El desarrollo de la industria automotriz se dirige de modo irreversible hacia la electromovilidad. La demanda social de este tipo de vehículos crece, y los diseñadores trabajan continuamente para mejorar la fabricación y el diseño de los coches eléctricos. Las piezas fabricadas con modernos plásticos juegan un papel importante en este proceso, puesto que permiten mejorar una serie de especificaciones en los coches de accionamiento eléctrico.
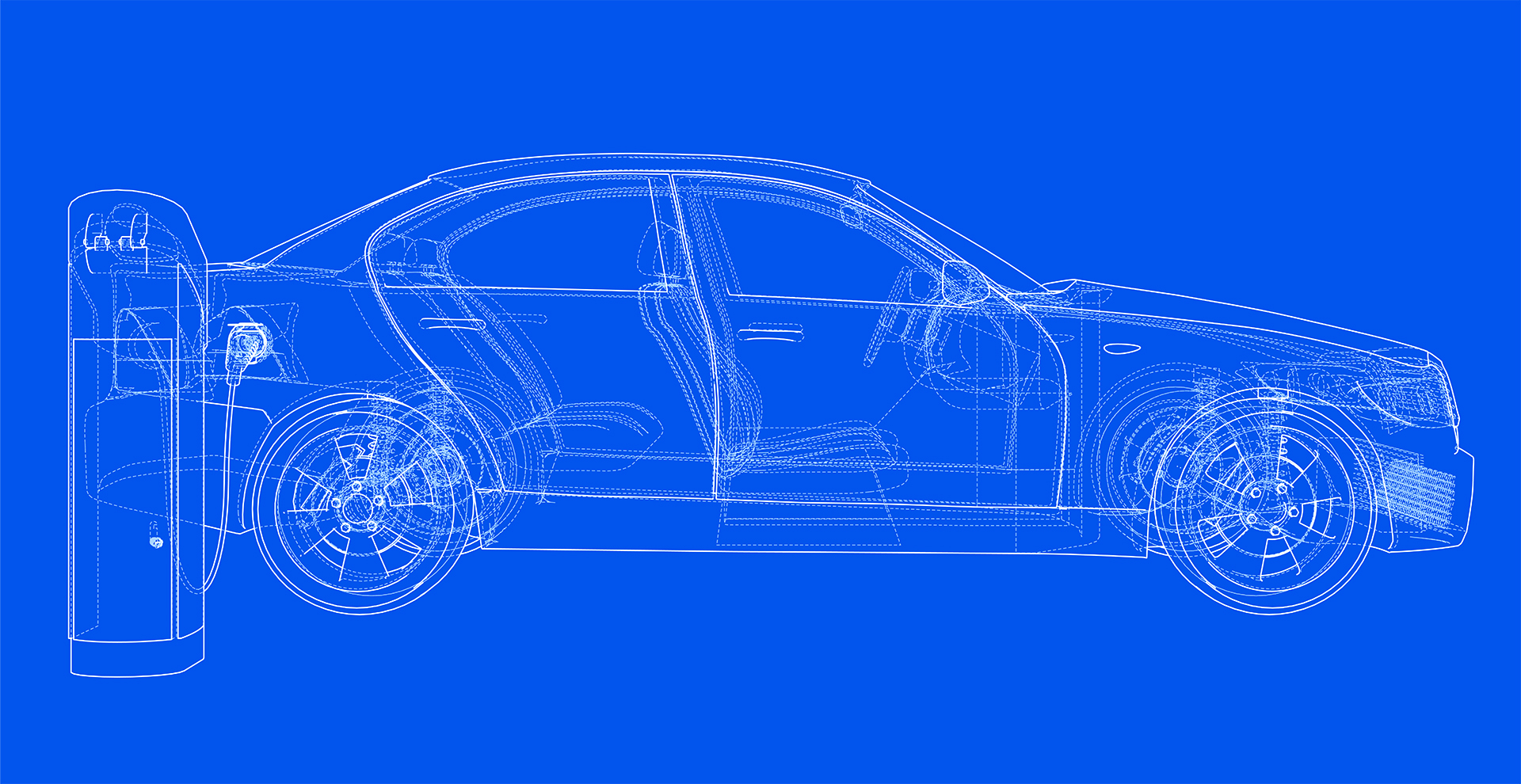
La industria automotriz está experimentando un proceso de electrificación. Actualmente los coches eléctricos constituyen alrededor del 6% del total de ventas en quince países de la Unión Europea, y la demanda evoluciona de forma ascendente. Alemania y Noruega lideran esta tendencia: en el primer semestre de 2019 se matricularon, respectivamente, 48.000 y 44.000 vehículos de este tipo. Las normas de emisión cada vez más rigurosas y las declaraciones que apuntan a una retirada de los vehículos con motores tradicionales de las grandes ciudades son el trasfondo de este cambio revolucionario en el sector automoción. Londres, Hamburgo y París están entre las ciudades posicionadas en esta línea. En Polonia, a comienzos de 2018 entró en vigor la Ley de Electromovilidad, que da a los gobiernos locales la capacidad de crear zonas de bajas emisiones. Las medidas a favor del medio ambiente y la homologación de los coches eléctricos siguen en aumento, aunque algunos observadores afirman que la propagación de los coches eléctricos en el continente europeo podría ser mayor. En este sentido, China ejerce un papel de liderazgo. En la primera mitad de 2019 se matricularon en el país asiático 628.000 coches enchufables, catorce veces más que en Europa.
