Rosnące wykorzystanie tworzyw sztucznych w przemyśle motoryzacyjnym jest odpowiedzią na potrzebę zmniejszenia masy pojazdów i poprawy efektywności paliwowej, dostosowania się do najbardziej rygorystycznych przepisów dotyczących emisji gazów cieplarnianych i zapotrzebowania na produkty przyjazne dla środowiska. Tworzywa sztuczne zapewniają jednak również ulepszenia w projektowaniu samochodów, zarówno jeśli chodzi o komponenty wewnętrzne jak i zewnętrzne.
Obecnie projektanci branży motoryzacyjnej poszukują lekkich materiałów, które poprawią projektowanie, produkcję i wydajność formowanych części. Przez dziesięciolecia zastępowali ciężkie metalowe elementy tworzywami sztucznymi, takimi jak polipropylen (tworzywo termoplastyczne) i kompozyty wypełnione włóknami. Praktyka ta rozszerza się, ponieważ producenci starają się zwiększyć zastosowanie polimerów w przypadku zewnętrznych części pojazdu i akcesoriów wewnętrznych.
Dzięki postępowi technologicznemu inżynierowie mają szerszy zakres nowych i lżejszych opcji, oferujących większą swobodę projektowania, również w częściach mechanicznych, które są zgodne ze strategią redukcji masy. Analiza najnowszych osiągnięć w zakresie redukcji wagi samochodów przedstawiona została w artykule Advanced Polymers Drive Automotive Lightweighting.
Nowe zastosowania tworzyw sztucznych
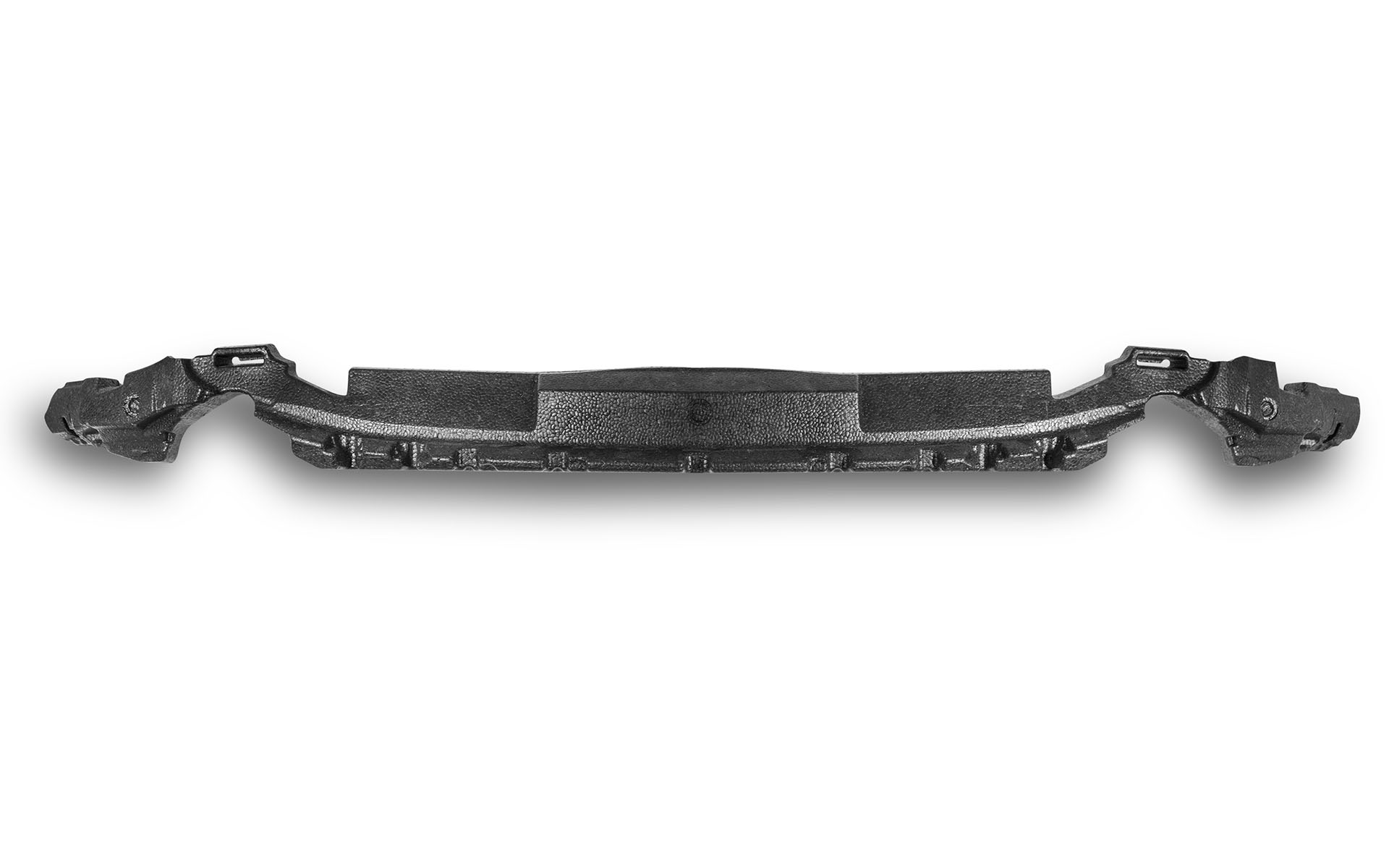
W Knauf Industries Automotive gromadzimy doświadczenie w projektowaniu i produkcji samochodowych komponentów z tworzyw sztucznych, rozszerzając zastosowania formowanych tworzyw sztucznych, takich jak spieniony polipropylen (EPP) i spieniony polistyren (EPS). Inwestujemy w innowacje poprzez działania IDLab, Centrum Badań, Rozwoju i Innowacji, w którym pracujemy z nowymi materiałami, zapewniającymi rozwiązania, których potrzebuje przemysł motoryzacyjny.
