Dzięki długoletniemu doświadczeniu i zaawansowanym metodom przetwórstwa oferujemy profesjonalne i kompleksowe rozwiązania dla branży automotive bazujące na lekkich, wytrzymałych i w pełni nadających się do recyklingu tworzywach sztucznych, takich jak polipropylen spieniony (EPP), polistyren spieniony (EPS) czy innowacyjny RELOOPP®. Inteligentne projektowanie, najnowocześniejsze technologie przetwórstwa z zastosowaniem surowców wtórnych i odnawialnych, pozwala na optymalizację produkcji, zmniejszenie emisji CO2 i poprawę efektywności energetycznej pojazdów. Odkryj materiały, które kształtują przyszłość zrównoważonej motoryzacji!
Nowoczesne tworzywa sztuczne w motoryzacji
Branża motoryzacyjna wiele zawdzięcza tworzywom sztucznym. Dzięki swoim wyjątkowym właściwościom, takim jak niewielki ciężar, wytrzymałość i zdolność do tłumienia energii elementy samochodowe z EPP i EPS stały się jednym z kluczowych elementów pasywnych systemów bezpieczeństwa. Szczególną rolę we współczesnym, zrównoważonym przemyśle automotive odgrywają innowacyjne spienione tworzywa, jak EPP (spieniony polipropylen) czy EPS (spieniony polistyren), które dodatkowo zapewniają doskonalą izolacyjność cieplną i akustyczną. Logiczną kontynuacją rozwoju tych materiałów są ich jeszcze bardziej zrównoważone wersje, które ograniczają ślad węglowy produkcji: RELOOPP® i NEOPS®.
Polipropylen spieniony (EPP)
Wypełniona w niemal 95% powietrzem spieniona struktura tworzywa EPP sprawia, że jest ono niezwykle lekkie, a jednocześnie wytrzymałe i odporne na wielokrotne uderzenia. Jego cechą wyróżniającą jest tzw. zdolność do elastycznego powrotu. Dzięki niej wyprodukowane z niego części nie rozpadają się na kawałki pod wpływem obciążenia, ani nie ulegają trwałej deformacji, lecz wracają do poprzedniego kształtu. Ze względu na tę charakterystyczną właściwość EPP zrewolucjonizowało produkcję automotive m.in. w obszarze elementów pasywnego bezpieczeństwa.
Doskonałe właściwości tego materiału związane z absorpcją energii sprawiły, że jest on bardzo często stosowany w elementach konstrukcyjnych, fotelach czy osłonach akumulatorów. Fotele samochodowe z EPP są nie tylko niezwykle bezpieczne, lecz także komfortowe w użytkowaniu. Niezwykła łatwość formowania tego materiału sprawia, że piankowe części mogą osiągać dowolne kształty, co sprzyja rozwojowi projektów zapewniających większą ergonomię i estetykę wnętrz pojazdów. Kolejną niezwykle ważną zaletą EPP z punktu widzenia współczesnych wymogów związanych z ochroną środowiska i zasobów naturalnych jest możliwość jego recyklingu w 100%.
Sprawdź wszystkie możliwości, jakie zapewnia EPP i zobacz nasze rozwiązania!
Neopolen® – nowa jakość EPP
Neopolen®, czyli najwyższej jakości spienione tworzywo EPP składa się w głównej mierze z zamkniętych komórek powietrza, dzięki czemu zapewnia doskonałą absorpcję energii, minimalny ciężar oraz wysoką stabilność termiczną. Tym samym sprawdza się niezawodnie w wielu trudnych zastosowaniach, również wymagających odporności na wysokie zakresy temperatur. Jego wysoka wytrzymałość na obciążenia statyczne i dynamiczne, a także odporność na działanie chemikaliów i oleju sprawiają, że Neopolen® może być z powodzeniem stosowany np. w pobliżu silnika. Surowiec występujący w szerokim zakresie gęstości od 20 do 100 g/l, bogatej palecie kolorów i w wersjach specjalnych np. o ograniczonej przewodności elektrycznej czy cieplnej pozwala na dobór idealnego rozwiązania do bardzo zróżnicowanych aplikacji.
