Cars manufactured in the last decade have many safety systems that we do not even notice during everyday driving. One such invisible element of passive safety is the bumper that is harmoniously integrated into the vehicle's body. What is it made of and what is its function?
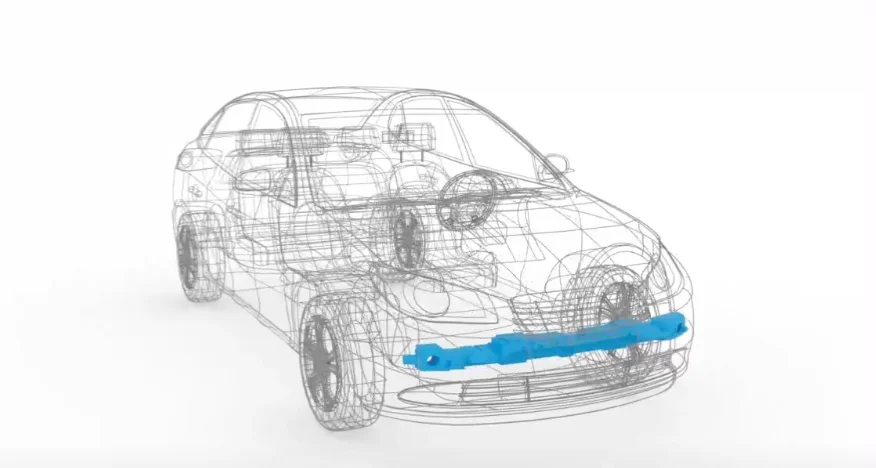
Looking at today's complex designs of car bumpers, it is hard to believe that in the very beginning they served only as a subtle decoration of the vehicle, providing no protection at the time of a collision. As early as 1910, car manufacturers began using strips of steel attached to the rear and front of the vehicle. Vehicles at the time were developing minimal speeds, and the bumper was only to prevent costly repairs to the car in the event of a possible contact with an obstacle.
As the automotive industry grew, these designs became heavier and more decorative to take the shape of a "slimmed down" chrome piece in the 1960s. The first plastic bumpers were introduced in the late 1960s and early 1970s by the General Motors brand. They were to absorb the energy of a low-speed collision and not be permanently damaged in the process. Today, modern bumpers are integrated into the body of the car and conceal many different functions. Their primary task is to ensure safety – not only for vehicle passengers, but especially for pedestrians.
Read also: From metal to plastic bumpers: in search of the balance between aesthetics and safety
How a car bumper is built – not just plastic

Modern car bumpers must have a properly resilient design that acts like a shock absorber in a moment of impact. Their main element is a steel structural section, the so-called bumper beam. This reinforcement is mounted horizontally on the front and rear panel of a car and carries the heaviest load during a crash. It is covered from the outside with a flexible EPP foam bumper padding.
In the event of an accident, the bumper padding dissipates kinetic energy and reduces noise, even during everyday driving. This element is usually given a profiled shape that corresponds to the geometry of the outermost part of the bumper, which is injection moulded cover made of thermoplastic materials such as polypropylene (PP) or polycarbonate (PC). Nowadays, various electronic elements such as parking sensors, reversing camera, fog lights, and sometimes additional air intakes are additionally built into the bumper's construction.
Safety bumper – what are its functions?
The primary function of a car bumper is to offset the effects of a possible collision, both for passengers and pedestrians. Designers and manufacturers in the automotive industry are constantly looking for the right design and material solutions to balance stiffness and flexibility with hardness and strength. Generally, the stronger and tougher the bumper design, the better it protects the structure of the car; however, it can be dangerous to the other vehicle and pedestrians.
Considering the fact that most often bumpers break during high-speed crashes, they serve little protective function for the vehicle passengers in such situations. The main crash force is taken up by the reinforced frame and the control crush zones, while the bumper is only the first barrier during contact. However, this initial dampening is to give the airbags time to deploy. A car bumper nowadays mainly serves as protection in case of low-speed collisions. Though, the shape and curvature of the car's front panel and the design of the bonnet are primarily intended to minimise pedestrian injuries in the event of a collision.
Bumper structure to be repaired?
According to the U.S. National Highway Traffic Safety Administration (NHTSA), pedestrian crashes increased from 12 to 17 percent of all traffic accidents between 2008 and 2018. The Governors Highway Safety Association points to similarly troubling changes, according to which the number of fatal pedestrian crashes increased from 4 109 to 6 238 between 2009 and 2018. The rise in popularity of more massive SUVs and crossovers, which have a higher bonnet and bumper, is cited as the main reason for this adverse change.
The difference in the position of the bumper beam is also important in the event of a collision between SUV and a smaller passenger car. To the extent that even at low speeds the structure of the latter can be significantly damaged. Given the growing popularity of this type of car in Europe as well, appropriate solutions will be needed. Although new cars are equipped with active systems to protect pedestrians, by automatically braking when danger is detected or warning the driver, they do not always work properly or fast enough. The above data shows how crucial is a properly designed bumper and the entire front panel of a car.
What kind of material will work best for a bumper production?
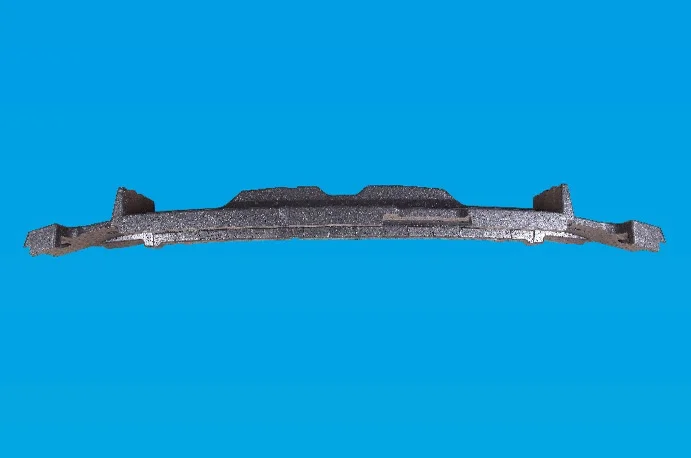
The most important role in terms of pedestrian safety is played by the flexible bumper padding, which acts as a shock absorber. In this area, foam materials are often used. Although alternative materials are being sought, these are still niche solutions. Research has been conducted, for example, on a bumper made of oak cork, which was to be designed especially for cars with a high bonnet, or a crash absorber with special rotors to dissipate kinetic energy. So far, EPP foam has proven to be the best material for bumper padding.
This material combines high mechanical strength with high elasticity to effectively dampen impact energy while being the most pedestrian friendly. The wide range of possibilities offered by the foamed polypropylene EPP processed in Knauf Industries' plants allow for easy adaptation of all the properties of foam damping elements, bumper paddings and grille covers made of it – from its low weight to its mechanical strength and elasticity, to its noise damping and even thermal insulation properties.
EPP does not crumble or disintegrate on impact, but deforms in the short term and immediately returns to its original shape. Thanks to modern software and 3D visualization techniques it is possible to work out the best solution of shock absorbing elements, which will fully meet the requirements of a given project, both in terms of use and aesthetics.