Nowadays, safety requirements and low weight of the car equipment play the most important role in car design. The material that still offers new possibilities for designers in this field is expanded polypropylene foam (EPP). Karwala company in cooperation with Knauf Industries has designed an innovative, ultra-light and durable child safety seat made with the use of modern material which is EPP.
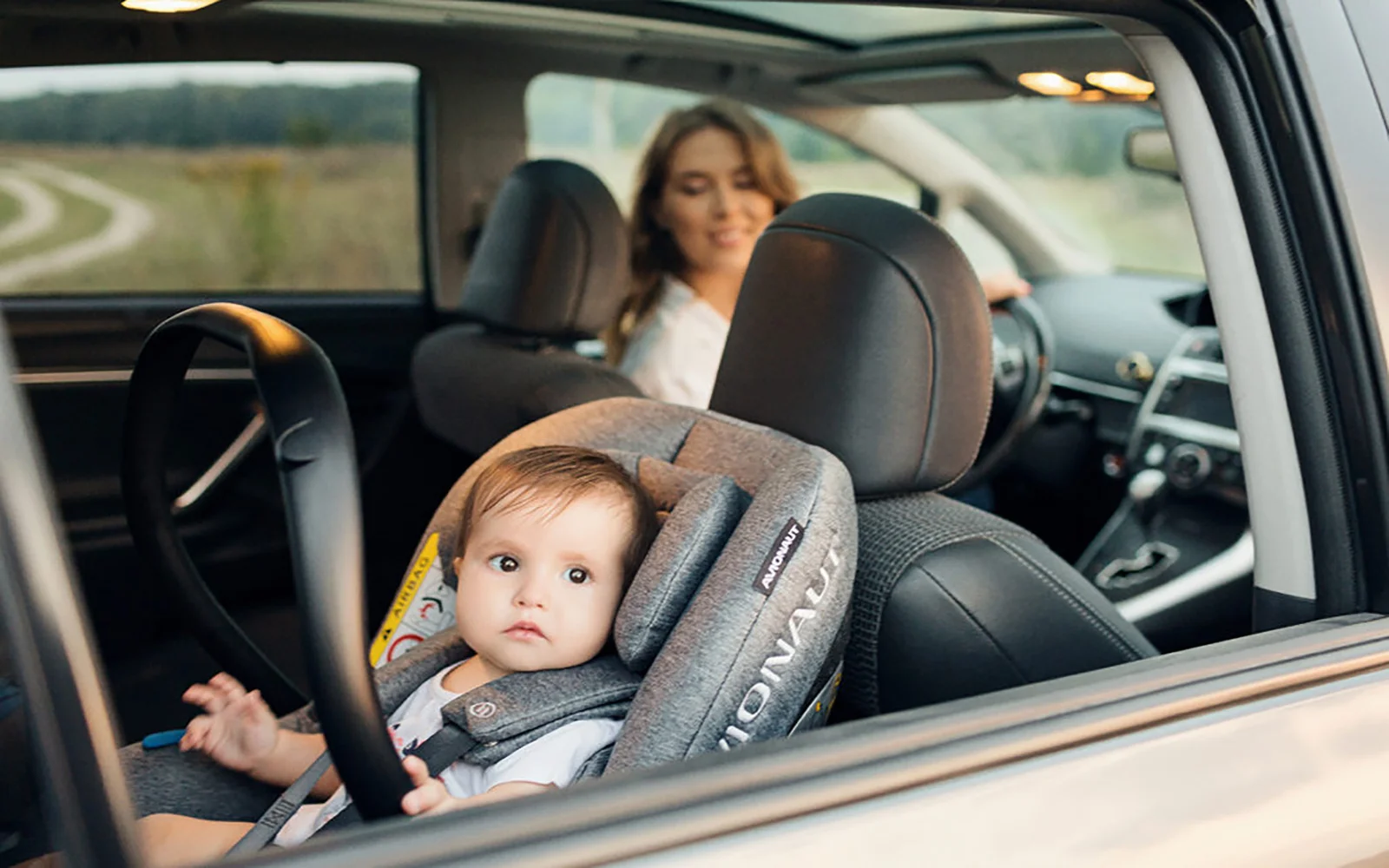
Photo: Avionaut
One of the most important challenges for the automotive industry is to balance the high strength parameters of structural solutions with the need to reduce vehicle weight at the same time. Manufacturers of automotive components are still looking for new material or innovative applications for already known solutions. The growing number of vehicles on the road, the increase in their average power and speed, and the high frequency of travelling with children, are forcing the development of technologies that can provide even better protection of their health and life in unexpected situations on the road. The Knauf Industries pressure moulding technology for car components made from expanded polypropylene foam (EPP) has proven to be the perfect answer to the need to produce a child safety seat that combines extraordinary strength with minimal weight.
