The number of electric cars in the world is growing rapidly – up to 145 million such vehicles are projected to be on the road by 2030 and demand for lithium-ion batteries is expected to increase up to 14 times. This raises the question of how to handle them at the end of their life so that they do not pose a threat to the environment. What does the disposal of car batteries entail in practice?
Environmental impact of EV batteries
The chemicals used to make electric car batteries are toxic, so when released into the environment they can have negative effects on living organisms, including humans. For example, cadmium causes kidney damage and anemia, cobalt disrupts thyroid function, while lithium is deposited in the lungs, leading to swelling. It is the dangers of irresponsible disposal of car batteries that are the most common arguments raised by opponents of e-mobility. The depletion of rare earth resources needed for battery production, as well as the CO2 emissions produced during their multi-stage processing, are also questionable. Some of these problems may be solved by properly recycling lithium-ion batteries. It involves reusing them as energy storage, for example, as well as recovering materials and valuable raw materials at the end of their life. This eliminates any waste or risk of potentially hazardous substances entering the environment. The degree of difficulty, and thus the profitability of recovery, depends on the type of battery.
What kind of car battery design is most favorable?
Lithium-ion batteries consist of four main components: cathode, anode, electrolyte and separator. They also include a solid aluminum protective container and module housing, as well as plastic covers for the cells, wires or connectors. Depending on the cathode material, there are several types of lithium-ion batteries. Currently, three types of batteries are used worldwide for electric cars: lithium-nickel-manganese-cobalt (NMC), lithium-nickel-cobalt-aluminum (NCA) and lithium-iron-phosphate (LFP) batteries. The first two power passenger cars, while the third is used mainly in electric buses. Their main advantages include high energy density, safe use and long service life. From the point of view of raw material recovery, NMC and NCA batteries are the most favorable, as they can be successfully hydrometallurgically and partially recycled. In contrast, the financial and environmental costs of recycling LFP lithium-ion batteries are higher than producing new batteries.
Disposal and recycling of car batteries – what does it involve?
What happens to used electric car batteries? Counterintuitively, they can gain a second life as energy storage in other manufacturing processes or become a source of power for less demanding devices, such as a scooter or electric bicycle. Some companies collect used batteries, which can serve for about 10 more years as energy storage before they need to be recycled.
What is the process of battery disposal?
As batteries vary in construction, disassembly is done manually by skilled people in protective clothing, as potential mistakes in disassembling the cells could result in ignition or explosion. The most expensive and labor-intensive step in battery recycling is the extraction of valuable materials such as lithium, cobalt, nickel and manganese.
There are typically three battery recycling processes: pyrometallurgical, hydrometallurgical and partial. In the first case, valuable metals are recovered by thermal treatment, in the second by chemical reactions, while the third involves partial recovery of materials and regeneration of the rest of the cathode. Battery recycling in Europe is carried out on a small scale by pilot and specialized recycling plants. For the time being, their capacity is sufficient in relation to demand, but the system will certainly need to be expanded. Greenpeace forecasts that 12.85 million tons of electric car batteries will be taken out of service by 2030.
How long does a battery take to decay depending on its type?
Batteries are often referred to as the most dangerous product of civilization. Regardless of the type, they are harmful to the environment due to their complex structure and the content of various chemicals. What is the decomposition time of individual battery components? It is estimated that the metal casing and other components made of metal decompose after 100 years, while the chemical substances decompose after hundreds of thousands of years or even never. Therefore, they are the cause of permanent pollution of soil and water.
How quickly do batteries degenerate before they go to a battery recycling facility?
As a general rule, electric car battery manufacturers provide an 8-year warranty on batteries. It is generally accepted that a battery is unusable when its efficiency drops below 70-80%, which, according to drivers' experience, can happen even after 12 years, which corresponds to driving about 580,000 kilometers. The lifespan of electric car batteries depends mainly on the number of charge and discharge cycles. In this aspect, LFP batteries are a firm favorite, as they are designed for more than 2,000 cycles, or approximately 10 years of use. However, due to their high power output, they are mainly used in heavy-duty applications.
In second place are NMC batteries with 1000-2000 cycles. Their main advantage is also high energy density, which means they can store a lot of energy relative to their weight, in this case – 150-220 Wh/kg. The third frequently used battery type in electric cars are the NCA batteries with 500 cycles and a density of 200-260 Wh/kg. The list closes with LMO (lithium-manganese) batteries with 300-700 cycles. These, however, have a low capacity compared to other battery types. New and better technologies are also being currently developed, such as the solid-state battery with a solid electrolyte, but for the time being they are not suitable for use in cars yet.
How much raw material can be recovered from batteries?
The amount of raw material recovered in the process of recycling batteries depends on their design and available technologies. Scientists are still working on such methods for recycling lithium-ion batteries that will yield the best possible results. For example, at a battery recycling plant created as part of a consortium of Renault, Veolia and Solvey, active materials from batteries are immersed in N-methylpyridinium, and – after draining and drying – crushed using ultrasound waves and leached with acid. In such a process, as much as 96% of cobalt and 98% of lithium can be recovered. Quantities of recovered raw materials from batteries will soon be strictly regulated within the European Union. At the end of 2022, regulations were introduced stating that nickel and cobalt are to be recycled in 90% from 2027, and as much as 95% as of 2030. For lithium, on the other hand, the values were set at 50 and 80% respectively. However, the high labor and carbon intensity of recycling lithium-ion batteries, as well as the cost of disposing of the batteries, remains an issue.
