En agosto de 1941, Henry Ford presentaba el “Soybean Car” en el festival anual Dearborn Days, en Michigan (EEUU). Es el primer coche fabricado con plástico. La estructura de acero estaba cubierta con 14 paneles de un plástico cuya fórmula se desconoce, aunque se cree que incluía fibra de soja mezclada con resina felónica. El coche pesaba unos 900 kg, 450 menos que el peso medio de los vehículos fabricados íntegramente con acero. El estallido de la II Guerra Mundial provocó el abandono de un proyecto que el pionero de la industria de la automoción confiaba en que tendría éxito.
En la actualidad, el plástico representa aproximadamente la mitad del volumen de cualquier automóvil estándar y un tercio del total de las piezas que lo componen, cantidades que irán en aumento en los próximos años debido a los esfuerzos de los fabricantes por reducir el peso y mejorar la eficiencia en el consumo de combustible.
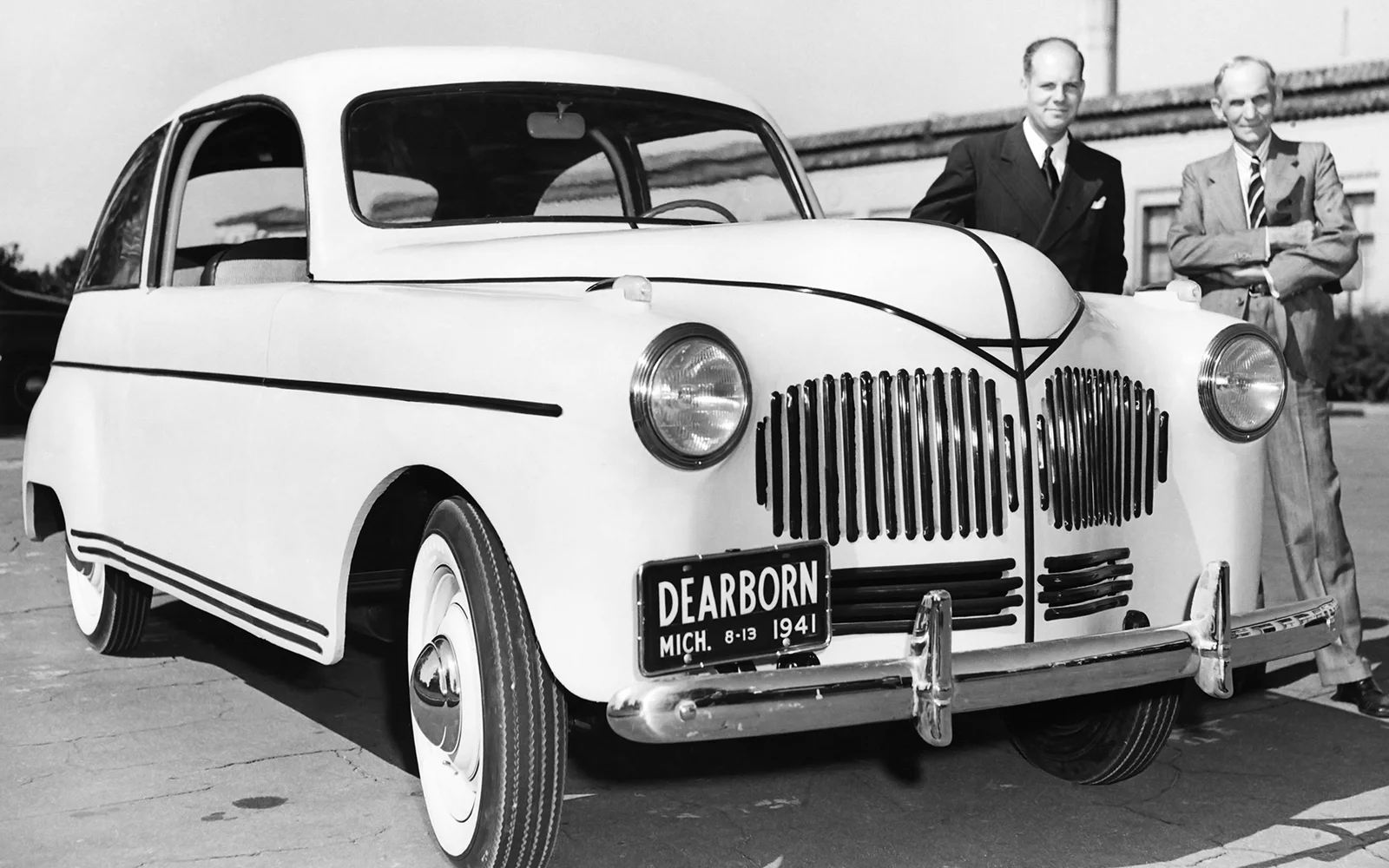
Sorprende descubrir experimentos como el de Ford tantos años después, aunque su Soybean Car no es un ejemplo aislado en la historia de la automoción. Aquel no dejaba de ser un vehículo conceptual, pues nunca llegó a producirse en serie; en cambio, en la antigua República Federal Alemana sí existió un coche de plástico fabricado de forma masiva. Se trata del Trabant, modelo de la marca VEB Sachsenring Automobilwerke Zwickau, que estaba formado en su mayor parte por un plástico duro llamado Duroplast. Se componía de materiales reciclados provenientes de la Unión Soviética, como fibras de algodón, resinas sintéticas y trapos. Estuvo en producción desde 1957 hasta 1990.