Unique lightweight child safety seat with core made of expanded polypropylene (EPP)
The advantages of the modern EPP foam have been appreciated by Karwala company, the owner of Avionaut brand, which developed an innovative model of the Avionaut Pixel child safety seat, distinguished by as much as 40% lower weight than products available on the market until now. The lightest child safety seat on the market for transporting children in the range of 0-13 kg weighs only 2.5 kg, which facilitates its daily use especially for people who do not have much strength. This effect has been achieved by replacing the hard plastic and polystyrene components used so far with a base made of expanded polypropylene (EPP).
The heart of the project is a patented solution by Karwala. The unique parameters of the solution in terms of safety, health care and comfort have been confirmed by crash tests carried out both by Karwala, the owner of Avionaut brand in its own laboratory and by independent global institutions.
Safest child safety seat
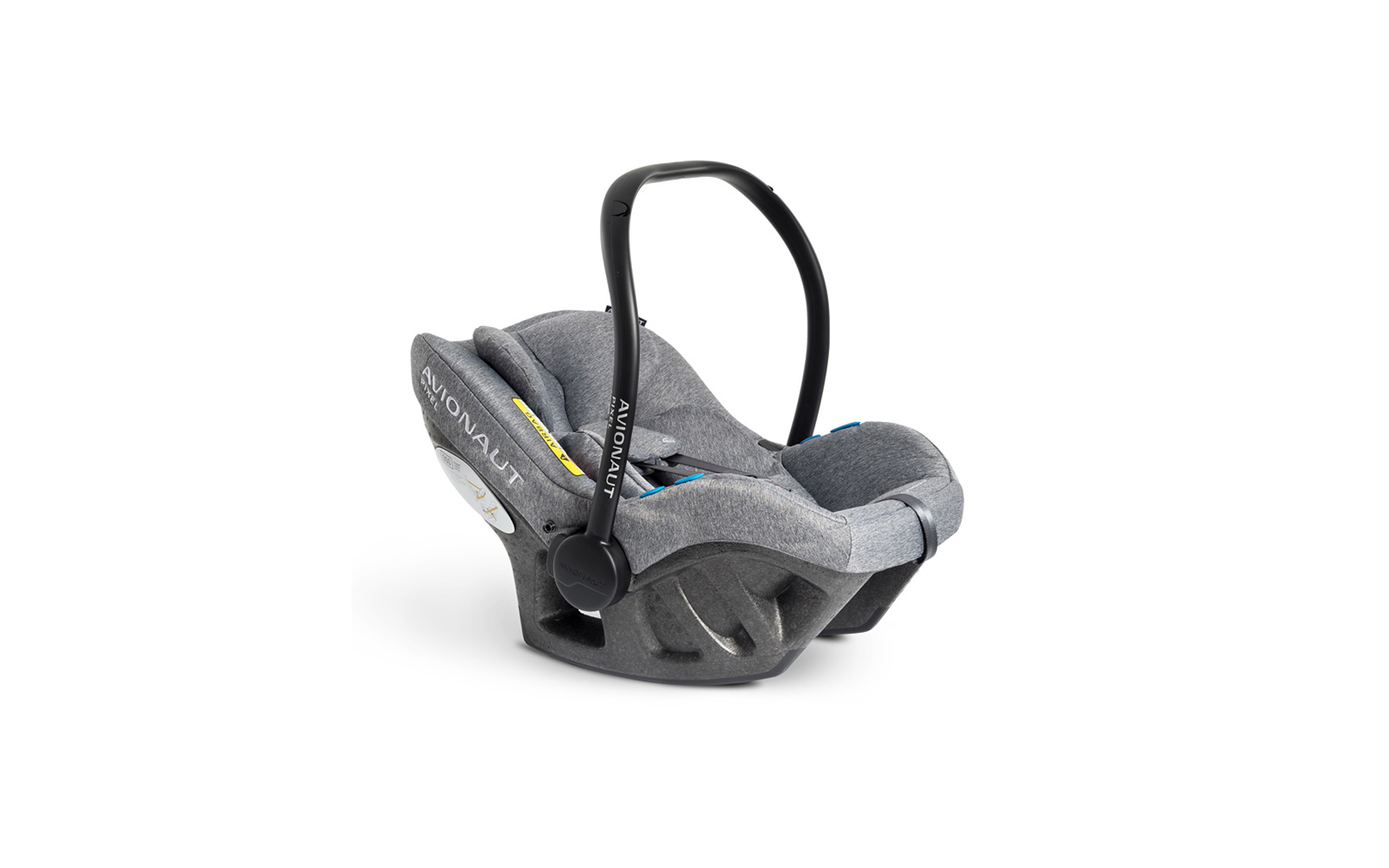
Photo: Avionaut
The Avionaut Pixel has undergone rigorous "Avio Test" tests to check what happens to the child's body during a front, rear and lateral impact, achieving top marks. At the time of a frontal and rear impact, Avionaut Pixel achieved a result of 140% for back protection and 153% for head protection, exceeding i-Size requirements by as much as 40% and 53%. In the lateral impact head protection test the result was 120%, 20% better than the i-Size standards.
