The battery is the “heart of an electric car” and is also its heaviest and most expensive component. Its lifespan and reliability depend not only on the design or type of cells themselves, but also on the type of housing. It can be made of various materials – not just metal anymore, but also innovative ultralight plastics.
How is a battery in an electric car built?
Batteries in electric cars consist of cells, which are connected in series and in parallel. This creates modules, which in turn form a battery pack. Each cell contains electrodes (anode and cathode), electrolyte and separator. The electrodes are made of active materials that, when exposed to a current, trigger a chemical reaction that produces electricity. The electrodes are immersed in an electrolyte that allows current to flow between them. The individual cells are separated by a separator – a type of membrane that prevents the cathode and anode from short-circuiting. The entire battery must be protected by a suitably sturdy housing, which absorbs shocks and protects the cells from extreme temperatures and electrical breakdowns.
What is a battery in a car made of? Components and materials
Which materials are used in the production process of batteries for electric cars, whether BEV, HEV or PHEV, depends on the type of cells. All of them have their advantages and disadvantages as regards their capacity, durability, production cost or safety of use. The most popular are lithium-ion (Li-ion), lithium-polymer (LiPo), nickel-metal hydride (NiMH) and nickel-cadmium (NiCd) batteries. The most valuable raw materials included in the various types of batteries for electric cars are the active materials used in the electrodes, such as lithium, cobalt, nickel, manganese, or graphite. Organic solutions of metal salts in the form of liquids or gels are used as electrolytes. The exception are solid-state batteries with a solid electrolyte, which are still under development. Meanwhile, polymeric materials and ceramic coatings are used for separators.
How many cells are there in a car battery?
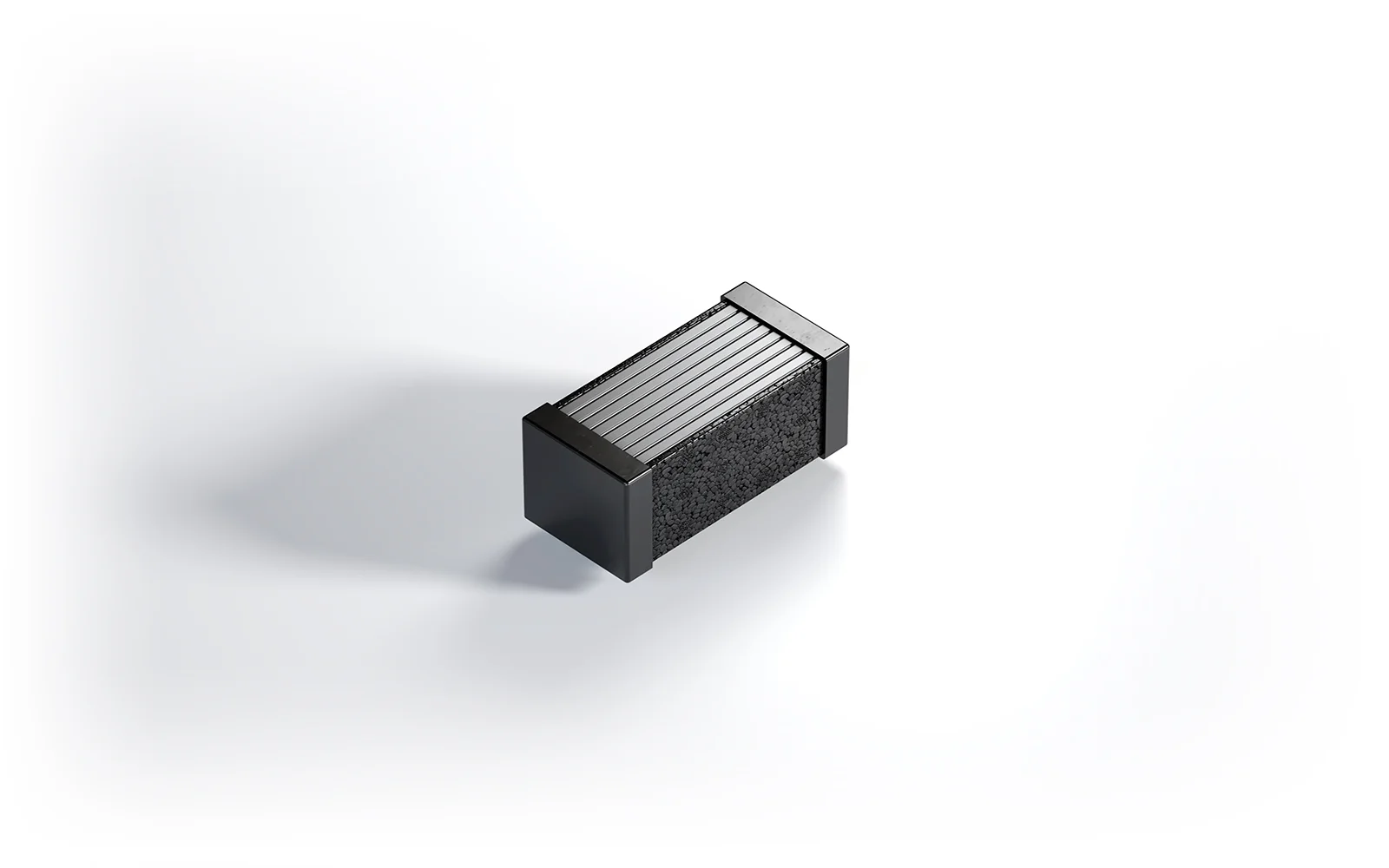
