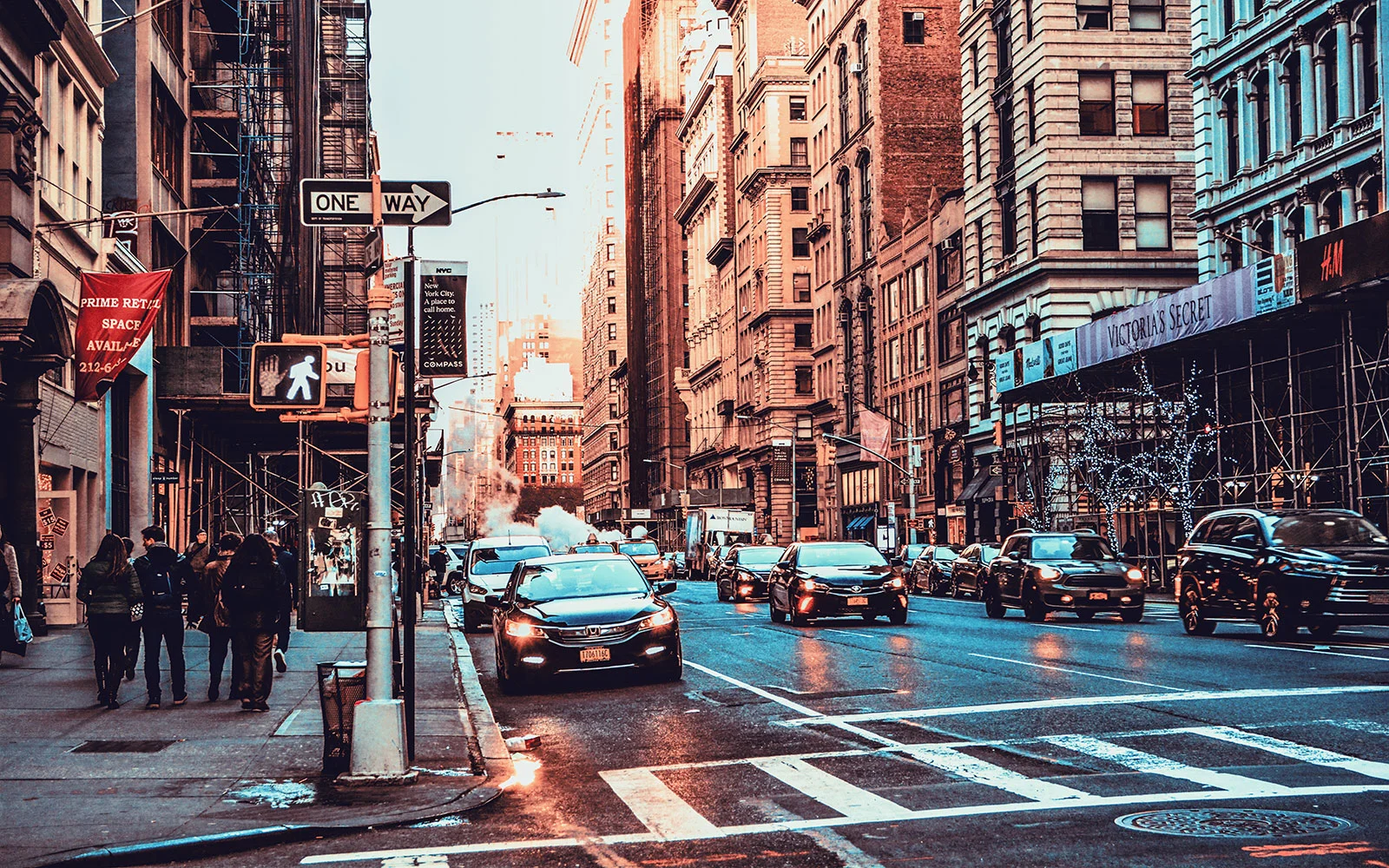
Small city cars have grown so much during the recent years that they have come closer to the C segment, i.e. some crossovers or SUVs. Enlargement of the outer dimensions of the car translates into a larger wheel track width and wider tyres, and this can make it very difficult to manoeuvre on crowded city streets. Increasing complete vehicle kerb weight also means greater combustion. All of this means that the automotive industry has to look for optimal solutions to reconcile the requirements of safety and comfort for users with the stricter regulations on CO2 emissions.
Why are compact city cars still growing?
The most important reason for the continued growth of city cars is the safety requirements. More rounded car contour is the result of carefully designed crumple zones in order to protect passengers from side impacts. The fact that today's cars are increasingly packed with sensors and electronics, which also require space for installation, is also significant. In addition, there is a psychological factor – we simply feel safer in a bigger car. This is why recent years have seen a move away from the smallest urban A-class cars to the “enlarged” B and C segment, which offers more space in the cabin and trunk.
Following the demands for comfort, the width of the car seats has increased and the equipment has become richer. Importance of the Premium segment is now growing in the automotive industry, and globalisation is making car manufacturers strive to unify their offers directed to Europe, Asia and America. At the same time, the American market is the most important one, and it is definitely dominated by large cars. Among the reasons for increasing the size of cars, we can also mention the most prosaic one – the growing average height of Europeans. It is estimated that since the second half of the nineteenth century it has increased by around 10 cm. Cars must therefore be longer, and to maintain proportions – they have also become wider.
How big will the cars of the future be?
Although it would seem that the cars of tomorrow will be much bigger, the maximum in this respect has already been reached. Designing the size of a car is limited by the aspects of the infrastructure development. The space on the roads and parking lots does not increase, in fact in many European cities the trend is the opposite. City centres are closed to car traffic and the trend towards a healthy lifestyle causes the increase of the number of cycle paths. Therefore, manufacturers are also faced with the challenge of reducing combustion and CO2 emissions, yet heavier vehicles require stronger engines.