Wybierz nowoczesne rozwiązania – dowiedz się więcej o NEOPOLEN®
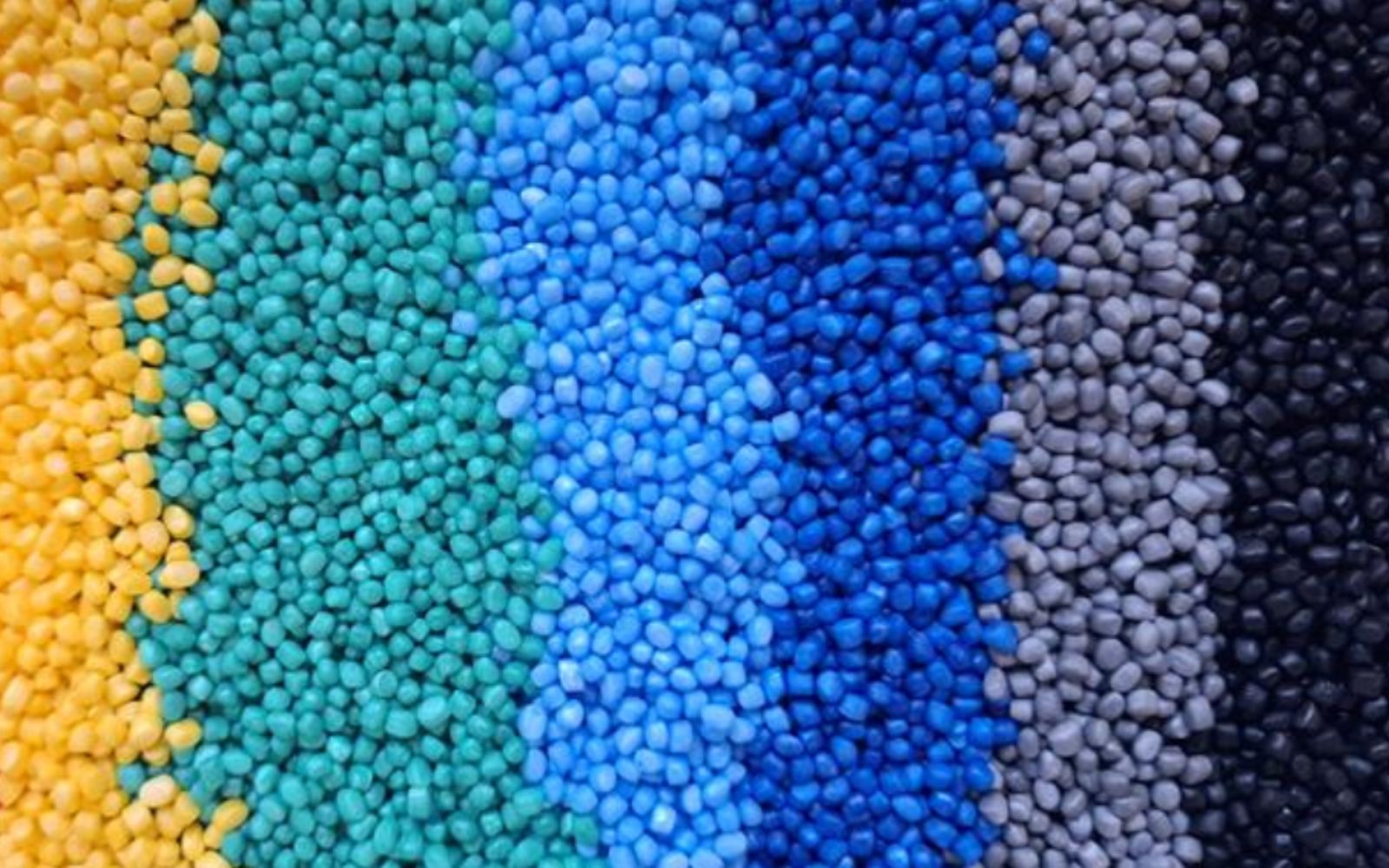
RELOOPP® – EPP z recyklingu
RELOOPP® został opracowany przez Knauf Industries w odpowiedzi na potrzebę stosowania bardziej zrównoważonych tworzyw sztucznych i stanowi idealną alternatywę dla tradycyjnego spienionego polipropylenu (EPP). Powstaje on nawet w 90% z pokonsumenckich odpadów EPP, które są następnie poddawane recyklingowi mechanicznemu i przetwarzane w pełnowartościowy materiał. Tym samym RELOOPP® wpisuje się w ideę gospodarki o obiegu zamkniętym, zmniejsza ilość odpadów i ogranicza zużycie surowców pierwotnych. Jednocześnie zachowuje wszystkie właściwości materiału produkowanego z surowców pierwotnych, dzięki czemu doskonale sprawdza się jako materiał do wytwarzania ultralekkich elementów pasywnych systemów bezpieczeństwa, części siedzeń samochodowych czy opakowań.