There is no set optimal number of cells used in an electric car battery. It depends on its capacity and voltage in each case. The higher the designed capacity and voltage of the battery, the more cells are needed. For example, a lithium-ion battery with a capacity of 60 kWh and a voltage of 400 V can consist of about 8,000 cells. Therefore, a smaller number of cells will be found in a small city car and a larger number in a long-range hybrid.
Car battery case – how does it affect an electric car?
A car battery case performs several important functions. First, it protects the battery from mechanical, thermal and chemical damage. Second, it can provide it with ventilation, thus helping to optimize heat distribution. Third, it provides “structure” for the modules and ensures that they stay in place. All of this means that a car battery housing must be manufactured from robust materials. Metals are often used for this purpose, which affects the weight of the battery and therefore also the dead weight, range and handling characteristics of the car. A low center of gravity, on the one hand, increases the car's grip and traction, and on the other, reduces its maneuverability. Therefore, manufacturers are looking for new material solutions to produce lighter batteries.
Manufacturing a housing for a car battery and materials used
The materials used to manufacture a car battery housing must meet high requirements in terms of impact strength, thermal insulation or resistance to fire and electrical breakdowns. Most commonly used materials include not only steel, aluminum, hard plastics or various types of composites, but also modern foams such as EPP. Foamed polypropylene, which has long been used as a material for transportation packaging, has also proven to be an excellent solution for making very lightweight insulation systems for car batteries and shock protection solutions. Here, it is an excellent replacement for much heavier plastics, and as an easily recyclable material, it facilitates the recycling of car batteries, which is in line with environmental regulations.
EPP components that protect car batteries and increase their lifespan
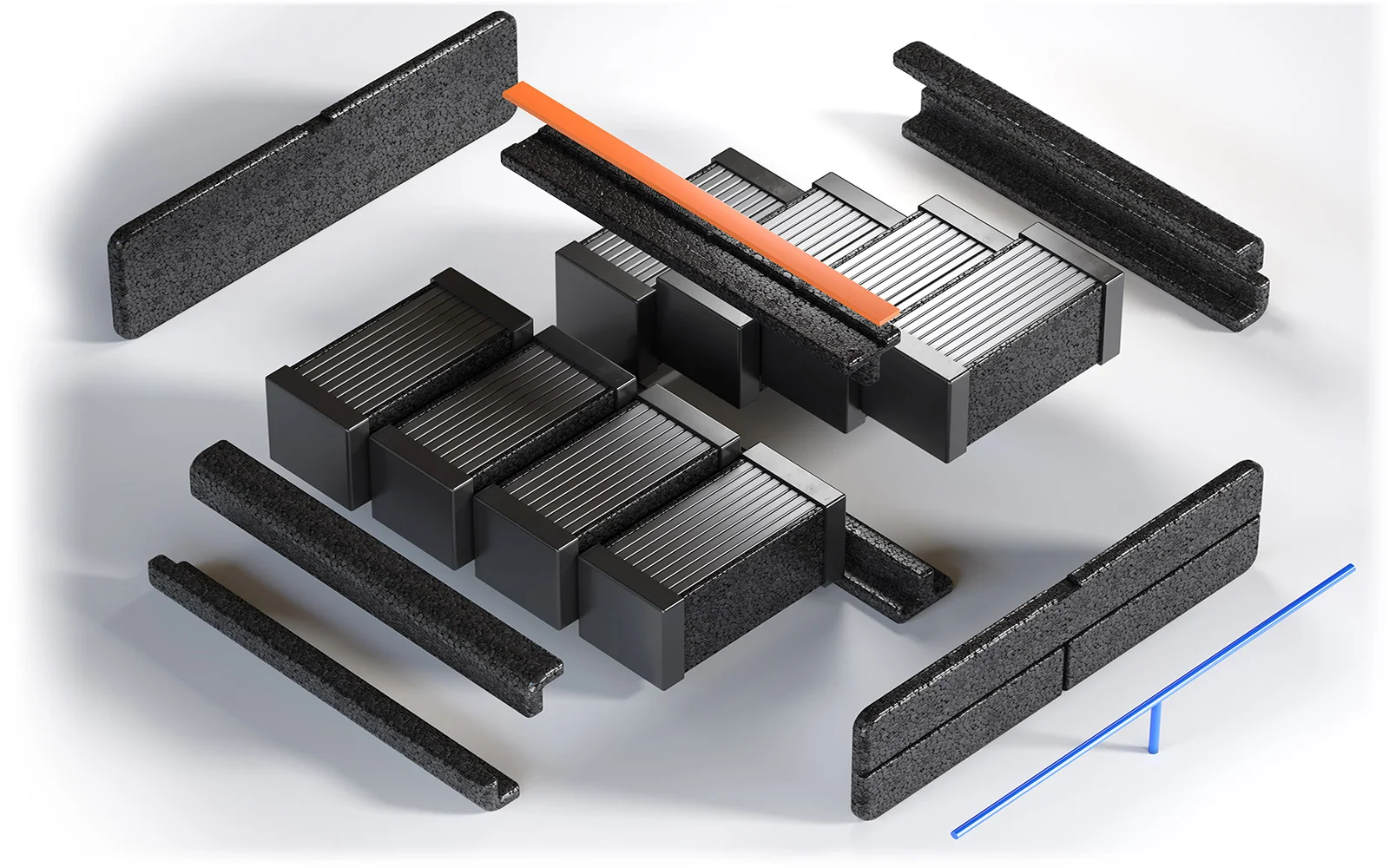