Manufacturer of sustainable components for car batteries
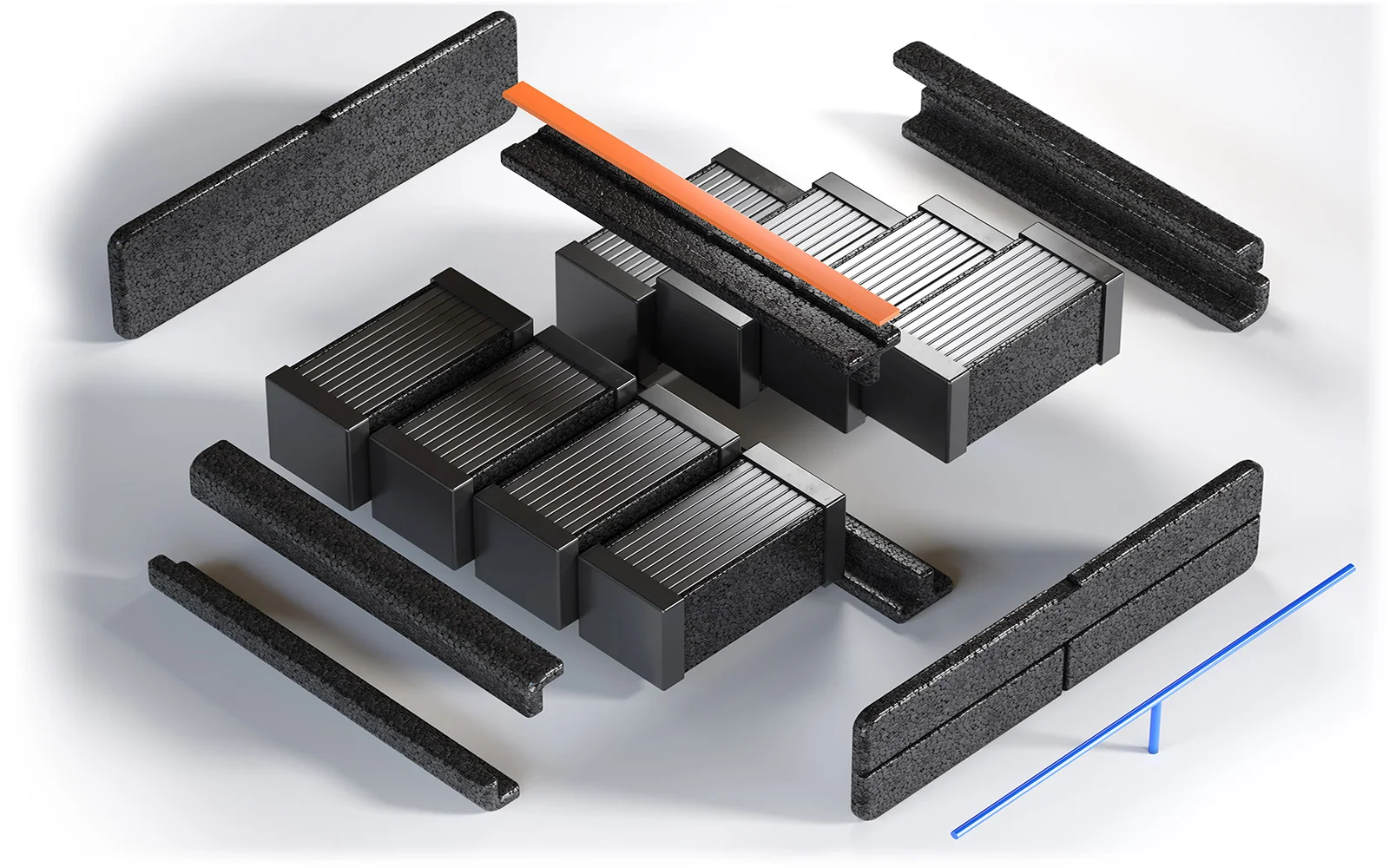
It is assumed that recycling of car batteries can reduce their carbon footprint by about 17%. If you look at the battery's components, the aluminum housing and the container responsible for protecting the modules weigh the most. That's as much as 126 kg in a battery weighing 400 kg! Not counting the cathode, anode and copper, the next heaviest component of the battery are the plastic components performing protective and mounting functions, weighing about 22 kg. Some of these components can be successfully manufactured from innovative, ultralight EPP plastic, which is about 95% air-filled and 100% recyclable.
At our facilities, we design and manufacture ultralight foam components for automotive batteries from EPP, which combine high mechanical strength with excellent insulation or anti-static properties. Molded housings, covers and mounting components for cells made of EPP not only provide them with excellent protection against shocks and varying temperatures, but also provide excellent insulation against electrical punctures. Specially developed connecting and fastening components make it easy to install and later also remove the cells. Moreover, EPP processing is easier and less energy-intensive than, for example, aluminum, and thus produces fewer CO2 emissions. As a result, it is possible to significantly reduce the carbon footprint of car batteries. A closed-loop economy in the automotive industry is one of the elements of our CSR activities.