La generalización del uso de los materiales plásticos en la industria de la automoción no solo está permitiendo fabricar vehículos más ligeros y más eficientes en el consumo de energía, sino que también los está haciendo más seguros. A medida que los fabricantes perfeccionan los diseños e incorporan nuevos materiales, se desmontan prejuicios como el de que “cuanto más rígido, más seguro”. Y en ello, el papel de termoplásticos como el polipropileno expandido (EPP) y el poliestireno expandido (EPS) es fundamental.
“Los coches de antes eran mucho más resistentes; ahora se abollan al mínimo impacto”. Relacionar seguridad con solidez, con chapas metálicas indeformables, de formas angulosas, sin presencia de plástico, es un prejuicio sin fundamento. Porque lo que un vehículo debe garantizar es la seguridad de sus ocupantes, y para ello, lo que debe ser indeformable es el habitáculo.
Hasta la década de 1950, los fabricantes de coches apenas se preocupaban por investigar cómo mejorar la seguridad de los pasajeros. Se consideraba que cuanto más rígido era el automóvil, mejor los protegía. Hasta que Mercedes-Benz empezó a hacer pruebas con maniquíes y descubrió que introduciendo zonas de absorción de impactos la gravedad de las colisiones se reducía.
Cuando se produce una colisión, si los elementos de la carrocería presentan una gran resistencia a la deformación, la energía cinética se traslada al interior del habitáculo, y son las personas quienes la absorben. En cambio, si la zona del impacto se “arruga”, absorbe una gran cantidad de energía y, por tanto, reduce las consecuencias para los ocupantes.
El plástico salva vidas
La introducción de los componentes plásticos en los elementos de seguridad pasiva supuso una revolución para la protección de las personas. Un estudio de la Administración Nacional de Seguridad de Tráfico en Carreteras (NHTSA) del gobierno de Estados Unidos determinó en 2015 que las tecnologías innovadoras de seguridad, muchas de las cuales incluían el uso de plásticos y compuestos, salvaron más de 600 000 vidas entre 1960 y 2012 en el país norteamericano.
El uso de plástico en los paneles exteriores es determinante en la absorción de los golpes. Además, aligera el peso de los coches, otra de las variables a tener en cuenta en cuanto a la mejora de la seguridad, puesto que a mayor peso más energía cinética y, por tanto, consecuencias más graves en caso de accidente.
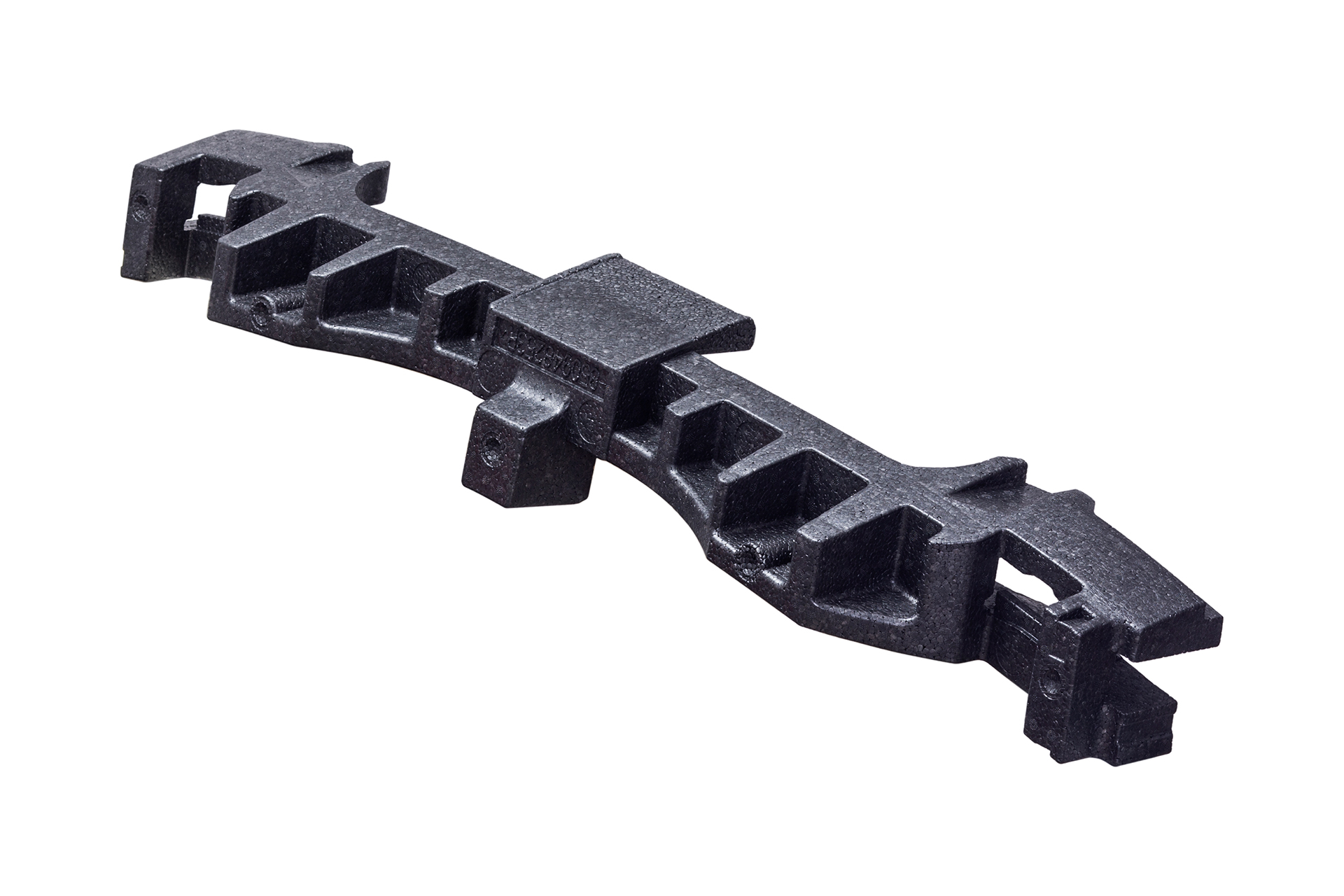