Wprowadzenie RELOOPP® to idealny wkład Knauf Industries w rozwój zrównoważonych rozwiązań materiałowych.
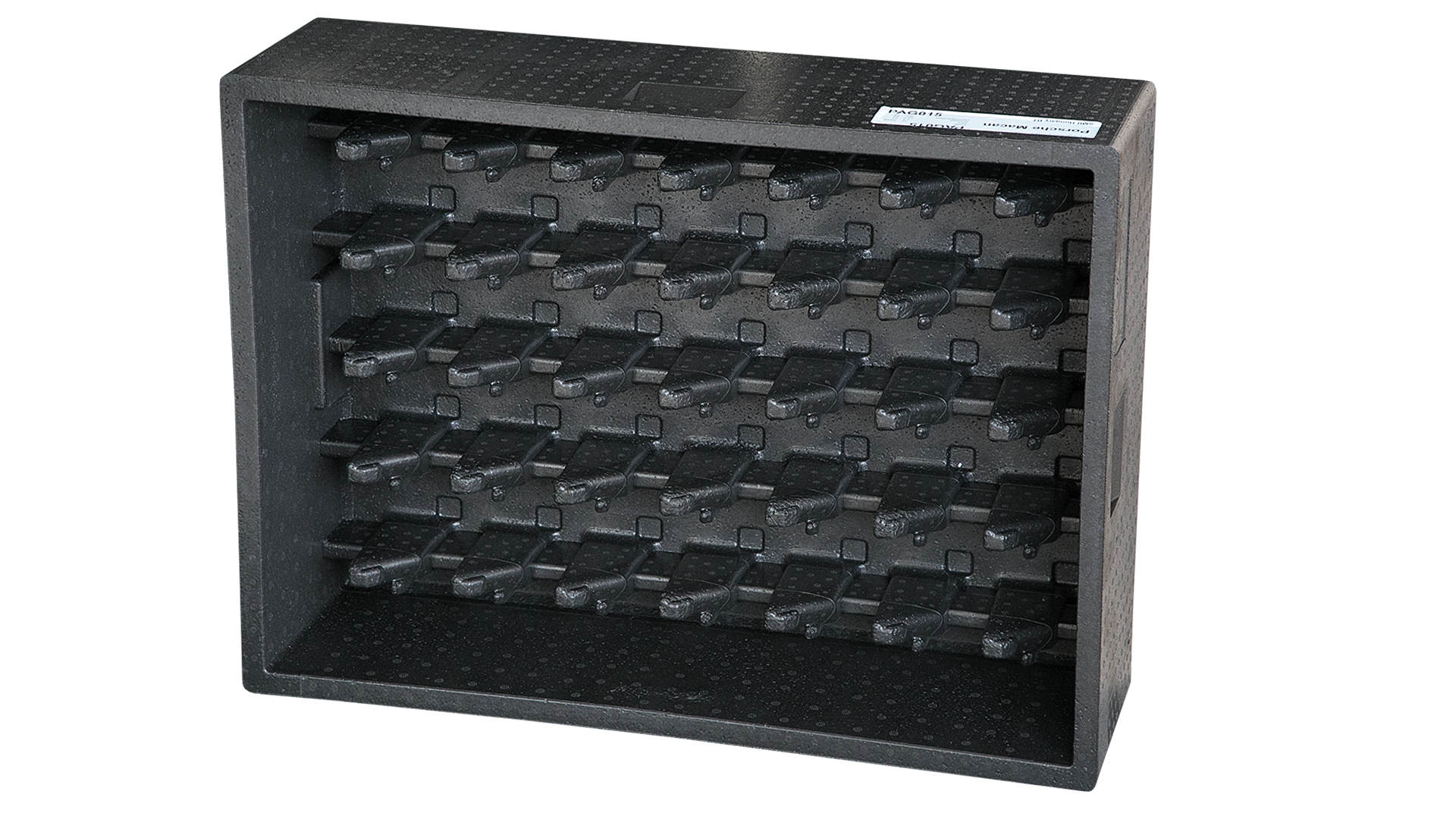
Polistyren spieniony (EPS)
EPS to wyjątkowo lekki materiał, który zawiera aż 98% powietrza, dzięki czemu sprawdza się idealnie zwłaszcza wszędzie tam, gdzie wymagane jest przede wszystkim ograniczenie masy własnej samochodu. Komponenty z EPS cechują się doskonałymi właściwościami izolacyjnymi – zarówno termicznymi, jak i akustycznymi oraz tłumiącymi, dzięki czemu sprawdzają się głównie w obszarach amortyzacji i ochrony komponentów. EPS znajduje szerokie zastosowanie w produkcji opakowań transportowych na części motoryzacyjne, ale także w konstrukcjach samochodów. W zależności od gęstości może sprawdzić się również jako wypełnienie podłogi, bagażnika czy drzwi samochodowych.