El futuro de los coches eléctricos: barreras
Uno de los problemas que la industria automotriz debe resolver es el rango relativamente bajo de coches eléctricos y el miedo de los usuarios a que la batería se descargue durante su viaje. Otro obstáculo es la dificultad para acceder a los puntos de carga de los coches eléctricos: en España existen en torno a 4.500 puntos de recarga, cifra que se sitúa por debajo de las que presentan países como Holanda, Francia y Alemania. Sin embargo, el desarrollo tecnológico y las numerosas inversiones que se están realizando indican que estas limitaciones desaparecerán del todo próximamente. En paralelo, los fabricantes de coches eléctricos también se han puesto manos a la obra con el fin de reducir el peso total de los vehículos hasta un 50%, lo que permitirá reducir la potencia del motor y, como resultado, el consumo de energía necesario para accionarlo.
Otra preocupación habitual acerca de los coches eléctricos está relacionada con el confort de la conducción, que surge del propio diseño de los vehículos enchufables. Por ejemplo, el motor eléctrico del coche, en contraste con un motor de combustión tradicional, no emite calor, lo cual puede dificultar el mantenimiento de una temperatura confortable dentro de él durante el invierno en el caso de se apliquen soluciones de diseño inadecuadas dentro de la cabina. Las piezas de coche ultraligeras fabricadas con plásticos expandidos que ofrecen propiedades de aislamiento térmico permiten eliminar muchas de estas limitaciones, tal y como ocurre con el polipropileno expandido (EPP) y el poliestireno expandido (EPS) procesados en la planta de Knauf Industries en Mszczonów.