Od lat 60. XX wieku tworzywa sztuczne zmieniły konstrukcje nadwozia i pozwoliły producentom oryginalnego wyposażenia (OEM) na montaż modułowy przy jednoczesnym obniżeniu kosztów produkcji. Plastikowe części wewnętrzne zapewniają nie tylko wygodę i styl, ale także ergonomię, kontrolę hałasu i zwiększone bezpieczeństwo.
Polimery oferują większą swobodę projektowania niż metale, nadają się do recyklingu, są odporne na ścieranie, trwałe i odporne na wibracji. Łączą one wiele cech, co doprowadziło do zmiany paradygmatu konstrukcji nadwozia. Obecnie spośród około 30 000 części, z których składa się samochód, jedna trzecia jest wykonana z 39 różnych rodzajów plastiku. 70% z nich jest wykonana z polipropylenu, poliuretanu, poliamidów i PCV.
Artykuł Six trends impacting the global automotive plastics market in the new decade, opublikowany przez Plastics Today, podkreśla główne innowacje, które przyczynią się do ciągłego wzrostu liczby tworzyw sztucznych w przemyśle motoryzacyjnym, zgodnie z raportem Automotive Plastics Market Research Report przygotowanym przez Global Market Insights.
Zapotrzebowanie na polipropylen będzie nadal rosło, ponieważ nowe zastosowania będą znajdowały się zarówno wewnątrz, jak i na zewnątrz pojazdów oraz pod maską, gdzie tworzywa sztuczne zastąpią niektóre metalowe części. Według raportu większa popularność samochodów elektrycznych zwiększy również wykorzystanie polistyrenu w częściach silnika, ponieważ w przeciwieństwie do silników spalinowych, silniki elektryczne nie wymagają odporności termicznej. Z drugiej strony oczekuje się, że EPP i EPS zastąpią ABS w dekoracyjnych częściach wnętrza ze względu na ich błyszczący wygląd.
Zobacz też: Części samochodowe z pianek w branży motoryzacyjnej – wytrzymałe komponenty z lekkiego materiału
Swoboda tworzenia
W połączeniu z technologią cyfrową tworzywa sztuczne umożliwiają wytwarzanie części o bardziej złożonej i organicznej geometrii dzięki drukowaniu 3D, warstwa po warstwie. Pozwala to projektantom na większą swobodę tworzenia, mającą zastosowanie do najnowszych samochodów, które możemy już znaleźć na rynku. Widzimy odzwierciedlenie tego w prototypach i pojazdach koncepcyjnych.
Funkcjonalne powierzchnie, które integrują elektronikę z tworzywami sztucznymi, zaczynają być rzeczywistością. W dłuższej perspektywie przyciski na desce rozdzielczej znikną, zapewniając ogromną swobodę w projektowaniu nowoczesnych samochodowych wnętrz.

Przykładem samochodu koncepcyjnego, który korzysta z tej kreatywnej wolności, jest Mercedes-Benz VISION EQS. Dzięki nowym technologiom łączy różnorodne materiały w poszukiwaniu zrównoważonego rozwoju, wewnątrz samochodu wykorzystując: drewno klonowe z niemieckich lasów wraz z plastikiem uzyskanym z plastikowych butelek z recyklingu (PET). Natomiast dach jest wynikiem specjalnego projektu rozwojowego, który łączy wysokiej jakości materiał tekstylny, do którego dodano odzyskane podczas recyklingu tworzywa sztuczne znalezione w morzu.
Swoboda projektowania, nowa, bardziej odważna i funkcjonalna estetyka, większe bezpieczeństwo, zmniejszona waga, a tym samym zużycie paliwa, zaangażowanie na rzecz zrównoważonego rozwoju … Tak właśnie tworzywa sztuczne rewolucjonizują przemysł motoryzacyjny.