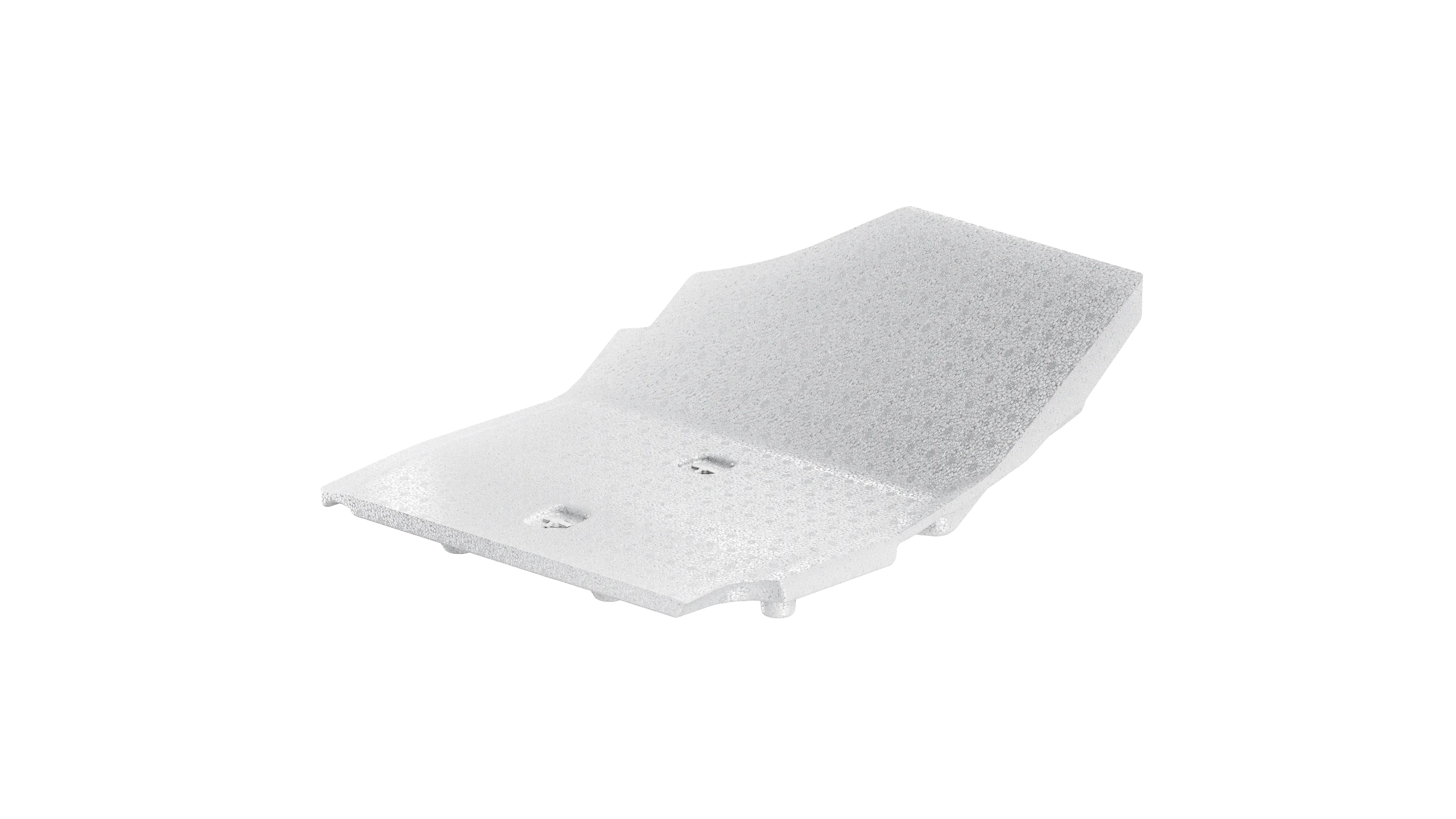
NEOPS® – nowa generacja EPS
NEOPS® to opracowany przez Knauf Industries innowacyjny piankowy materiał, który stanowi doskonałą alternatywę dla tradycyjnego polistyrenu spienionego (EPS). Tworzywo wytwarzane w oparciu o bilans biomasy (Biomass Balance) z surowców odnawialnych, charakteryzuje się zmniejszonym śladem węglowym nawet o 30%, dzięki ochronie zasobów kopalnych.
Materiał NEOPS® zachowuje przy tym wszystkie zalety tradycyjnego EPS, jak minimalny ciężar i wysoka odporność mechaniczna, neutralność chemiczna oraz łatwość formowania. Ze względu na te cechy znajduje on idealne zastosowanie przy produkcji izolacji, opakowań przemysłowych i na żywność, ale także części technicznych. Podobnie jak EPS w pełni podlega recyklingowi, co czyni go materiałem w pełni zgodnym z zasadami gospodarki obiegu zamkniętego.
Wybierz nowoczesne rozwiązania – dowiedz się więcej o NEOPS®
CELOOPS®
CELOOPS® to innowacyjny materiał opracowany przez Knauf Industries, wykonany w całości z odpadów plastikowych pochodzących z recyklingu. CELOOPS® oferuje takie same właściwości techniczne jak tradycyjny EPS, w tym lekkość, trwałość, amortyzację wstrząsów oraz odporność na wilgoć i rozwój mikroorganizmów. Nadaje się do stosowania w opakowaniach na żywności, zastosowaniach przemysłowych i komponentach technicznych. Ponadto CELOOPS® nadaje się do recyklingu za pośrednictwem istniejących kanałów recyklingu EPS i programu odzysku Knauf Circular®, wspierając przejście na bardziej zrównoważoną gospodarkę tworzywami sztucznymi.