Retos para los fabricantes de coches eléctricos y nuevas aplicaciones de las piezas de plástico
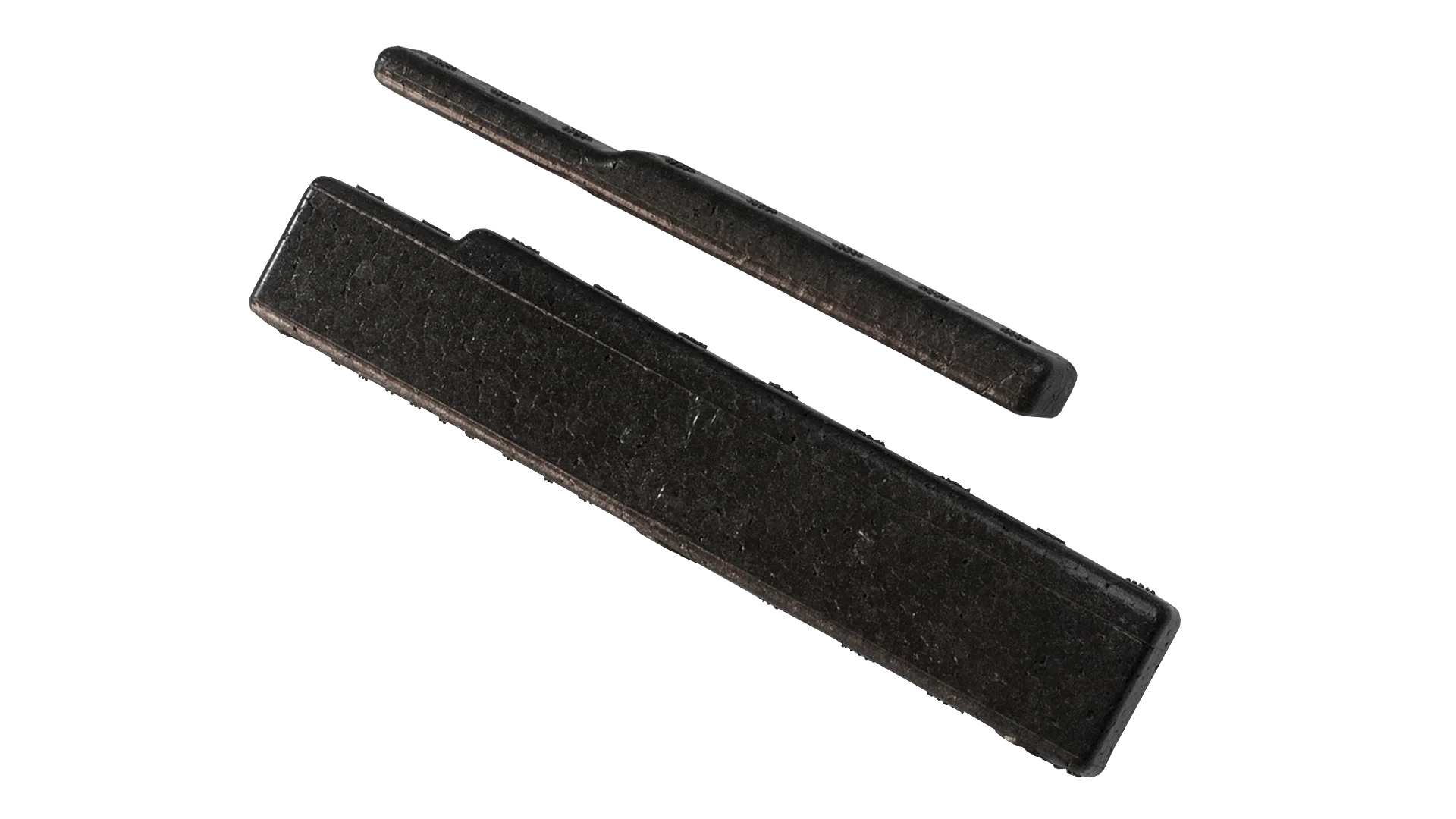
Podría parecer que los plásticos de los coches eléctricos desempeñan el mismo papel que en los coches tradicionales con motor de combustión. Es decir, reducir su peso y, al mismo tiempo, garantizar la resistencia adecuada de toda la estructura. Hace algún tiempo, las piezas de automóvil fabricadas con el método de inyección termoplástica permitían ‘adelgazar’ la silueta de los vehículos, por ejemplo, sustituyendo los parachoques metálicos macizos y el cristal de las pantallas de iluminación. Al mismo tiempo, la aplicación de plásticos expandidos en interiores permitió la protección acústica de la cabina y amortiguar las vibraciones. En los coches eléctricos, la demanda de piezas fabricadas con espuma – EPP y EPS – seguirá creciendo, aunque solo sea por la necesidad de aplicar un aislamiento térmico adicional en el techo y las puertas que impida el enfriamiento del interior del coche. Las propiedades aislantes de estos plásticos también permiten proteger la batería contra los cambios de temperatura demasiado repentinos que podrían causar su fallo. Sin embargo, si nos fijamos en el diseño de un coche eléctrico paso a paso, comprobamos que los plásticos elásticos y fáciles de moldear pueden ayudar a hacer cambios mucho más profundos en su aspecto.