En Knauf Industries Automotive fabricamos piezas de EPP y EPS, como parachoques delanteros y traseros, parrillas y amortiguadores de parachoques, que constituyen la primera línea de defensa en caso de colisión. Las cualidades de estos materiales plásticos, mucho más ligeros y flexibles que los tradicionalmente utilizados en la industria automotriz, les confieren una capacidad de absorción de energía hasta cinco veces superior.
Cuando se produce el impacto, los componentes plásticos absorben la energía, creando una zona “arrugada”, que colapsa como un acordeón, y actúa como cojín protector para los ocupantes del coche. Estas mismas propiedades actúan como elemento protector para los peatones, pues no es lo mismo impactar contra un parachoques metálico que contra uno compuesto en un 98% por aire, como ocurre con el EPP.
Pero no solo encontramos EPP y EPS en los elementos de seguridad pasiva exterior, sino también en el habitáculo: asientos, revestimiento de volante, almohadillas para las rodillas, revestimiento de puertas, etc.
Los reposacabezas, por ejemplo, aparecieron a mediados de los años 50 como un elemento de lujo. En 1969 ya eran obligatorios para todos los vehículos matriculados en EEUU, pero en España no se no se empezaron a homologar hasta la última década del siglo pasado. Fabricado con EPP, se trata de un elemento de seguridad fundamental para reducir las consecuencias de una colisión en las cervicales.
El informe del Instituto de Seguros para la Seguridad Vial estadounidense señalaba en 2017 que las muertes de conductores cayeron de 87 por millón a 30 por millón entre 2002 y 2015 gracias a las mejoras en la seguridad de los automóviles.
EPP para la seguridad infantil
Entre estos avances cabe destacar, por último, los referidos a la seguridad infantil. Las primeras sillitas para niños, muy rudimentarias, aparecieron en 1930. Entonces, su función básicamente era evitar las distracciones al conductor. No fue hasta la década de los sesenta que se fabricaron las primeras sillitas con elementos de seguridad, cuyo uso se generalizaría en los ochenta. En España, sin embargo, aún tendrían que pasar unos cuantos años —hasta su obligatoriedad en 2005— para que la gran mayoría de niños dispusieran de una medida de seguridad que ha salvado miles de vidas, y cuyo elemento principal es el polipropileno expandido.
Las sillas de coche infantiles que fabrica Knauf Industries Automotive con EPP son ligeras, fuertes y resistentes a altas cargas en el tiempo. Absorben muy bien la energía cinética, sin sufrir deformaciones incluso después de varios impactos.
La seguridad es una de las áreas en evolución permanente dentro de la industria de la automoción. Los avances en las últimas décadas han sido espectaculares, y la investigación continúa para sacar todo el provecho a las cualidades de los nuevos materiales.