Kluczowe zalety naszych materiałów
Nasze nowoczesne spienione tworzywa sztuczne nie tylko spełniają najbardziej rygorystyczne wymagania techniczne stawiane np. w obszarach bezpieczeństwa czy transportu żywności, lecz także promują zrównoważony rozwój.
Lekkie materiały składające się głównie z powietrza są wyjątkowo efektywnym rozwiązaniem w projektach motoryzacyjnych, gdyż obniżają masę własną pojazdów i dzięki temu ograniczają ich zapotrzebowanie na paliwo czy energię elektryczną. Jednocześnie ze względu na właściwości tłumiące i termoizolacyjne wewnętrzne części samochodowe z EPP i EPS skutecznie chronią pasażerów przed następstwami wypadków oraz poprawiają wygodę podróżowania, zapewniając komfort cieplny i redukując hałas. Natomiast zewnętrzne części samochodowe z EPP przyczyniają się do ochrony bezpieczeństwa pieszych. Stanowią ponadto doskonałą odpowiedź na potrzeby producentów OEM związane ze zrównoważonym rozwojem i wymogami GOZ, gdyż w 100% podlegają recyklingowi. Natomiast dzięki wysokiej formowalności są niezwykle efektywne kosztowo. Elastyczne procesy produkcyjne pozwalają na masowe wytwarzanie części o dowolnych kształtach, co wspiera tworzenie niestandardowych i innowacyjnych rozwiązań.
Nasze podejście do innowacji i recyklingu
Historia motoryzacji to historia ciągłego postępu, dlatego w ramach naszego Centrum Innowacji ID Lab koncentrujemy się na projektowaniu i produkcji elementów z tworzyw sztucznych w nowych technologiach. Dzięki ścisłej współpracy z ekspertami oraz nowoczesnemu podejściu do recyklingu mechanicznego i chemicznego jesteśmy w stanie tworzyć innowacyjne rozwiązania, które odpowiadają na potrzeby różnych branż, jak m.in. sektora motoryzacji czy produkcji opakowań transportowych. W odpowiedzi na konieczność zmniejszania emisyjności przemysłu, pracujemy nad zrównoważonymi tworzywami spienionymi, które oszczędzają pierwotne zasoby, są wytwarzane z zastosowaniem zasobów odnawialnych czy produkowanymi w oparciu o bilans biomasy.
W pracy nad nowymi rozwiązaniami wykorzystujemy zaawansowane narzędzia, takie jak druk 3D, skanery 3D i symulacje numeryczne, co ułatwia testowanie nowych produktów i pozwala uzyskać jeszcze lepsze rezultaty. Dzięki temu jesteśmy w stanie jeszcze efektywniej wspierać naszych partnerów we wdrażaniu ekologicznych materiałów i znacznie skrócić proces wprowadzania produktów na rynek, poprawiając jednocześnie ich jakość.
Przykłady zastosowań innowacyjnych tworzyw spienionych
Nowoczesne technologie produkcyjne pozwalają na precyzyjne kontrolowanie parametrów naszych produktów zgodnie z oczekiwaniami klienta czy konkretną aplikacją. W zależności od parametrów związanych z gęstością, twardością czy odpornością na ściskanie i uderzenia znajdują one zastosowanie w produkcji zderzaków, siedzeń, elementów wewnętrznych pojazdów, wyjątkowo lekkich osłon przeciwsłonecznych czy opakowań ochronnych do transportu delikatnych części samochodowych.
W porównaniu z twardymi tworzywami sztucznymi wyróżniają się doskonałymi właściwościami izolacyjnymi, zarówno termicznymi, jak i akustycznymi, a także odpornością na uderzenia, co umożliwia ich stosowanie w częściach samochodu wymagających podwyższonej amortyzacji. Niektóre z nich mogą również sprawdzić się w ekstremalnych zastosowaniach. Np. EPP może uzyskać podwyższoną odporność na wysokie temperatury czy przebicia elektryczne, dzięki czemu może być używany w obudowach baterii do samochodów elektrycznych czy osłonach zbiorników na wodór.