Cars will certainly not get smaller, but their shapes may change. More stream lined and narrower body silhouette would reduce aerodynamic resistance, which would translate into lower combustion. The use of narrower tires, as currently seen on some electric car models, also serves this purpose, which contributes to reducing rolling resistance. However, the key element of “slimming” the cars is primarily the use of lighter, yet highly durable materials, such as polypropylene foam (EPP).
Lighter car seats and safety systems in cars
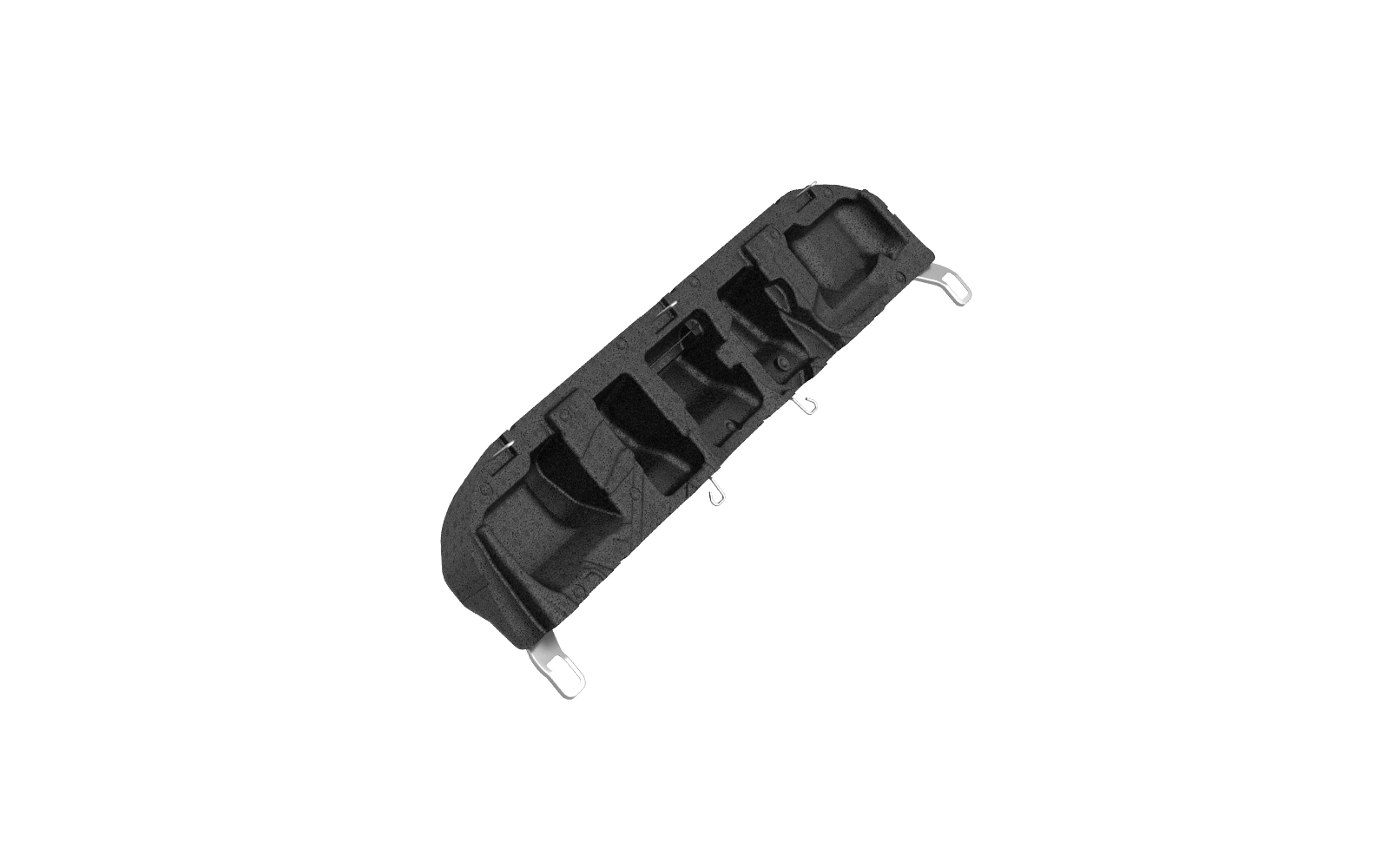
Increase in the average complete vehicle kerb weight is not only due to the fact that the dimensions are increasing, but also to better equipment, which is supposed to ensure more comfort and safety. In addition to the fact that the seats are wider, they often have additional mechanisms allowing for adjustment in a larger number of positions. Pillars and reinforcements are becoming increasingly thicker, so that the cockpit may form a strong “cage” protecting the driver and passengers in case of a collision.
Another increasingly common issue is the acoustic protection of the cockpit, which would require additional kilograms of insulation. In all these areas, modern polypropylene foam (EPP) components produced among other locations at Knauf Industries in Wrocław and Adamowice are perfectly applicable. This material combines resistance to mechanical damage and deformation with a low weight compared to traditional seat fillings, impact damping elements or sound insulators. The material offered by Knauf Industries is available in a wide range of densities – from 15 to 250 grams per litre. This allows the elements produced from it to be given strictly defined properties related to resistance to strong impacts, sound damping or flexibility. Strong advantage of this technology is that EPP moulded parts can be easily combined with other materials. Even very complex multi-component parts, e.g. with aluminium reinforcements, ABS surfaces or fabric finishes, can therefore be produced quickly and economically in a single, complex production process.