The safety of the structure and the materials used to construct it was additionally confirmed by prestigious and internationally recognized tests carried out, among others, by the German automobile club ADAC (Allgemeiner Deutsher Automobil-Club), the Dutch organisation TASS/TNO (Netherlands Organisation for Applied Scientific Research), the Italian CSI (Certification and Analysis Centre) and the Polish institute PIMOT (Industrial Automotive Institute).
— Work on the Avionaut Pixel child safety seat has taken about two years from the moment we started cooperating with Knauf Industries, creating a prototype through its successive evolutions and tests. Today, we can safely say that we are proud of this product and the selection of all construction components. In retrospect and looking at the results we have achieved, we can confidently say that it was worth dedicating so much effort to this project. We have succeeded in creating the lightest, most comfortable child safety seat in the world, which in terms of parameters exceeds the current safety standards. Avionaut Pixel is already conquering foreign markets, noting a steady increase in sales – says Artur Kowalski, Leading Engineer at Karwala.
Innovative child safety seat construction
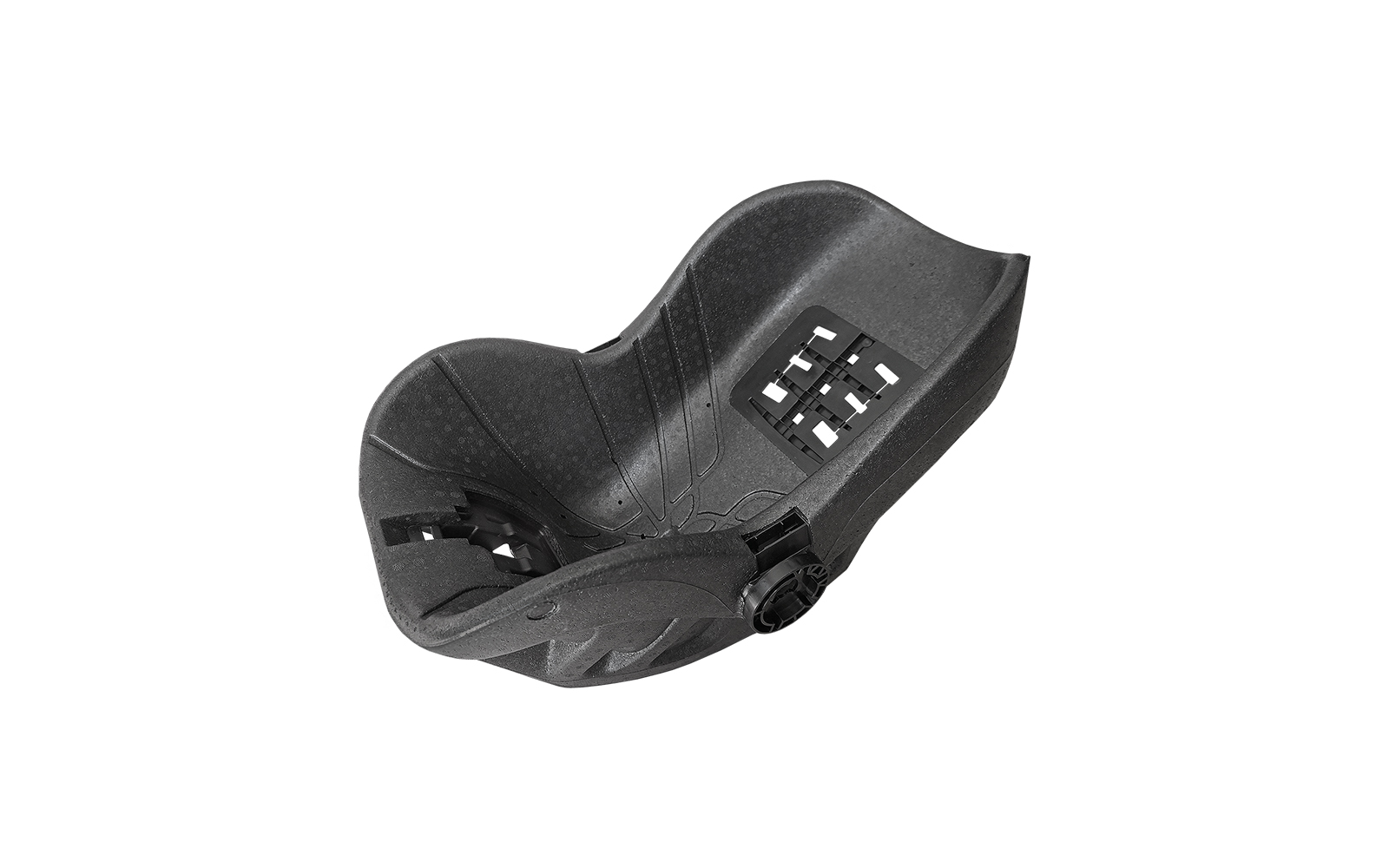
Photo: Knauf Industries
The target for Karwale's specialists was extremely ambitious. The original solution assumed making the whole base of the child safety seat from expanded polypropylene (EPP). Thanks to the cooperation with Knauf Industries, it has been possible to develop a mould and direct granule moulding technology that allows for obtaining a compact structure with uniformly high density. This was especially important to ensure compliance with current strength and resistance standards to all forces affecting the child safety seat during a collision. The second but no less important challenge was to precisely match the EPP base with other construction components made of other materials.
The crucial issue was to connect the "crust" with the plastic insert sunk into it. The design assumption was that these two elements were to interact optimally with each other in order to achieve the assumed strength parameters. The construction process also required to include the range of material deformation and the interaction between the base and the insert resulting from calculations and test results. Thanks to the close cooperation of specialists from Knauf Industries and Karwala, it was possible to achieve high precision in the bonding of the base and the insert, which resulted in excellent results in many demanding tests.
— Participation in this project was a challenge for us because we entered into a new market segment. We approached it with great attention and particular commitment, which is required for the safety of children. During our cooperation with Karwala , we tried to respond to any qualitative indications from our partner. Today we are sure that we have successfully met these requirements and created a product with the highest global parameters. Together with the Avionaut brand we have created a solution that has revolutionised the industry. I am convinced that it is only a matter of time when the solutions from Knauf Industries EPP will find application in another new and innovative construction solution — says Marcin Zawadzki, Key Account Manager at Knauf Industries.