EPP y EPS en la automoción
Hoy en día, el plástico es indispensable para todas las marcas. Los termoplásticos moldeados, como el polipropileno expandido (EPP) y el poliestireno expandido (EPS), constituyen el elemento fundamental en los sistemas de seguridad pasiva de los vehículos, como los parachoques que fabrica Knauf Industries Automotive. Pero no sólo eso, pues sus numerosas propiedades los hacen adecuados para asumir cualquier función en el ecosistema del vehículo, ya sea en el chasis, en la carrocería, como accesorio interno o externo.
Con las regulaciones gubernamentales respecto a las emisiones de gases contaminantes y consumo de combustibles fósiles, tanto los fabricantes de automóviles como los proveedores de componentes invierten en sus departamentos de I+D+I para conseguir nuevos materiales mediante la combinación de plásticos y otros materiales ligeros que sustituyan las piezas metálicas, más pesadas y menos eficientes en términos de consumo energético y seguridad.
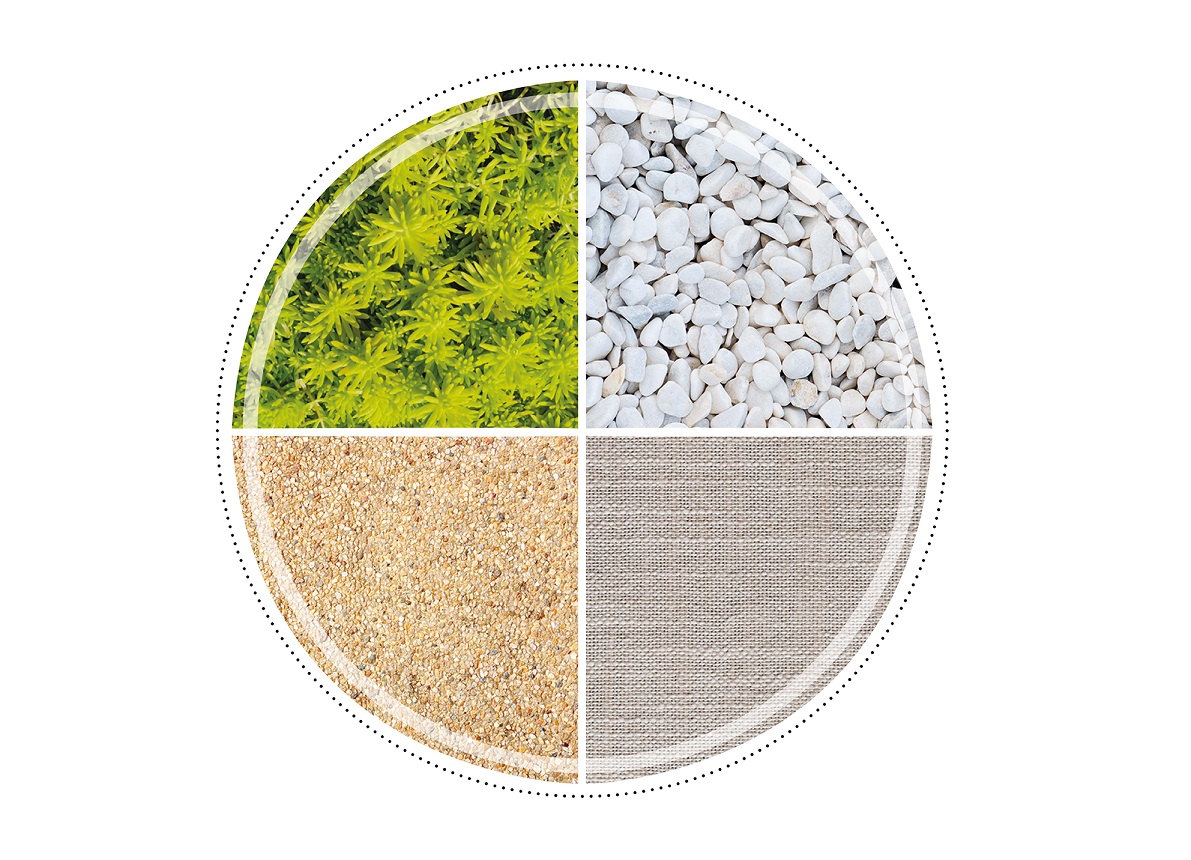
A través de su departamento de innovación y desarrollo, Knauf Industries Automotive aporta soluciones que amplían las aplicaciones de las piezas de EPP y su atractivo para los fabricantes. Como la nueva paleta de 36 texturas para superficies de polipropileno expandido, que mediante el desarrollo de tecnologías digitales son una alternativa atractiva a las piezas tradicionales de espuma, y responden a las últimas tendencias en diseño industrial.
