Robotization is an inevitable trend in changes in the industry. Even though Poland still has the dynamic development in this branch ahead, more and more companies implement modern solutions of the automatics. An excellent example of this is the Knauf Industries factory in Wrocław, where an advanced six-axis robot has been installed, which performs production of complex expanded polypropylene (EPP) components for the automotive branch.
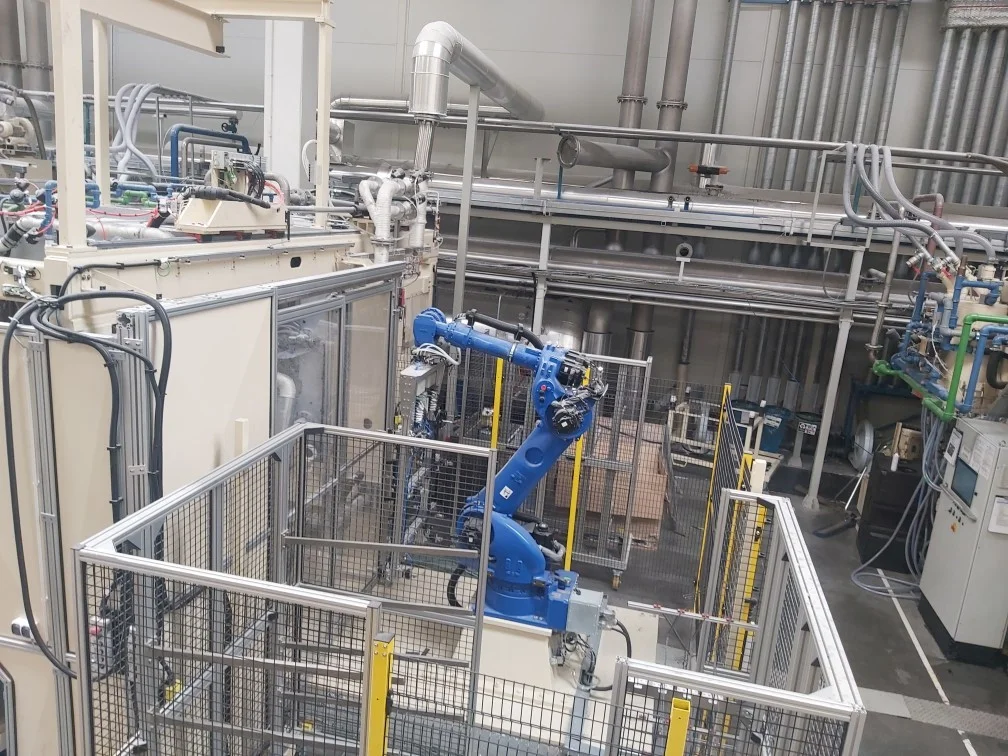
It results from the data published by the International Federation of Robotics (IFR) that in the whole world the year-to-year number of cooperating robots grows by 23% and by 5% for the industrial robots. This dynamic development has its origins not only in demographic factors, such as the process of the society aging and drop in the number of professionally active persons in the consecutive years, but also in striving by the companies to improve reliability and effectiveness of production simultaneously increasing speed of manufacturing and product quality. The robotization is the most preferably used in these branches of industry, in which repeatable manual operations are necessary. The most robotized branch now is the automotive, in which these kinds of solutions have become used in manufacturing of car parts. The first place in this branch is occupied by car manufacturing concerns in Asia.
How does robotization of the manufacturing process look in the world and in Poland?
The unquestioned leaders in the field of robotization are Asiatic countries. The first place is occupied by Singapore where concentration factor amounts 831 of robots per 10,000 employees. In Europe the most robotized industry is in Germany with the factor of 338 robots. Polish contribution in this phenomenon is small nowadays as in 2019 per 10,000 employees there were 42 robots, however there is a growing trend. Still in 2018 this figure was only 36, which means 17% of increase year to year. Polish entrepreneurs more and more frequently reach out for modern solutions of the robotics – even up to 91% of them declares the willingness of complete or at least partial robotization of production.
The benefits that are offered by use of the robots are appreciated especially by the automotive branch, where in series production the emphasis put to maintain the qualitative standards is especially high, due to extremely elevated safety standards. In Poland this regularity is clearly visible as per 10,000 employees of the automotive industry factories, there are as many as 165 robots, which makes this industry the leader in the scale of the state economy. The visible advantage of this industry over the other branches should not surprise anyone also because of the fact that the robotization of the industrial processes took its start just in the automotive branch.
Role of the industrial robots in the automotive branch in the past and today
The first robots were constructed already in the 50-ties of the 20-th century and already within a decade later they appeared in the factories of General Motors and Ford. Then they were treated as a technical curiosity rather than ”complete” workers. Mass application of production robots took place on the break of the 70-ties and 80-ties when other American concerns and then also the European automotive producers followed this path. At that time the objective of the robotization was to increase production and output of factories simultaneously diminishing the unit costs. Today, however, the center of gravity moved towards improvement of the quality of the works, which require higher precision and accuracy of operation. Application of the robots in the automotive branch reduces production cycles even of very complicated components and substantially improves safety of the whole process. A machine does not get tired, slow down the pace and commit mistakes in series, repeatable production when humans take over the control functions.
How do the modern robots look like?