También te puede interesar: Industria del automóvil – fabricación de componentes de vehículos a partir de materias primas inocuas para el medio ambiente
El mercado de los coches eléctricos del futuro
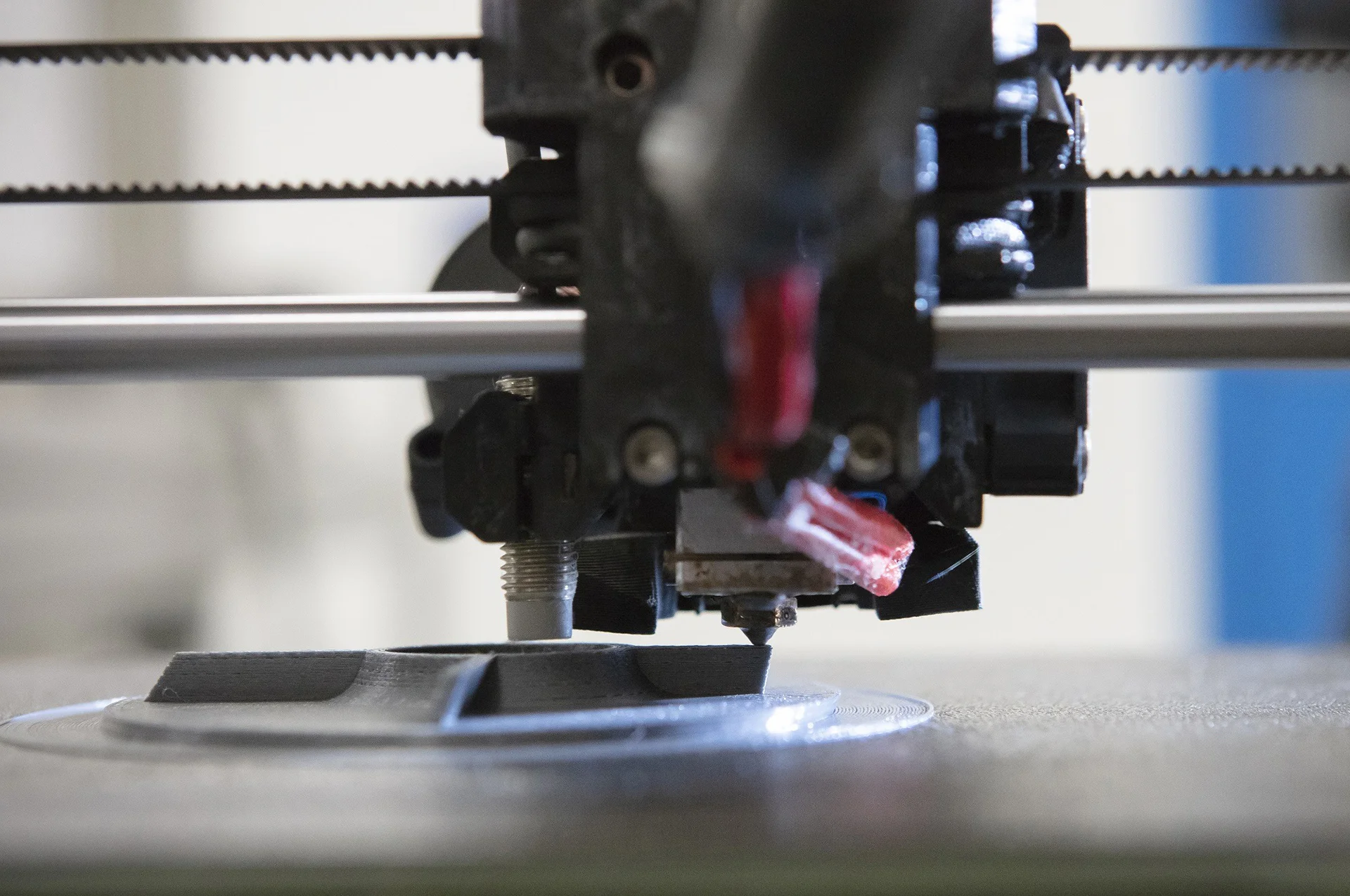
Por ahora, las versiones eléctricas de los coches insignia de las grandes marcas automovilísticas mundiales como Mercedes, Audi, Hyundai o Kia solo se distinguen de las que tienen motores de combustión por detalles menores como son la ausencia del tubo de escape o la incorporación de una cámara en lugar de un espejo lateral. Pero las diferencias que se están gestando son mucho más profundas y pueden cambiar completamente el diseño de los coches eléctricos en el futuro. Sobre todo, porque el tradicional motor grande y el sistema de accionamiento ya no ocupan tanto espacio en un coche eléctrico. Un accionamiento eléctrico es mucho más pequeño y no requiere una refrigeración tan intensa. Además, el suelo de un coche eléctrico puede ser completamente plano y las ruedas pueden disponer de un espacio más amplio. Esto ofrece posibilidades totalmente nuevas para el diseño de interiores y de maleteros. La rejilla tradicional, que ahora suele sustituirse por un simulador, desaparecerá con el tiempo. Asimismo, los plásticos desempeñarán un importante papel en la introducción de nuevas soluciones en el ámbito de la funcionalidad y el diseño de los coches eléctricos. Gracias a los modernos métodos de procesamiento que utilizamos, como el sobremoldeo, podemos superar las dificultades en términos económicos para fabricar componentes funcionales compuestos de múltiples materiales. ¡Esperamos con impaciencia la llegada de estos proyectos innovadores!