“EPP foam is characterized by high impact resistance, excellent thermal and acoustic insulation, and can be easily formed into any shape. As a result, it is successfully used to manufacture a variety of automotive battery components, from insulators to separators, and fasteners. The excellent damping properties of foamed polypropylene mean that such a housing protects sensitive cells from shocks and vibrations, extending the life of batteries in electric cars and increasing the range of such vehicles. The EPP separators also prevent electrical breakdowns and the transfer of high temperatures between cells, benefiting battery operating temperatures and safety. On the other hand, the mounting elements simplify the routing of electrical cables and make it easier to remove the battery after use.” says Nicolas Moreau (Automotive Project Manager at Knauf Industries).
How does a battery in an electric car work?
The battery in an electric car works by converting chemical energy into electrical energy and vice versa. When the battery is charging, electric current from the grid or charging station flows into the battery, causing ions to migrate through the electrolyte from the anode to the cathode. On the other hand, during battery discharge, when electric current flows from the battery to the electric motor, the whole process is reversed.
Which electric car battery design is the best choice and why?
So far, no single optimal battery design has been developed to fit every car. Electric vehicle manufacturers use very different technologies. Two basic types of cell design may be distinguished, though: cylindrical and prismatic. In the case of cylindrical construction, the cells have adopted a cylindrical shape. The advantages of such a design include high energy density, good thermal and mechanical resistance of the cells, but there are large space losses, and cooling is difficult. In a prismatic design, on the other hand, the cells are cuboid in shape, which makes better use of the available space, facilitates cooling, and provides more freedom in shaping the modules. However, the energy density is lower in this case, and there is an increase in battery weight and manufacturing costs. Whatever the shape of the cells and the design of the modules, plastic injection molding technology makes it possible to produce perfectly matched mounting, insulation or EPP housing components that fully meet the expectations of designers and developers.