Modern robots cooperate side by side with their human operators, substituting them in monotonous and sometimes physically arduous operations. Currently the most willingly used kind of the robots are the solutions, which use an arm or even two arms form, which can perform multiaxial movements and various high precision tasks. They are so-called articulated robots, five- and six-axial, most frequently applied at operations such as e.g. manipulation, machining, painting, transport and assembly. Their advantages comprise large working space, quick movements, flexible assembly possibilities and the options of obtaining any orientation of the effector, i.e. of the device at the end of the robot arm. The future trend are so called cobots, i.e. the robots collaborating with a human (collaborative robots), and also the possibilities of smooth data exchange with devices, which is offered by Industry 4.0. The development of the robotization is directed towards an autonomous factory, which will execute production entirely on its own, however, as the experts stress, there is still a long way to go.
Larger precision and safety of the manufacturing processes at Knauf Industries, Wrocław
A new generation six-axial robot was applied at the plant of Knauf Industries, Wrocław, which is known for implementation of pioneering technological solutions. It was installed on the production line of car back seats, where operations are performed depending on taking metal frames from a supply trolley and inserting them into an EPP mold. At a large number of repetitions this operation would require much effort on behalf of the employees, related to carrying of the frames and entering with them into the machine, where the mold is located.
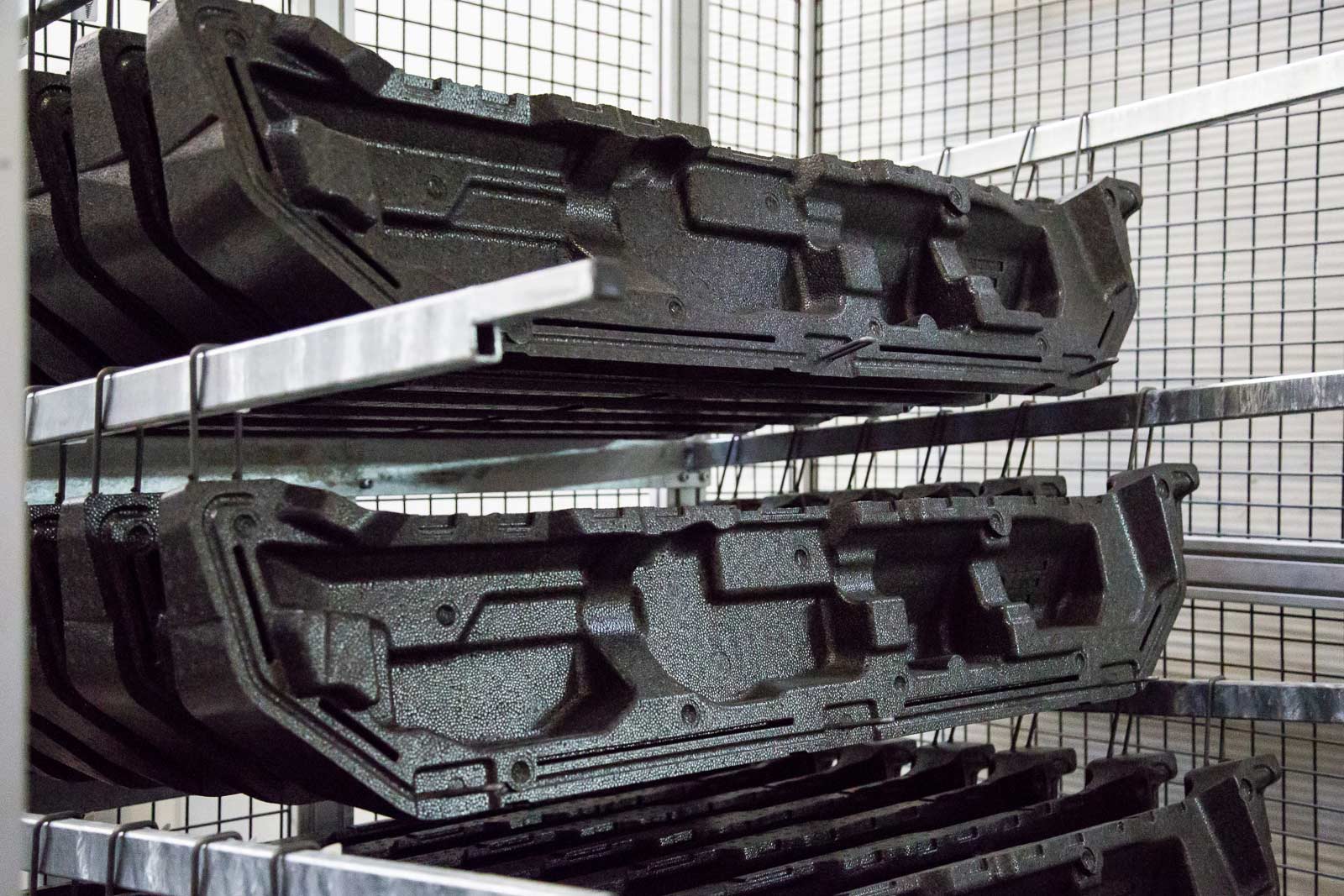
The robot does this task for them with large speed and precision. Its tremendous advantage is the possibility of manipulating the objects in three main axis and a three stage rotation, thanks to which it enables execution of even very complicated, multi-element components. Thus it can be used not only for manufacturing of the seats, but also for all the solutions, which assume connection of complicated shapes and different plastic materials processed at the Knauf Industries plant, such as the EPP with a metal insert or frame or an EPP component with injected plastic. Thanks to it, as a target, it will not be used only at manufacturing for the automotive branch customers, but also for other branches serviced by the Knauf Industries plant, such as e.g. HVAC. It makes it a very flexible and versatile tool, which opens broad production perspectives.