Todas las grandes marcas apuestan por los polímeros, y además, de acuerdo con la creciente concienciación medioambiental, anuncian planes para aumentar el uso de plásticos reciclados en sus coches. Es el caso de Ford, que incluye en cada vehículo el equivalente a 250 botellas recicladas, y que fabrica unas 300 piezas con materiales renovables, entre ellos, alfombras de avión.
El Nissan Leaf está compuesto en un 25% por material reciclado (botellas para los asientos, tela para las almohadillas y componentes electrónicos reutilizados); el Prius de Toyota y el Soul EV de Kia llevan cojines de asiento y otras partes hechas con bioplásticos; y en la misma línea se encuentra el Jeep Grand Cherokee.
Volvo se comprometió en 2018 a fabricar el 25% de los plásticos de sus coches nuevos con materiales reciclados a partir de 2025. El SUV híbrido XC60 T8 es el primer resultado de ese anuncio, pues los asientos están hechos de botellas de plástico y redes de pesca reciclados, mientras que parte del maletero es el resultado de reciclar botes de kétchup y de champú.
General Motors utiliza las botellas de plástico para las cubiertas insonorizantes del motor del Chevrolet Equinox, y tapones de plástico reciclados para las cubiertas del radiador del GMC Sierra. Honda utiliza el plástico reciclado en el asiento del Acura y recicla parachoques para transformarlos en guardabarros y en protectores contra las salpicaduras. Ejemplos parecidos podríamos enumerar de Volkswagen, Chrysler, Renault, etc.
¿Cuáles son los coches con más plástico?
Las diferencias en cuanto al uso de componentes plásticos entre las principales marcas son pequeñas. Para hallar ejemplos que realmente llamen la atención, nos tenemos que fijar en vehículos más sencillos y de menor tamaño, como el Birò O2 de Estrima. Se trata de un scooter eléctrico de cuatro ruedas para un solo pasajero. Es 100% eléctrico, con batería extraíble, y está fabricado en más de un 80% con plástico. Sólo el chasis es metálico. Todo el exterior, los paneles frontal y trasero y el capó son de plástico reciclado.
El O2 es fruto de la colaboración entre Estrima y Mandalaki Studio, que se encargó de recuperar objetos para el mantenimiento de carreteras, como carteles y conos, y los trituró hasta convertirlos en polvo fino, que es la materia prima para moldear por rotación los componentes del vehículo. Los asientos, el tacómetro, el volante y las puertas están fabricados con plásticos no reciclados, como el PVC termoformado.
El O2 se comercializa, pero existen otros proyectos conceptuales que apuestan por el plástico como material principal para la fabricación de coches. Es el caso de Luca, una idea del equipo ecomotor de la Universidad Tecnológica de Eindhoven, que pretenden que sea una realidad a mitad de año. Usa compuestos de base biológica que incluyen desechos plásticos recuperados del océano. El chasis se ha proyectado en PET reciclado intercalado entre capas externas de lino. La carrocería se formará con un nuevo material que combinará un aditivo derivado de residuos domésticos con polipropileno reciclado.
En 2013, Toyota presentaba el modelo ME.WE, un coche conceptual que simplificaba en todo lo posible para maximizar la comodidad, abaratar costes y reducir la huella ecológica. Sustituía los materiales utilizados tradicionalmente en el sector automoción por otros más ligeros y sostenibles, como el EPP. Incorporaba paneles intercambiables (puertas, capó, aletas, parachoques) sobre una estructura tubular de aluminio. Mediante estos componentes, 100% reciclables, Toyota lograba reducir el peso hasta un 20%, dejándolo en solo 750 kg.