Tworzywa sztuczne wykorzystywane w technologii wtrysku
W technologii wtrysku tworzyw sztucznych wykorzystywanych do produkcji komponentów dla branży automotive, kluczową rolę odgrywają materiały o wysokiej trwałości, odporności na temperaturę i elastyczności projektowej. Knauf Industries stosuje szeroką gamę zaawansowanych tworzyw, takich jak PP (polipropylen) i PP/EPDM, które zapewniają dobrą odporność chemiczną i elastyczność — idealne do zastosowań w elementach zewnętrznych i wnętrzach pojazdów. ABS oraz PC/ABS łączą wytrzymałość mechaniczną z estetyką wykończenia, dzięki czemu doskonale sprawdzają się w elementach kokpitów i obudowach. PA6 GF30 (poliamid z włóknem szklanym) i PP GF30 to materiały wzmacniane, wykorzystywane tam, gdzie wymagana jest wyjątkowa sztywność, np. w strukturach siedzeń, mocowaniach czy elementach konstrukcyjnych. W zależności od wymagań klienta możemy również zastosować tworzywa takie jak PC, PC/PMMA oraz PS, który znajduje zastosowanie w produkcji prostszych komponentów o mniejszych wymaganiach mechanicznych. Dobór odpowiedniego tworzywa zależy od funkcji komponentu, jego lokalizacji w pojeździe oraz wymogów jakościowych i środowiskowych.
Tworzywa sztuczne w motoryzacji – FAQ
Jakie są główne korzyści stosowania spienionych tworzyw sztucznych w motoryzacji?
Spienione tworzywa sztuczne oferują wiele korzyści w zastosowaniach motoryzacyjnych. Przyczyniają się do poprawy efektywności energetycznej, bezpieczeństwa i zrównoważonego rozwoju. Są znacznie lżejsze niż tradycyjne materiały, takie jak metal, filc, guma czy twarde tworzywa sztuczne. Pozwala to zmniejszyć masę pojazdu, co przekłada się na niższe zużycie paliwa i mniejsze emisje CO2. Jednocześnie materiały te doskonale izolują termicznie wnętrze pojazdu i ograniczają hałas, podnosząc komfort podróżowania.
Ze względu na łatwość formowania spienione tworzywa sztuczne umożliwiają one projektowanie skomplikowanych kształtów i elementów, takich jak zderzaki, deski rozdzielcze czy różnego rodzaju obudowy. Nie tylko poprawiają funkcjonalność i estetykę, lecz także zapewniają swobodę projektowania. Stosowanie spienionych materiałów w branży motoryzacyjnej przyczynia się ponadto do jej zrównoważonego rozwoju. Wiele z nich, jak np. RELOOPP®, może być wytwarzanych z surowców z recyklingu, co jest zgodne z wymogami gospodarki o obiegu zamkniętym. Warto również dodać, że w przeciwieństwie np. do metalu spienione tworzywa sztuczne nie ulegają korozji. Tym samym przedłużają żywotność samochodów.
Czym różni się EPP od EPS i które tworzywo lepiej sprawdzi się w zastosowaniach motoryzacyjnych?
EPP (spieniony polipropylen) i EPS (spieniony polistyren) różnią się od siebie pod wieloma względami. EPP jest odporny na trwałe odkształcenie i wraca do poprzedniego kształtu po ustaniu nacisku, dzięki czemu jest idealny do produkcji elementów amortyzacyjnych, jak np. amortyzatory zderzaków czy wypełnienia zagłówków. EPP ma również większą odporność na wysokie temperatury, dzięki czemu może być stosowany w pobliżu silnika lub innych źródeł ciepła. EPS jest z kolei bardziej podatny na trwałe odkształcenia i może ulegać kruszeniu, dlatego znajduje zastosowanie w obszarach, gdzie wymagana jest mniejsza wytrzymałość na obciążenia, uderzenia i temperaturę. Jeśli natomiast chodzi o zrównoważony rozwój, zarówno EPP, jak i EPS mogą być poddawane recyklingowi, jednak w przypadku EPS proces ten jest nieco bardziej skomplikowany. Pomimo słabszych właściwości mechanicznych EPS jest jednak tańszy w przetwarzaniu i bardziej efektywny kosztowo, co może być dużą zaletą w niektórych aplikacjach, jak np. produkcja elementów wypełnień czy opakowań jednorazowych.
Czy tworzywa EPP, EPS, RELOOPP® CELOOPS i NEOPS® nadają się do recyklingu?
Tak, wszystkie te materiały w pełni nadają się do recyklingu, choć procesy ich wtórnego przetwarzania mogą się od siebie różnić. W przypadku EPP (spieniony polipropylen) materiał jest najpierw rozdrabniany, a następnie topiony i formowany w nowe produkty. Proces ten może być wykorzystywany do produkcji materiałów takich jak RELOOPP® (EPP z zawartością z recyklingu), który również w pełni nadaje się do recyklingu. Proces recyklingu EPS (i jego bardziej zrównoważonych alternatyw – NEOPS® i CELOOPS) wygląda podobnie, jednak przed rozdrobnieniem wymaga on opróżnienia z powietrza. Pomimo tego, że jest to nieco bardziej uciążliwe, proces ten jest w pełni dopracowany i z powodzeniem stosowany przez wiele firm zajmujących się recyklingiem. Uzyskany w ten sposób wysokiej jakości surowiec jest ponownie wykorzystywany do izolacji termicznej i pakowania. Materiały zostały zaprojektowane z myślą o zrównoważonym rozwoju i gospodarce o obiegu zamkniętym.
W jaki sposób zastosowanie lekkich tworzyw sztucznych wpływa na efektywność pojazdów?
Zastosowanie lekkich, spienionych tworzyw sztucznych wpływa na efektywność pojazdów na wiele sposobów. Przede wszystkim obniżają one ich masę własną. Lżejsze samochody zużywają mniej paliwa, a jeśli są zasilane energią elektryczną – są w stanie pokonać więcej kilometrów na jednym ładowaniu oraz są tańsze w eksploatacji. Spienione tworzywa sztuczne cechują się ponadto lepszą izolacyjnością cieplną niż tradycyjne materiały, co poprawia efektywność działania systemów klimatyzacji i ogrzewania. Materiały, takie jak EPP czy RELOOPP® są ponadto wytrzymałe i odporne na odkształcenia, dzięki czemu doskonale nadają się do zastosowania w elementach pochłaniających energię w razie kolizji, takich jak zderzaki czy zagłówki. Co więcej, zrównoważone tworzywa sztuczne, takie jak CELOOPS i RELOOPP®, są wykonane z surowców pochodzących z recyklingu i NEOPS® w oparciu o zasadę bilansu masy, która promuje gospodarkę o obiegu zamkniętym i poprawia ekologiczność samochodów.
Jakie komponenty samochodowe można wykonać z EPP, a jakie z EPS?
Zarówno EPP (spieniony polipropylen), jak i EPS (spieniony polistyren) można znaleźć w projektach samochodów; jednak ich różne właściwości mechaniczne wpływają na obszary ich zastosowania. EPP posiada tzw. pamięć kształtu – jest odporny na odkształcenia i wielokrotne uderzenia, co czyni go bardziej uniwersalnym. Dzięki tej właściwości jest wykorzystywany do produkcji zderzaków i elementów pochłaniających uderzenia, takich jak zagłówki, podłokietniki i panele drzwiowe. Nadaje się również do systemów izolacji akumulatorów w pojazdach elektrycznych, ze względu na swoją odporność na wysokie temperatury i właściwości elektrostatyczne. Z drugiej strony EPS jest lżejszy i nieco mniej odporny na uderzenia, dzięki czemu nadaje się do mniej wymagających zastosowań, takich jak panele wypełniające deskę rozdzielczą i konstrukcje podłogowe, izolacja w systemach klimatyzacji, a także opakowania transportowe dla części samochodowych.